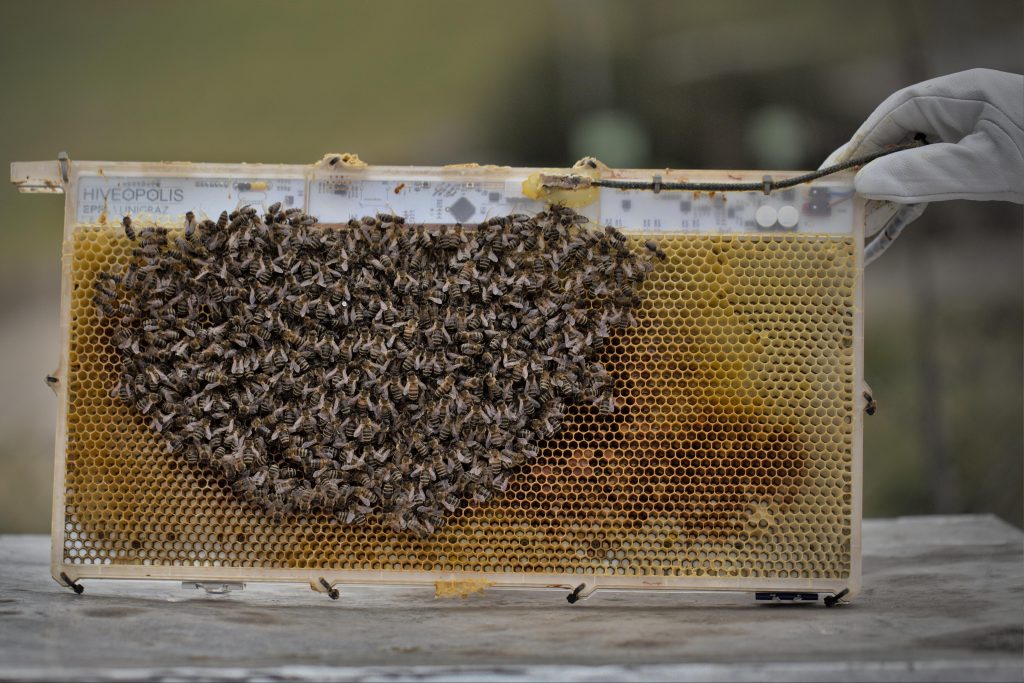
The robotic system is shown in an experimental hive © Artificial Life Lab/U. of Graz/Hiveopolis
By Celia Luterbacher
Honeybees are famously finicky when it comes to being studied. Research instruments and conditions and even unfamiliar smells can disrupt a colony’s behavior. Now, a joint research team from the Mobile Robotic Systems Group in EPFL’s School of Engineering and School of Computer and Communication Sciences and the Hiveopolis project at Austria’s University of Graz have developed a robotic system that can be unobtrusively built into the frame of a standard honeybee hive.
Composed of an array of thermal sensors and actuators, the system measures and modulates honeybee behavior through localized temperature variations.
“Many rules of bee society – from collective and individual interactions to raising a healthy brood – are regulated by temperature, so we leveraged that for this study,” explains EPFL PhD student Rafael Barmak, first author on a paper on the system recently published in Science Robotics. “The thermal sensors create a snapshot of the bees’ collective behavior, while the actuators allow us to influence their movement by modulating thermal fields.”
“Previous studies on the thermal behavior of honeybees in winter have relied on observing the bees or manipulating the outside temperature,” adds Martin Stefanec of the University of Graz. “Our robotic system enables us to change the temperature from within the cluster, emulating the heating behavior of core bees there, and allowing us to study how the winter cluster actively regulates its temperature.”
A ‘biohybrid superorganism’ to mitigate colony collapse
Bee colonies are challenging to study in winter since they are sensitive to cold, and opening their hives risks harming them in addition to influencing their behavior. But thanks to the researchers’ biocompatible robotic system, they were able to study three experimental hives, located at the Artificial Life Lab at the University of Graz, during winter and to control them remotely from EPFL. Inside the device, a central processor coordinated the sensors, sent commands to the actuators, and transmitted data to the scientists, demonstrating that the system could be used to study bees with no intrusion – or even cameras – required.
