AI, robotics, automation: The fourth industrial revolution is here
Army looks for a few good robots, sparks industry battle
#276: IROS 2018 Exhibition (Part 2 of 3), with Kristoffer Richardsson, Michael Zillich and Paulo Alvito
In this interview, Audrow Nash interviews Kristoffer Richardsson, Michael Zillich, and Paulo Alvito.
Kristoffer Richardsson, Developer at Bitcraze in Sweden, speaks about small open-source unmanned aerial vehicle and different ways of localizing them.
Michael Zillich, CTO of Blue Danube Robotics in Austria, discusses a robotics platform for picking up toys, called Kenny. Zillich talks about Kenny’s design, including sensors and its robotic arm. He discusses how children can show the robot where to put specific toys, about how this large European project was coordinated, and about possibly commercializing this platform.
Paulo Alvito, CEO and CTO and Co-founder of IDMind in Portugal, discusses remote inspection robot for sewers. Alvito discusses what it means to be remotely autonomous, the design of the robot, and how these robots communicate data.
Links
Top Article for 2018 – How Artificial Intelligence and Robotics Can Create More Employment Opportunities
Top Article for 2018 – Here Are All the Companies Testing Autonomous Cars In 2018
Top Article for 2018 – Smart Cities are the Future
Holiday robot videos 2018 – part 3
Holiday robot videos 2018 – part 2
Happy holidays everyone! Here are some more robot videos to get you into the holiday spirit.
Have a last minute holiday robot video of your own that you’d like to share? Send your submissions to sabine.hauert@robohub.org. Read More
Robots with sticky feet can climb up, down, and all around
By Lindsay Brownell
Jet engines can have up to 25,000 individual parts, making regular maintenance a tedious task that can take over a month per engine. Many components are located deep inside the engine and cannot be inspected without taking the machine apart, adding time and costs to maintenance. This problem is not only confined to jet engines, either; many complicated, expensive machines like construction equipment, generators, and scientific instruments require large investments of time and money to inspect and maintain.
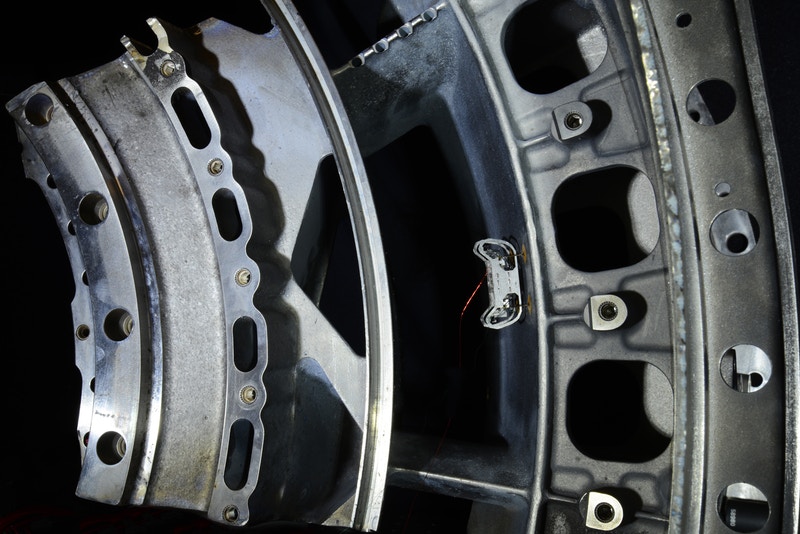
Researchers at Harvard University’s Wyss Institute for Biologically Inspired Engineering and John A. Paulson School of Engineering and Applied Sciences (SEAS) have created a micro-robot whose electroadhesive foot pads, origami ankle joints, and specially engineered walking gait allow it to climb on vertical and upside-down conductive surfaces, like the inside walls of a commercial jet engine. The work is reported in Science Robotics.
“Now that these robots can explore in three dimensions instead of just moving back and forth on a flat surface, there’s a whole new world that they can move around in and engage with,” said first author Sébastien de Rivaz, a former Research Fellow at the Wyss Institute and SEAS who now works at Apple. “They could one day enable non-invasive inspection of hard-to-reach areas of large machines, saving companies time and money and making those machines safer.”
The new robot, called HAMR-E (Harvard Ambulatory Micro-Robot with Electroadhesion), was developed in response to a challenge issued to the Harvard Microrobotics Lab by Rolls-Royce, which asked if it would be possible to design and build an army of micro-robots capable of climbing inside parts of its jet engines that are inaccessible to human workers. Existing climbing robots can tackle vertical surfaces, but experience problems when trying to climb upside-down, as they require a large amount of adhesive force to prevent them from falling.
