Commentary: War in Ukraine accelerates global drive toward killer robots
Stronger Outcomes for Automotive Component Machining with Enhanced Vision System
Understanding Vision Transformers (ViTs): Hidden properties, insights, and robustness of their representations
A robot that can help firefighters during indoor emergencies
RoboHouse Interview Trilogy, part II: Wendel Postma and Project MARCH
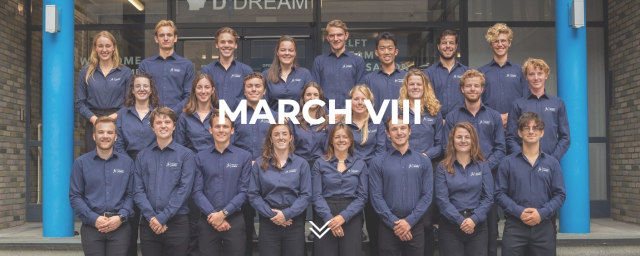
For the second part of our RoboHouse Interview Trilogy: The Working Life of the Robotics Engineer we speak with Wendel Postma, chief engineer at Project MARCH VIII. How does he resolve the conundrum of integration: getting a bunch of single-minded engineers to ultimately serve the needs of one single exoskeleton user? Rens van Poppel inquires.
Wendel oversees technical engineering quality, and shares responsible for on-time delivery within budget with the other project managers. He spends his days wandering around the Dream Hall on TU Delft Campus, encouraging his team to explore new avenues for developing the exoskeleton. What is possible within the time that we have? Can conflicting design solutions work together?
Bringing bad news is part of the chief engineer’s job.
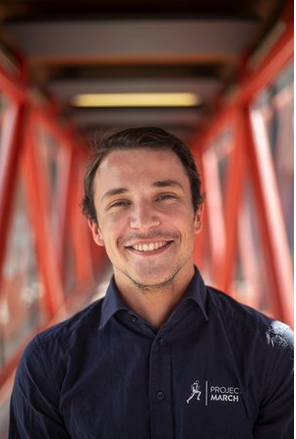
There is no shortage of hobbies and activities for Chief Engineer, Wendel. Sitting still is something he can’t do, which is why outside of Project MARCH, he is doing a lot of sports. This year, Wendel is making sure the team has 1 exoskeleton at the end of the year instead of many different parts. He also communicates well within the team so all the technological advances are understood and with a class of yoga so everyone can relax again. Wendel has many different goals. For example, he later wants to work in the health industry and complete an Ironman. Source: Project MARCH website.
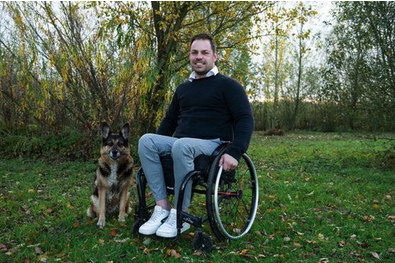
In daily life, Arnhem-based Project MARCH pilot Koen van Zeeland is an executive in laying fibreglass in the Utrecht area. He was diagnosed with a spinal cord injury in 2013. Koen is a hard worker and his phone is always ringing. Yet he likes to make time to have a drink with his friends in the pub. Besides the pub, you might also find him on the moors, where he likes to walk his dog Turbo. Koen is also super sporty. Besides working out three times a week, Koen is also an avid cyclist with the goal of cycling up the mountains in Austria on his handbike. Source: Project MARCH website.
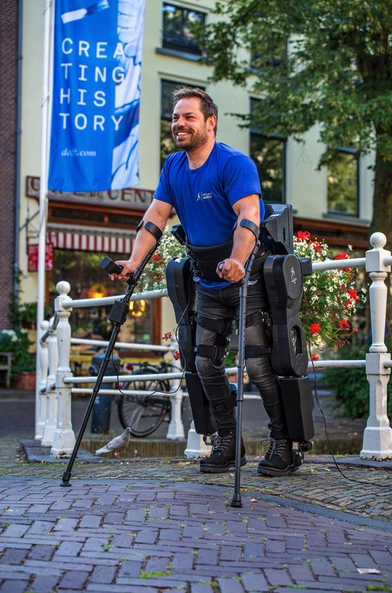
Koen van Zeeland is the primary test user of the exoskeleton and has control over the movements he makes. Project MARCH therefore calls him the ‘pilot’ of the exoskeleton. As the twenty-seventh and perhaps most important team member, Koen is valued highly within Project MARCH VIII. Source: Project MARCH website.
