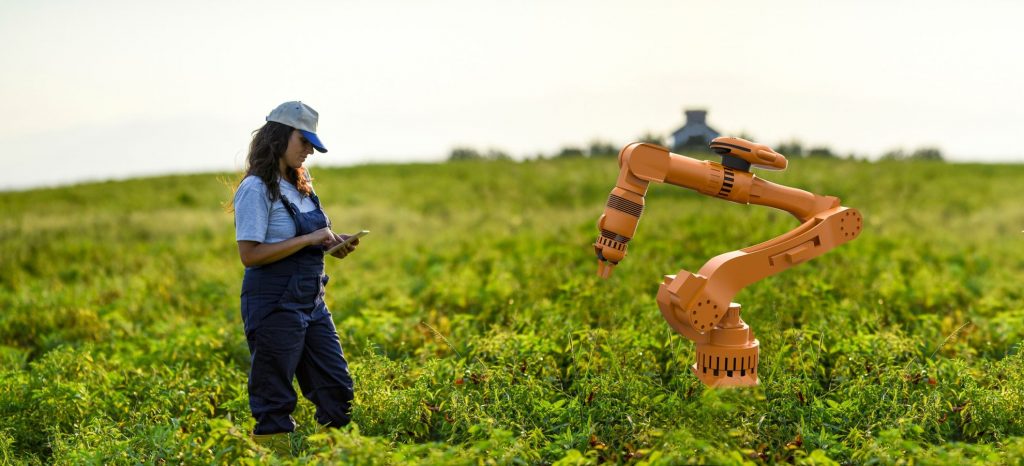
Artificial intelligence is set to revolutionise agriculture by helping farmers meet field-hand needs and identify diseased plants. © baranozdemir, iStock
In the Dutch province of Zeeland, a robot moves swiftly through a field of crops including sunflowers, shallots and onions. The machine weeds autonomously – and tirelessly – day in, day out.
“Farmdroid” has made life a lot easier for Mark Buijze, who runs a biological farm with 50 cows and 15 hectares of land. Buijze is one of the very few owners of robots in European agriculture.
Robots to the rescue
His electronic field worker uses GPS and is multifunctional, switching between weeding and seeding. With the push of a button, all Buijze has to do is enter coordinates and Farmdroid takes it from there.
‘With the robot, the weeding can be finished within one to two days – a task that would normally take weeks and roughly four to five workers if done by hand,’ he said. ‘By using GPS, the machine can identify the exact location of where it has to go in the field.’
About 12 000 years ago, the end of foraging and start of agriculture heralded big improvements in people’s quality of life. Few sectors have a history as rich as that of farming, which has evolved over the centuries in step with technological advancements.
In the current era, however, agriculture has been slower than other industries to follow one tech trend: artificial intelligence (AI). While already commonly used in forms ranging from automated chatbots and face recognition to car braking and warehouse controls, AI for agriculture is still in the early stages of development.
Now, advances in research are spurring farmers to embrace robots by showing how they can do everything from meeting field-hand needs to detecting crop diseases early.
Lean and green
For French agronomist Bertrand Pinel, farming in Europe will require far greater use of robots to be productive, competitive and green – three top EU goals for a sector whose output is worth around €190 billion a year.
“Labour is one of the biggest obstacles in agriculture.”
– Fritz van Evert, ROBS4CROPS
One reason for using robots is the need to forgo the use of herbicides by eliminating weeds the old-fashioned way: mechanical weeding, a task that is not just mundane but also arduous and time consuming. Another is the frequent shortage of workers to prune grapevines.
‘In both cases, robots would help,’ said Pinel, who is research and development project manager at France-based Terrena Innovation. ‘That is our idea of the future for European agriculture.’
Pinel is part of the EU-funded ROBS4CROPS project. With some 50 experts and 16 institutional partners involved, it is pioneering a robot technology on participating farms in the Netherlands, Greece, Spain and France.
‘This initiative is quite innovative,’ said Frits van Evert, coordinator of the project. ‘It has not been done before.’
In the weeds
AI in agriculture looks promising for tasks that need to be repeated throughout the year such as weeding, according to van Evert, a senior researcher in precision agriculture at Wageningen University in the Netherlands.
‘If you grow a crop like potatoes, typically you plant the crop once per year in the spring and you harvest in the fall, but the weeding has to be done somewhere between six and 10 times per year,’ he said.
Plus, there is the question of speed. Often machines work faster than any human being can.
“With this robot everything is done in the field.”
– Francisco Javier Nieto De Santos, FLEXIGROBOTS
Francisco Javier Nieto De Santos, coordinator of the EU-funded FLEXIGROBOTS project, is particularly impressed by a model robot that takes soil samples. When done by hand, this practice requires special care to avoid contamination, delivery to a laboratory and days of analysis.
‘With this robot everything is done in the field,’ De Santos said. ‘It can take several samples per hour, providing results within a matter of minutes.’
Eventually, he said, the benefits of such technologies will extend beyond the farm industry to reach the general public by increasing the overall supply of food.
Unloved labour
Meanwhile, agricultural robots may be in demand not because they can work faster than any person but simply because no people are available for the job.
Even before inflation rates and fertiliser prices began to surge in 2021 amid an energy squeeze made worse by Russia’s invasion of Ukraine this year, farmers across Europe were struggling on another front: finding enough field hands including seasonal workers.
‘Labour is one of the biggest obstacles in agriculture,’ said van Evert. ‘It’s costly and hard to get these days because fewer and fewer people are willing to work in agriculture. We think that robots, such as self-driving tractors, can take away this obstacle.’
The idea behind ROBS4CROPS is to create a robotic system where existing agricultural machinery is upgraded so it can work in tandem with farm robots.
For the system to work, raw data such as images or videos must first be labelled by researchers in ways than can later be read by the AI.
Driverless tractors
The system then uses these large amounts of information to make “smart” decisions as well as predictions – think about the autocorrect feature on laptop computers and mobile phones, for example.
A farming controller comparable to the “brain” of the whole operation decides what needs to happen next or how much work remains to be done and where – based on information from maps or instructions provided by the farmer.
The machinery – self-driving tractors and smart implements like weeders equipped with sensors and cameras – gathers and stores more information as it works, becoming “smarter”.
Crop protection
FLEXIGROBOTS, based in Spain, aims to help farmers use existing robots for multiple tasks including disease detection.
Take drones, for example. Because they can spot a diseased plant from the air, drones can help farmers detect sick crops early and prevent a wider infestation.
‘If you can’t detect diseases in an early stage, you may lose the produce of an entire field, the production of an entire year,’ said De Santos. ‘The only option is to remove the infected plant.’
For example, there is no treatment for the fungus known as mildew, so identifying and removing diseased plants early on is crucial.
Pooling information is key to making the whole system smarter, De Santos said. Sharing data gathered by drones with robots or feeding the information into models expands the “intelligence” of the machines.
Although agronomist Pinel doesn’t believe that agriculture will ever be solely reliant on robotics, he’s certain about their revolutionary impact.
‘In the future, we hope that the farmers can just put a couple of small robots in the field and let them work all day,’ he said.
Research in this article was funded by the EU. If you liked this article, please consider sharing it on social media.
Watch the video
This article was originally published in Horizon, the EU Research and Innovation magazine.