The team based HAMR-E on one of its existing micro-robots, HAMR, whose four legs enable it to walk on flat surfaces and swim through water. While the basic design of HAMR-E is similar to HAMR, the scientists had to solve a series of challenges to get HAMR-E to successfully stick to and traverse the vertical, inverted, and curved surfaces that it would encounter in a jet engine.
First, they needed to create adhesive foot pads that would keep the robot attached to the surface even when upside-down, but also release to allow the robot to “walk” by lifting and placing its feet. The pads consist of a polyimide-insulated copper electrode, which enables the generation of electrostatic forces between the pads and the underlying conductive surface. The foot pads can be easily released and re-engaged by switching the electric field on and off, which operates at a voltage similar to that required to move the robot’s legs, thus requiring very little additional power. The electroadhesive foot pads can generate shear forces of 5.56 grams and normal forces of 6.20 grams – more than enough to keep the 1.48-gram robot from sliding down or falling off its climbing surface. In addition to providing high adhesive forces, the pads were designed to be able to flex, thus allowing the robot to climb on curved or uneven surfaces.
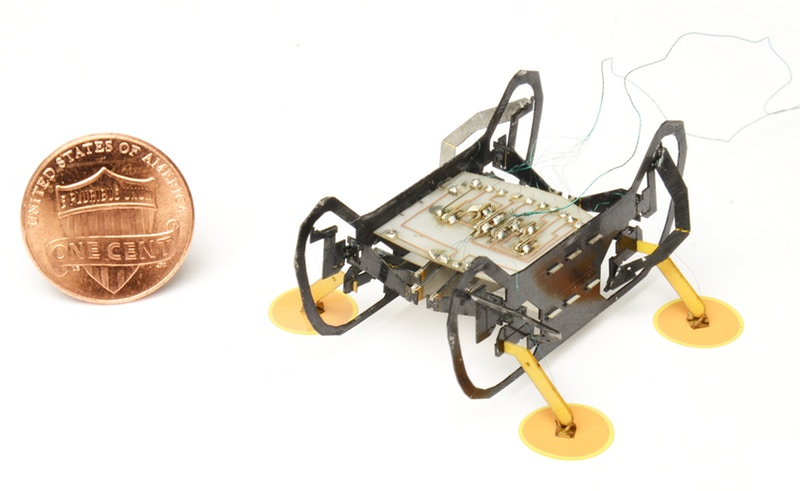
The scientists also created new ankle joints for HAMR-E that can rotate in three dimensions to compensate for rotations of its legs as it walks, allowing it to maintain its orientation on its climbing surface. The joints were manufactured out of layered fiberglass and polyimide, and folded into an origami-like structure that allows the ankles of all the legs to rotate freely, and to passively align with the terrain as HAMR-E climbs.
Finally, the researchers created a special walking pattern for HAMR-E, as it needs to have three foot pads touching a vertical or inverted surface at all times to prevent it from falling or sliding off. One foot releases from the surface, swings forward, and reattaches while the remaining three feet stay attached to the surface. At the same time, a small amount of torque is applied by the foot diagonally across from the lifted foot to keep the robot from moving away from the climbing surface during the leg-swinging phase. This process is repeated for the three other legs to create a full walking cycle, and is synchronized with the pattern of electric field switching on each foot.
When HAMR-E was tested on vertical and inverted surfaces, it was able to achieve more than one hundred steps in a row without detaching. It walked at speeds comparable to other small climbing robots on inverted surfaces and slightly slower than other climbing robots on vertical surfaces, but was significantly faster than other robots on horizontal surfaces, making it a good candidate for exploring environments that have a variety of surfaces in different arrangements in space. It is also able to perform 180-degree turns on horizontal surfaces.
HAMR-E also successfully maneuvered around a curved, inverted section of a jet engine while staying attached, and its passive ankle joints and adhesive foot pads were able to accommodate the rough and uneven features of the engine surface simply by increasing the electroadhesion voltage.
This iteration of HAMR-E is the first and most convincing step towards showing that this approach to a centimeter-scale climbing robot is possible, and that such robots could in the future be used to explore any sort of infrastructure, including buildings, pipes, engines, generators, and more
ROBERT WOOD
The team is continuing to refine HAMR-E, and plans to incorporate sensors into its legs that can detect and compensate for detached foot pads, which will help prevent it from falling off of vertical or inverted surfaces. HAMR-E’s payload capacity is also greater than its own weight, opening the possibility of carrying a power supply and other electronics and sensors to inspect various environments. The team is also exploring options for using HAMR-E on non-conductive surfaces.
“This iteration of HAMR-E is the first and most convincing step towards showing that this approach to a centimeter-scale climbing robot is possible, and that such robots could in the future be used to explore any sort of infrastructure, including buildings, pipes, engines, generators, and more,” said corresponding author Robert Wood, Ph.D., who is a Founding Core Faculty member of the Wyss Institute as well as the Charles River Professor of Engineering and Applied Sciences at SEAS.