Project MARCH is iterative enterprise.
Most of its workplace drama comes from the urgency to deliver at least one significant improvement on the existing prototype. This year’s obsessions is weight; a lighter exoskeleton would require less power from both pilot and motors. Self-balancing would become easier to realise.
In order not to weaken the frame of the exoskeleton, there was a lot of enthusiasm to experiment with carbon fibre, which is both a light and strong material. Something, however, got in the way: the team struggled to find a pilot.
My job is making sure that in the end we don’t have 600 separate parts, but one exoskeleton.
“Having a test pilot is crucial if we are to reach our goals,” Wendel says. “Our current exoskeleton is built to fit the particular body shape of the person controlling it. The design is not yet adjustable to a different body shape. So it is crucial to get the pilot involved as quickly as possible.”
Not having a pilot was stressful for the entire team.
Their dream of creating a self-balancing exoskeleton was in danger. Wendel had to step up: “As chief engineer you have to make tough decisions. Carbon fibre is strong, but not flexible and difficult to machine. That is why we switched to aluminium, because it is easier to modify even after it is finished.”
“It was a huge disappointment,” Wendel says. “Some of us had already finished trainings for carbon manufacturing. Carbon parts were already ordered. The team felt let down. We had spent a so much time on something that was now impossible – because of the delays caused by having no pilot.”
“I learnt that bringing bad news is part of the chief engineer’s job. The next step is to look at how to convert the engineers’ enthusiasm for carbon fibre into new solutions and to redeploy their personal qualities.”
Wendel says the job also taught him to consider a hundred things at the same time. And to make sacrifices. Project MARCH involves long workdays and maybe not seeing your friends and roommates as much as you would like.
As a naturally curious person, Wendel found out that curiosity must be complemented by grit to make it in robotics. You often need to go deeper and study in more detail to make a good decision. “It is hard work. However, that is also what makes the job so much fun. You work in such a highly motivated team.”
That is also what makes the job so much fun.
The carbon story ended well, though.
When the team did found a pilot, hard-working Koen van Zeeland, the choice for aluminium as a base material paid off. Through a process of weight analysis, parts can now be optimised for an ever lighter exoskeleton.
The Project MARCH team continues to grow through setbacks and has doubled-down on their efforts to create the world’s first self-balancing exoskeleton. If they succeed, it will be a huge success for this unique way of running a business.
The post RoboHouse Interview Trilogy, Part II: Wendel Postma and Project MARCH appeared first on RoboHouse.
Third Wave Automation Announces Strategic Investment from Qualcomm Ventures and Zebra Technologies
ep.364: Shaking Up The Sheetmetal Industry, with Ed Mehr
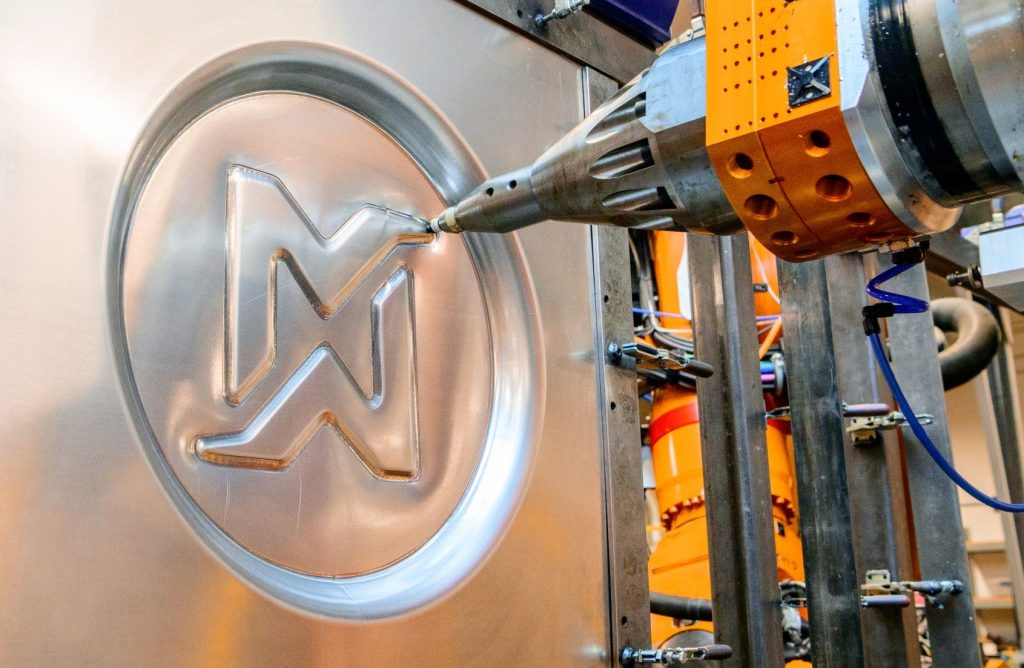
Conventional sheet metal manufacturing is highly inefficient for the low-volume production seen in the space industry. At Machina Labs, they developed a novel method of forming sheet metal using two robotic arms to bend the metal into different geometries. This method cuts down the time to produce large sheet metal parts from several months down to a few hours. Ed Mehr, Co-Founder and CEO of Machina Labs, explains this revolutionary manufacturing process.
