Autonomous robotic rover helps scientists with long-term monitoring of deep-sea carbon cycle and climate change
A model that translates everyday human activities into skills for an embodied artificial agent
Automated Loading and Unloading of CNC Machines
ReSkin could help researchers discover a sense of touch
Tobias Holmes: Agriculture Robots, Herbicide Resistance, and Education | Sense Think Act Podcast #6
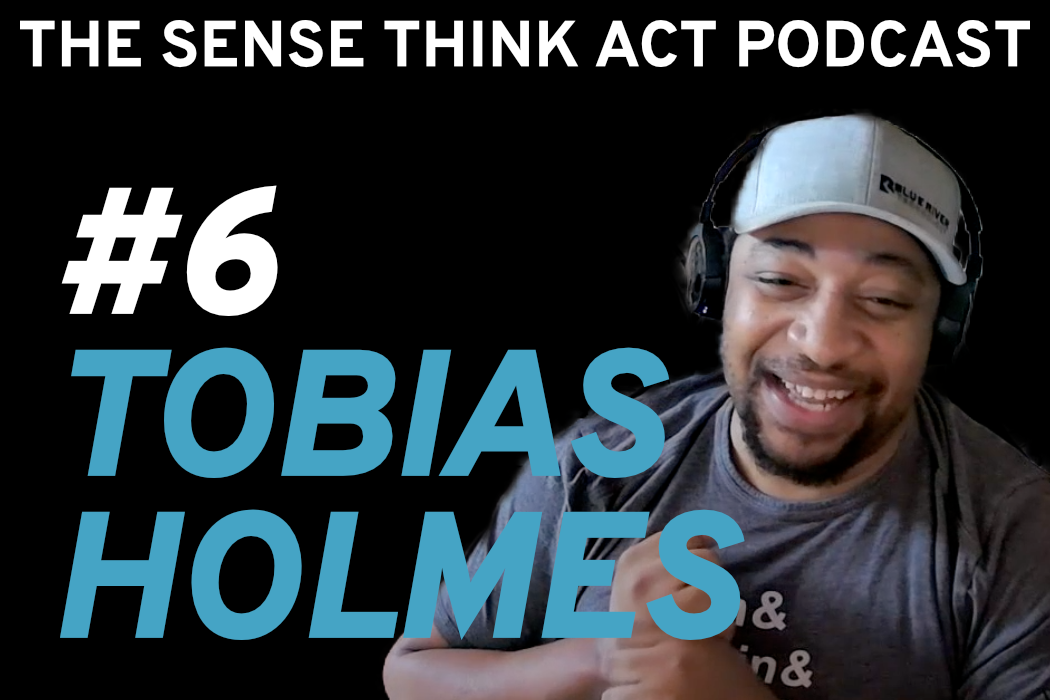
In this episode, Audrow Nash speaks to Tobias Holmes, Quality Assurance Manager at Blue River Technologies. Blue River uses computer vision and robotics in agriculture and was acquired by John Deere in 2017. Tobias speaks about herbicide resistance, spraying weeds, quality assurance and testing on hardware, and on encouraging kids to learn robotics.
Episode Links
- Download the episode
- Tobias’ LinkedIn
- Blue River Technology
- FIRST Robotics
- Crystal Ray High School (East Bay)
Podcast info
A new algorithm to help robots escape dead ends.
Investigating how robot systems can function better in dynamic environments
Evolution in the Press Shop – Intelligent, Camera-based Tool Protection in Stamping and Forming Technology
We are delighted to announce the launch of Scicomm – a joint science communication project from Robohub and AIhub
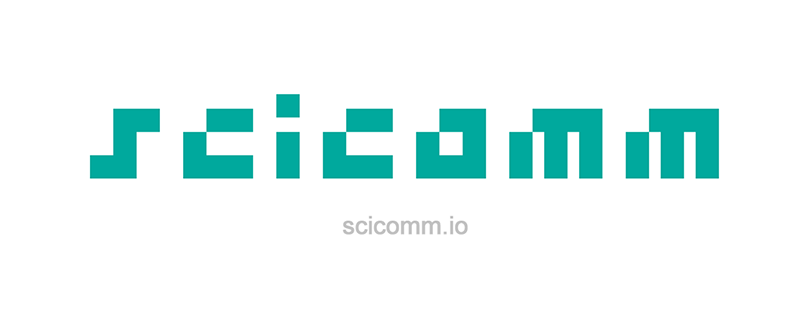
Scicomm.io is a science communication project which aims to empower people to share stories about their robotics and AI work. The project is a joint effort from Robohub and AIhub, both of which are educational platforms dedicated to connecting the robotics and AI communities to the rest of the world.
This project focuses on training the next generation of communicators in robotics and AI to build a strong connection with the outside world, by providing effective communication tools.