Mobile Robotic Systems Group head Francesco Mondada explains that one of the most important aspects of the system – which he calls a ‘biohybrid superorganism’ for its combination of robotics with a colony of individuals acting as a living entity – is its ability to simultaneously observe and influence bee behavior.
“By gathering data on the bees’ position and creating warmer areas in the hive, we were able to encourage them to move around in ways they would never normally do in nature during the winter, when they tend to huddle together to conserve energy. This gives us the possibility to act on behalf of a colony, for example by directing it toward a food source, or discouraging it from dividing into too-small groups, which can threaten its survival.”
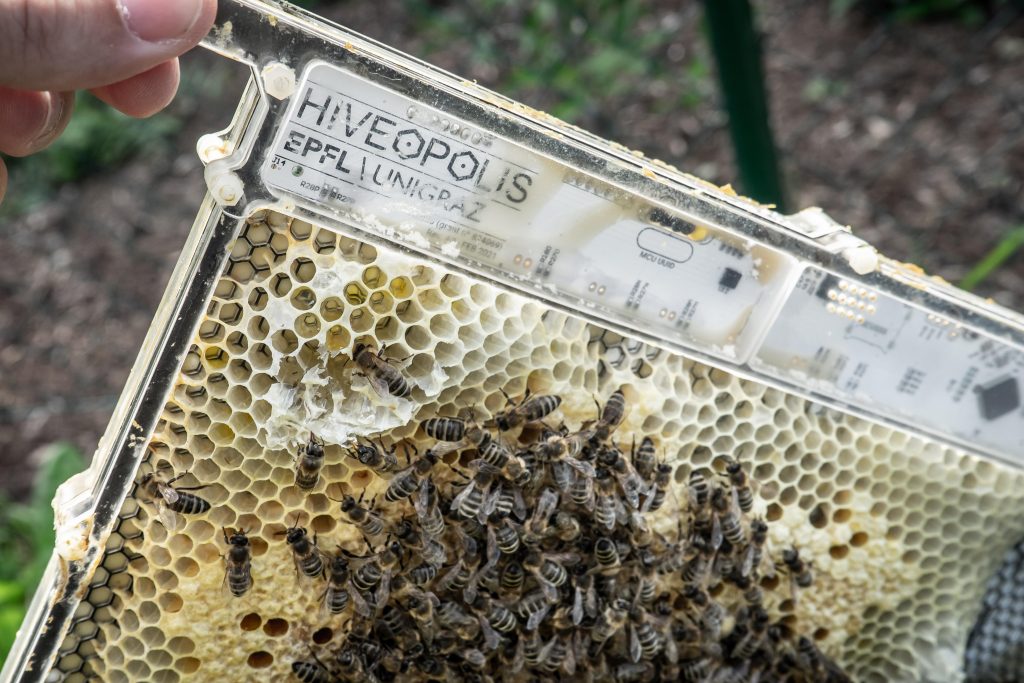
The robotic system is shown in an experimental hive © MOBOTS / EPFL / Hiveopolis
The scientists were able to prolong the survival of a colony following the death of its queen by distributing heat energy via the actuators. The system’s ability to mitigate colony collapse could have implications for bee survivability, which has become a growing environmental and food security concern as the pollinators’ global populations have declined.
Never-before-seen behaviors
In addition to its potential to support colonies, the system has shed light on honeybee behaviors that have never been observed, opening new avenues in biological research.
“The local thermal stimuli produced by our system revealed previously unreported dynamics that are generating exciting new questions and hypotheses,” says EPFL postdoctoral researcher and corresponding author Rob Mills. “For example, currently, no model can explain why we were able to encourage the bees to cross some cold temperature ‘valleys’ within the hive.”
The researchers now plan to use the system to study bees in summertime, which is a critical period for raising young. In parallel, the Mobile Robotic Systems Group is exploring systems using vibrational pathways to interact with honeybees.
“The biological acceptance aspect of this work is critical: the fact that the bees accepted the integration of electronics into the hive gives our device great potential for different scientific or agricultural applications,” says Mondada.
This work was supported by the EU H2020 FET project HIVEOPOLIS (no. 824069), coordinated by Thomas Schmickl, and by the Field of Excellence COLIBRI (Complexity of Life in basic Research and Innovation) at the University of Graz.