Ed Mehr
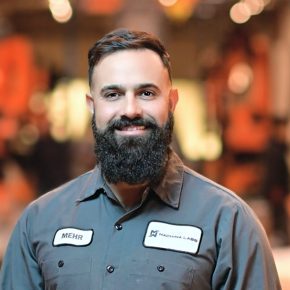
Ed Mehr is the co-founder and CEO of Machina Labs. He has an engineering background in smart manufacturing and artificial intelligence. In his previous position at Relativity Space, he led a team in charge of developing the world’s largest metal 3D printer. Relativity Space uses 3D printing to make rocket parts rapidly, and with the flexibility for multiple iterations. Ed previously was the CTO at Cloudwear (Now Averon), and has also worked at SpaceX, Google, and Microsoft.
Links
- Machina Labs
- Download mp3
- Subscribe to Robohub using iTunes, RSS, or Spotify
- Support us on Patreon
Robot Talk Episode 37 – Interview with Yang Gao
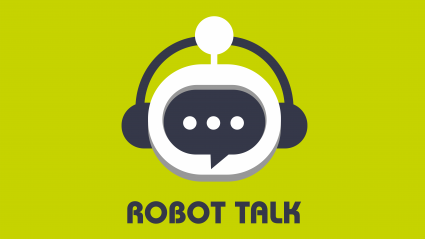
Claire chatted to Professor Yang Gao from the University of Surrey all about space robotics and planetary exploration.
Yang Gao is Professor of Space Autonomous Systems and Founding Head of the STAR LAB that specializes in robotic sensing, perception, visual guidance, navigation, and control (GNC) and biomimetic mechanisms for industrial applications in extreme environments. She brings over 20 years of research experience in developing robotics and autonomous systems, in which she has been the principal investigator of over 30 inter/nationally teamed projects and involved in real-world mission development.
Using the cuttlefish eye as a template for robot eyes that can see better in murky conditions
How a Government Drone Blacklist Could Impact Farms
How a Government Drone Blacklist Could Impact Farms
Top 5 robot trends 2023
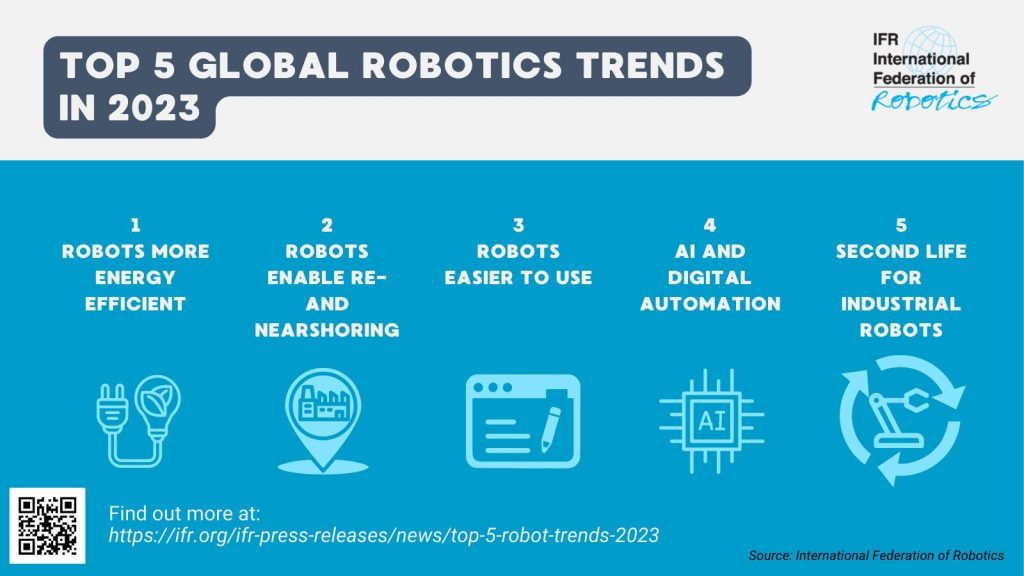
Top 5 Robot Trends 2023 © International Federation of Robotics
The stock of operational robots around the globe hit a new record of about 3.5 million units – the value of installations reached an estimated 15.7 billion USD. The International Federation of Robotics analyzes the top 5 trends shaping robotics and automation in 2023.