“While academic scientists are very good at coming up with fundamental questions to explore in the lab, sometimes collaborations with industrial scientists who understand real-world problems are required to develop innovative technologies that can be translated into useful products. We are excited to help catalyze these collaborations here at the Wyss Institute, and to see the breakthrough advances that emerge,” said Wyss Founding Director Donald Ingber, M.D., Ph.D., who is also the Judah Folkman Professor of Vascular Biology at Harvard Medical School and the Vascular Biology Program at Boston Children’s Hospital, and Professor of Bioengineering at SEAS.
This study is co-authored by Benjamin Goldberg, Ph.D., Neel Doshi, Kaushik Jayaram, Ph.D., and Jack Zhou from the Wyss Institute and Harvard SEAS.
Support for this research was contributed by the Wyss Institute for Biologically Inspired Engineering at Harvard University, Rolls-Royce, and the US Army Research Office.
NVIDIA Jetson AGX Xavier Module for Next-Gen Autonomous Machines
The Growth of Non-Industrial Robotics Is Driving a Diversification of New Robotics Applications, According to Tractica
Why AI robot toys could be good for kids
Growing bio-inspired shapes with a 300-robot swarm
Work by I. Slavkov, D. Carrillo-Zapata, N. Carranza, X. Diego, F. Jansson, J. Kaandorp, S. Hauert, J. Sharpe
Our work published today in Science Robotics describes how we grow fully self-organised shapes using a swarm of 300 coin-sized robots. The work was led by James Sharpe at EMBL and the Centre for Genomic Regulation (CRG) in Barcelona – together with my team at the Bristol Robotics Laboratory and University of Bristol.
Here’s a video summarising the results, or you can read the paper here:
Self-organised shapes
Nature is capable of producing impressive functional shapes throughout embryonic development. Broadly, there are two ways to form these shapes.
1) Top-down control. Cells have access to information about their position through some coordinate system, for example generated through their molecular gradients. Cells use this information to decide their fate, which ultimately creates the shapes. There are beautiful examples of this strategy being used for robot swarms, check here for work by Rubenstein et al. (video).
2) Local self-organisation. Cells generate reaction-diffusion systems, such as those described by Alan Turing, resulting in simple periodic patterns. Cells can use these patterns to decide their fate and the resulting shape.
We use the second strategy, here’s how it works.
Patterning
We start from a swarm of 300 closely packed robots in a disc – each running the same code. Each robot stores two morphogens u and v, which you can think of as virtual chemical signals. Morphogen u activates itself and the other morphogen v, whereas v inhibits itself and the other morphogen u – this is a ‘reaction’ network. ‘Diffusion’ of u and v happens through communication from robot to robot. Symmetry breaking caused by the ‘reaction-diffusion’ system results in spots emerging on the swarm (or stripes if we change the parameters!). Areas with high-levels of morphogens are shown in green – that’s what we call a “Turing spot”.
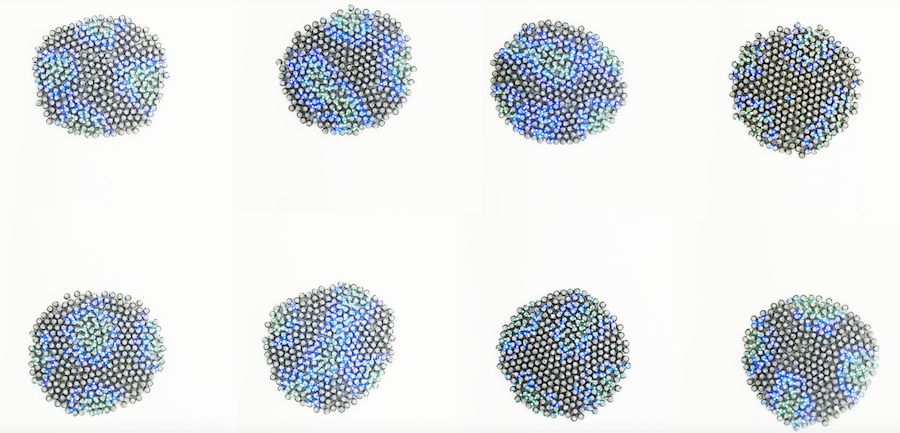
Tissue movement
In biology, cells may die or multiply depending on their patterning. As we can’t do either of those things with robots, we simply move robots from areas where they are no longer needed to areas of growth. The general idea is that robots that are on the edge of the swarm, and are not in a Turing spot, move along the edge of the swarm until they are near the spot. This causes protrusions to grow at the location of the Turing spots.

Following these simple rules, we are able to grow shapes in a repeatable manner, although all the shapes are slightly different. If you watch the video, you’ll see that these shapes look quite organic. We did over 20 experiments with large robot swarms, each one taking about 3 hours.