People working in the field are developing an enormous array of systems and technologies. However, due to a relative lack of high quality, impartial information in the mainstream media, the general public receive a lot hyped news which ends up causing fear and / or unrealistic expectations surrounding these technologies.
Scicomm.io has been created to facilitate the connection between the robotics and AI world and the rest of the world through teaching how to establish truthful, honest and hype-free communication. One that brings benefit to both sides.
Scicommm bytes
With our series of bite-sized videos you can quickly learn about science communication for robotics and AI. Find out why science communication is important, how to talk to the media, and about some of the different ways in which you can communicate your work. We have also produced guides with tips for turning your research into blog post and for avoiding hype when promoting your research.
Training
Training the next generation of science communicators is an important mission for scicomm.io (and indeed Robohub and AIhub). As part of scicomm.io, we run training courses to empower researchers to communicate about their work. When done well, stories about AI and robotics can help increase the visibility and impact of the work, lead to new connections, and even raise funds. However, most researchers don’t engage in science communication, due to a lack of skills, time, and reach that makes the effort worthwhile.
With our workshops we aim to overcome these barriers and make communicating robotics and AI ‘easy’. This is done through short training sessions with experts, and hands-on practical exercises to help students begin their science communication journey with confidence.
A virtual scicomm workshop in action.
During the workshops, participants will hear why science communication matters, learn the basic techniques of science communication, build a story around their own research, and find out how to connect with journalists and other communicators. We’ll also discuss different science communication media, how to use social media, how to prepare blog posts, videos and press releases, how to avoid hype, and how to communicate work to a general audience.
For more information about our workshops, contact the team by email.
Find out more about the scicomm.io project here.
Robots hit the streets as demand for food delivery grows
From a garage to Swiss lakes and rivers: the story of Proteus, an underwater robot
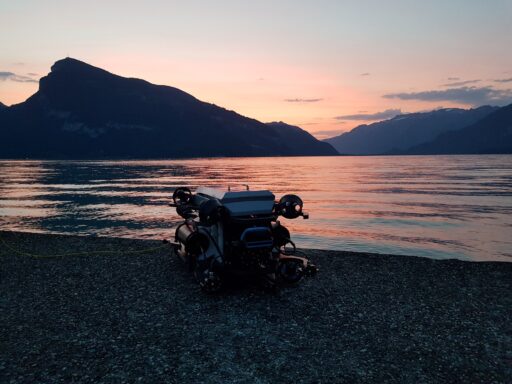
Proteus and sunset with the Swiss mountains in the background at Lake Thun (photo credit: Gallus Kaufmann)
In 2018, Christian Engler felt he’d studied enough theory at the ETH Zurich and longed to put it all into practice. It was evident to Christian that the best way to get hands-on experience was to start something himself. Others were not so sure. Especially when they heard about his ambition to revive a project from high school.
The project involved underwater robots, also known as Remotely Operated Vehicles (ROVs). But now Christian wanted to step it up a gear. He not only wanted to build an ROV, but he also wanted to take part at the international MATE ROV Competition 2019 – the biggest ROV competition in the world. His passion motivated a further seven students and Tethys Robotics was born.
Start of the journey
To be able to compete at a high level, Tethys Robotics needed support. The main supporter was and still is Professor Siegwart and his Autonomous Systems Lab (ASL). Due to a previous project, SCUBO, the team had the chance to benefit from their experience and were able to use their carbon fibre shell to build their version of the underwater robot, the SCUBO 2.0.