“Robots play a fundamental role in securing the changing demands of manufacturers around the world,” says Marina Bill, President of the International Federation of Robotics. “New trends in robotics attract users from small enterprise to global OEMs.”
1 – Energy Efficiency
Energy efficiency is key to improve companies’ competitiveness amid rising energy costs. The adoption of robotics helps in many ways to lower energy consumption in manufacturing. Compared to traditional assembly lines, considerable energy savings can be achieved through reduced heating. At the same time, robots work at high speed thus increasing production rates so that manufacturing becomes more time- and energy-efficient.
Today’s robots are designed to consume less energy, which leads to lower operating costs. To meet sustainability targets for their production, companies use industrial robots equipped with energy saving technology: robot controls are able to convert kinetic energy into electricity, for example, and feed it back into the power grid. This technology significantly reduces the energy required to run a robot. Another feature is the smart power saving mode that controls the robot´s energy supply on-demand throughout the workday. Since industrial facilities need to monitor their energy consumption even today, such connected power sensors are likely to become an industry standard for robotic solutions.
2 – Reshoring
Resilience has become an important driver for reshoring in various industries: Car manufacturers e.g. invest heavily in short supply lines to bring processes closer to their customers. These manufacturers use robot automation to manufacture powerful batteries cost-effectively and in large quantities to support their electric vehicle projects. These investments make the shipment of heavy batteries redundant. This is important as more and more logistics companies refuse to ship batteries for safety reasons.
Relocating microchip production back to the US and Europe is another reshoring trend. Since most industrial products nowadays require a semiconductor chip to function, their supply close to the customer is crucial. Robots play a vital role in chip manufacturing, as they live up to the extreme requirements of precision. Specifically designed robots automate the silicon wafer fabrication, take over cleaning and cleansing tasks or test integrated circuits. Recent examples of reshoring are Intel´s new chip factories in Ohio or the recently announced chip plant in the Saarland region of Germany run by chipmaker Wolfspeed and automotive supplier ZF.
3 – Robots easier to use
Robot programming has become easier and more accessible to non-experts. Providers of software-driven automation platforms support companies, letting users manage industrial robots with no prior programming experience. Original equipment manufacturers work hand-in-hand with low code or even no-code technology partners that allow users of all skill levels to program a robot.
The easy-to-use software paired with an intuitive user experience replaces extensive robotics programming and opens up new robotics automation opportunities: Software start-ups are entering this market with specialized solutions for the needs of small and medium-sized companies. For example: a traditional heavy-weight industrial robot can be equipped with sensors and a new software that allows collaborative setup operation. This makes it easy for workers to adjust heavy machinery to different tasks. Companies will thus get the best of both worlds: robust and precise industrial robot hardware and state-of-the-art cobot software.
Easy-to-use programming interfaces, that allow customers to set up the robots themselves, also drive the emerging new segment of low-cost robotics. Many new customers reacted to the pandemic in 2020 by trying out robotic solutions. Robot suppliers acknowledged this demand: Easy setup and installation, for instance, with pre-configured software to handle grippers, sensors or controllers support lower-cost robot deployment. Such robots are often sold through web shops and program routines for various applications are downloadable from an app store.