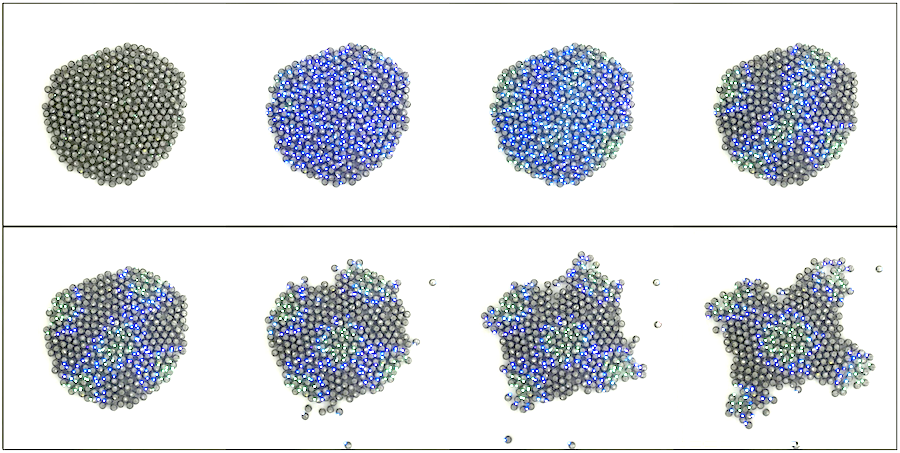
Because the rules are so simple, and only rely on local information, we get adaptability and robustness for free.
Adaptability
First, as the shape grows, the Turing spots move, showing that the patterning adapts to the shape of the swarm, and that the shape further adapts to the patterning. Second, we can easily change the starting configuration of the swarm (smaller number of robots, or a ‘rectangular’ starting conditions) and the shape still forms.
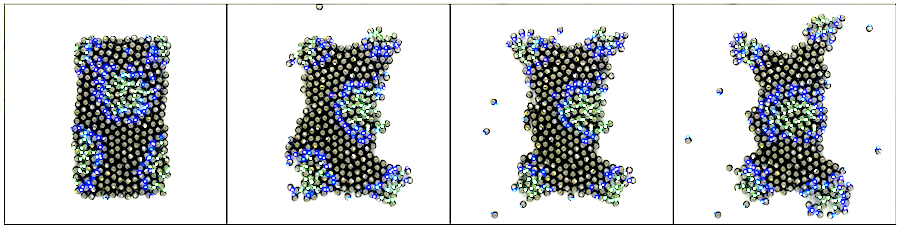
Robustness
Chopping off a protrusion, causes the robots to regrow it, or to reallocate robots to other protrusions in the swarm. Splitting the swarm causes it to self-heal.
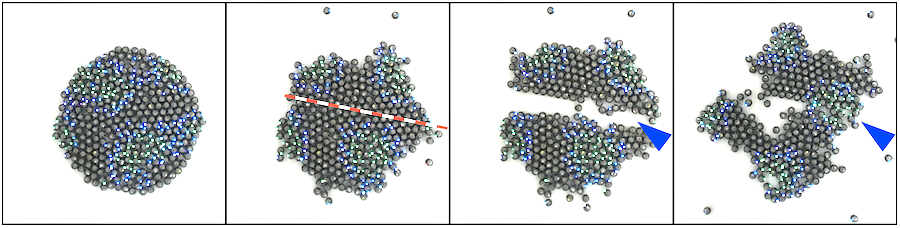
Potential for real world applications
While inspiration was taken from nature to grow the swarm shapes, the goal is ultimately to make large robot swarms for real-world applications. Imagine hundreds or thousands of tiny biodegradable robots growing shapes to explore a disaster environment after an earthquake or fire, or sculpting themselves into a dynamic 3D structure such as a temporary bridge that could automatically adjust its size and shape to fit any building or terrain. There is still a long way to go however, before we see such swarms outside the laboratory.
Team
James Sharpe (EMBL Barcelona) led the Swarm-Organ project, which was initiated at the Centre for Genomic Regulation (CRG) when Sharpe was a group leader there. Sabine Hauert (Bristol Robotics Laboratory and University of Bristol) was the key senior collaborator. Other collaborators were Fredrik Jansson (currently employed at Centrum Wiskunde & Informatica – CWI) and Jaap Kaandorp (University of Amsterdam – UvA).
Paper
You can read more in the paper Slavkov, I., Zapata D. C. et al., Science Robotics (2018).
Funding
The research leading to these results has received funding from the European Union Seventh Framework Programme (FP7) under grant agreement n° 601062, and the EPSRC Centre for Doctoral Training in Future Autonomous and Robotic Systems (FARSCOPE) at the Bristol Robotics Laboratory.