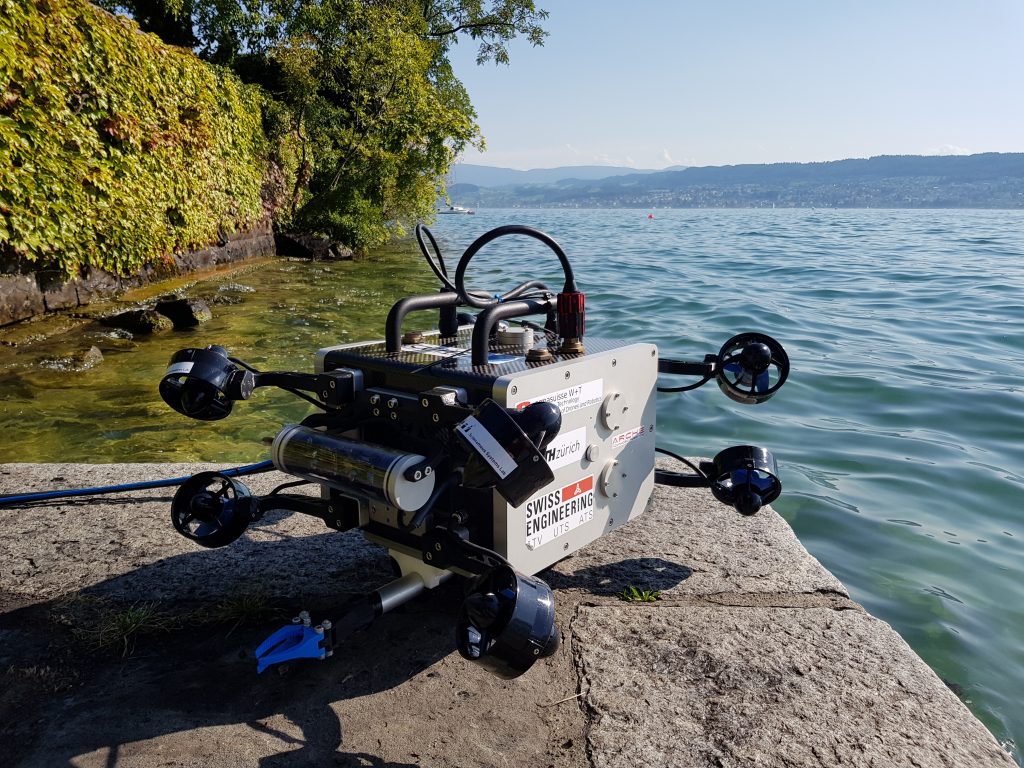
SCUBO taking a sunbath at Lake Zurich (photo credit: Gallus Kaufmann)
While the original SCUBO was developed to film coral reefs, the new version of SCUBO had to be adapted to fulfil the tasks at the MATE ROV Competition. To prevent damaging the coral reefs, the original SCUBO had a different position and orientation of the eight actuators (also known as thrusters) at the cost of stability and control. Furthermore, no batteries were allowed at the competition inside of the robot. For that reason, the entire electronics, software interface and controlling had to be redesigned to be able to take part at the competition.
Essentially, the sensors of both SCUBO versions are the same consisting of Attitude and Heading Reference System (AHRS), pressure sensor, stereo camera and temperature sensor.
The only downside was that the ASL did not have enough space to accommodate us. Therefore, we ended up working in the lab’s basement. But this did not affect our motivation – now complete with ‘garage start-up’ vibe – or the successful outcome. Tethys Robotics was the first Swiss team ever to compete. Out of 75 teams, Tethys came in at 9th place.
Real world applications
After the competition, SCUBO 2.0 was showcased at various exhibitions. This is how we came across the divers from the Swiss Explosive Ordnance Disposal (EOD), whose mission is to retrieve lost ammunition from Swiss lakes. Since this is a dangerous and very challenging task for divers, Tethys started collaborating on an underwater robot up to the task. The robot had to be modular, lightweight, and easily deployable. With the support of the ASL, the algorithms developed for drones have been implemented to the underwater drones of Tethys Robotics. And by having multiple tests at the operation site with the EOD divers and blank ammunition, the new underwater robot Proteus was developed with a real world application in mind. With their help, Proteus has been developed to be modular and more focused to be used as a diver buddy instead of working individually. In particular, the underwater drone can be used as a lift for material and as a communication device to the top side.
Challenges and future of Proteus
There have been many changes to the design and the application field between the competition robot and the new Proteus. Proteus is able to be deployed in every Swiss lake (+300 m depth rating) and is powered again, as the original SCUBO, by batteries. The communication and camera streams are transmitted via a fiber optics cable to a control station on the shore. Moreover, in addition to the sensors used in SCUBO, Proteus has been upgraded with sensors mainly used for localization and orientation underwater which consist of a sonar, Doppler Velocity Logger (DVL), acoustic Short Baseline system (SBL) and event cameras.
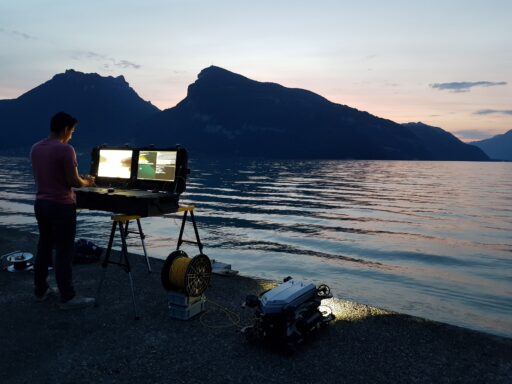
Proteus mission setup (photo credit: Gallus Kaufmann)
The current research focuses on the improvement of the underwater localization. The different sensors are not accurate, fast or robust enough to be used in Swiss lakes and in particular rivers. Therefore, a sensor fusion algorithm is being implemented to combine the advantages of the different sensors. Furthermore, Tethys Robotics is trying to find further applications and an appropriate market segment to position the developed underwater drones. By finding further partners and interest, the project could make the transition to a company and develop the prototypes to final products.