4 – Artificial Intelligence (AI) and digital automation
Propelled by advances in digital technologies, robot suppliers and system integrators offer new applications and improve existing ones regarding speed and quality. Connected robots are transforming manufacturing. Robots will increasingly operate as part of a connected digital ecosystem: Cloud Computing, Big Data Analytics or 5G mobile networks provide the technological base for optimized performance. The 5G standard will enable fully digitalized production, making cables on the shopfloor obsolete.
Artificial Intelligence (AI) holds great potential for robotics, enabling a range of benefits in manufacturing. The main aim of using AI in robotics is to better manage variability and unpredictability in the external environment, either in real-time, or off-line. This makes AI supporting machine learning play an increasing role in software offerings where running systems benefit, for example with optimized processes, predictive maintenance or vision-based gripping.
This technology helps manufacturers, logistics providers and retailers dealing with frequently changing products, orders and stock. The greater the variability and unpredictability of the environment, the more likely it is that AI algorithms will provide a cost-effective and fast solution – for example, for manufacturers or wholesalers dealing with millions of different products that change on a regular basis. AI is also useful in environments in which mobile robots need to distinguish between the objects or people they encounter and respond differently.
5 – Second life for industrial robots
Since an industrial robot has a service lifetime of up to thirty years, new tech equipment is a great opportunity to give old robots a “second life”. Industrial robot manufacturers like ABB, Fanuc, KUKA or Yaskawa run specialized repair centers close to their customers to refurbish or upgrade used units in a resource-efficient way. This prepare-to-repair strategy for robot manufacturers and their customers also saves costs and resources. To offer long-term repair to customers is an important contribution to the circular economy.
Top 5 robot trends 2023
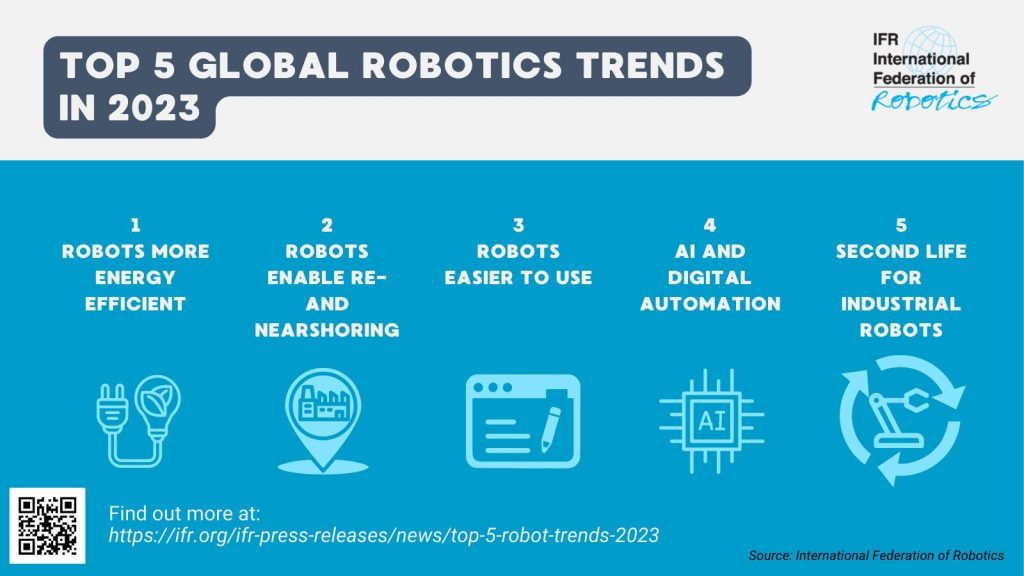
Top 5 Robot Trends 2023 © International Federation of Robotics
The stock of operational robots around the globe hit a new record of about 3.5 million units – the value of installations reached an estimated 15.7 billion USD. The International Federation of Robotics analyzes the top 5 trends shaping robotics and automation in 2023.
“Robots play a fundamental role in securing the changing demands of manufacturers around the world,” says Marina Bill, President of the International Federation of Robotics. “New trends in robotics attract users from small enterprise to global OEMs.”
1 – Energy Efficiency
Energy efficiency is key to improve companies’ competitiveness amid rising energy costs. The adoption of robotics helps in many ways to lower energy consumption in manufacturing. Compared to traditional assembly lines, considerable energy savings can be achieved through reduced heating. At the same time, robots work at high speed thus increasing production rates so that manufacturing becomes more time- and energy-efficient.
Today’s robots are designed to consume less energy, which leads to lower operating costs. To meet sustainability targets for their production, companies use industrial robots equipped with energy saving technology: robot controls are able to convert kinetic energy into electricity, for example, and feed it back into the power grid. This technology significantly reduces the energy required to run a robot. Another feature is the smart power saving mode that controls the robot´s energy supply on-demand throughout the workday. Since industrial facilities need to monitor their energy consumption even today, such connected power sensors are likely to become an industry standard for robotic solutions.
2 – Reshoring
Resilience has become an important driver for reshoring in various industries: Car manufacturers e.g. invest heavily in short supply lines to bring processes closer to their customers. These manufacturers use robot automation to manufacture powerful batteries cost-effectively and in large quantities to support their electric vehicle projects. These investments make the shipment of heavy batteries redundant. This is important as more and more logistics companies refuse to ship batteries for safety reasons.
Relocating microchip production back to the US and Europe is another reshoring trend. Since most industrial products nowadays require a semiconductor chip to function, their supply close to the customer is crucial. Robots play a vital role in chip manufacturing, as they live up to the extreme requirements of precision. Specifically designed robots automate the silicon wafer fabrication, take over cleaning and cleansing tasks or test integrated circuits. Recent examples of reshoring are Intel´s new chip factories in Ohio or the recently announced chip plant in the Saarland region of Germany run by chipmaker Wolfspeed and automotive supplier ZF.
3 – Robots easier to use
Robot programming has become easier and more accessible to non-experts. Providers of software-driven automation platforms support companies, letting users manage industrial robots with no prior programming experience. Original equipment manufacturers work hand-in-hand with low code or even no-code technology partners that allow users of all skill levels to program a robot.
The easy-to-use software paired with an intuitive user experience replaces extensive robotics programming and opens up new robotics automation opportunities: Software start-ups are entering this market with specialized solutions for the needs of small and medium-sized companies. For example: a traditional heavy-weight industrial robot can be equipped with sensors and a new software that allows collaborative setup operation. This makes it easy for workers to adjust heavy machinery to different tasks. Companies will thus get the best of both worlds: robust and precise industrial robot hardware and state-of-the-art cobot software.
Easy-to-use programming interfaces, that allow customers to set up the robots themselves, also drive the emerging new segment of low-cost robotics. Many new customers reacted to the pandemic in 2020 by trying out robotic solutions. Robot suppliers acknowledged this demand: Easy setup and installation, for instance, with pre-configured software to handle grippers, sensors or controllers support lower-cost robot deployment. Such robots are often sold through web shops and program routines for various applications are downloadable from an app store.
4 – Artificial Intelligence (AI) and digital automation
Propelled by advances in digital technologies, robot suppliers and system integrators offer new applications and improve existing ones regarding speed and quality. Connected robots are transforming manufacturing. Robots will increasingly operate as part of a connected digital ecosystem: Cloud Computing, Big Data Analytics or 5G mobile networks provide the technological base for optimized performance. The 5G standard will enable fully digitalized production, making cables on the shopfloor obsolete.
Artificial Intelligence (AI) holds great potential for robotics, enabling a range of benefits in manufacturing. The main aim of using AI in robotics is to better manage variability and unpredictability in the external environment, either in real-time, or off-line. This makes AI supporting machine learning play an increasing role in software offerings where running systems benefit, for example with optimized processes, predictive maintenance or vision-based gripping.
This technology helps manufacturers, logistics providers and retailers dealing with frequently changing products, orders and stock. The greater the variability and unpredictability of the environment, the more likely it is that AI algorithms will provide a cost-effective and fast solution – for example, for manufacturers or wholesalers dealing with millions of different products that change on a regular basis. AI is also useful in environments in which mobile robots need to distinguish between the objects or people they encounter and respond differently.
5 – Second life for industrial robots
Since an industrial robot has a service lifetime of up to thirty years, new tech equipment is a great opportunity to give old robots a “second life”. Industrial robot manufacturers like ABB, Fanuc, KUKA or Yaskawa run specialized repair centers close to their customers to refurbish or upgrade used units in a resource-efficient way. This prepare-to-repair strategy for robot manufacturers and their customers also saves costs and resources. To offer long-term repair to customers is an important contribution to the circular economy.