MiniMACS6 Stabilizes the Furuta Pendulum
Jellyfish-like robots could one day clean up the world’s oceans
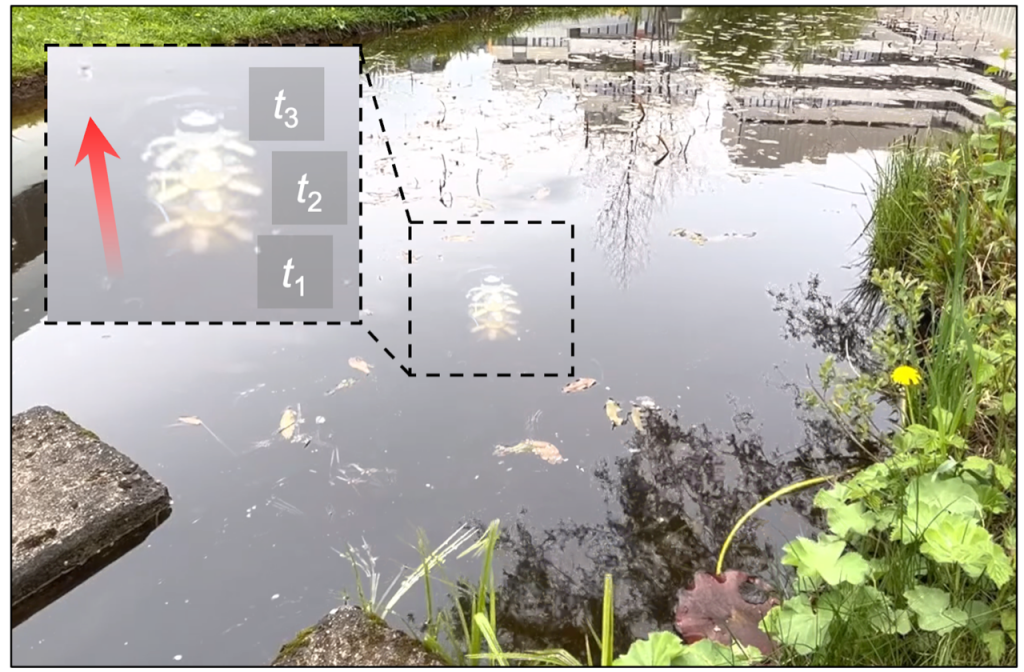
Most of the world is covered in oceans, which are unfortunately highly polluted. One of the strategies to combat the mounds of waste found in these very sensitive ecosystems – especially around coral reefs – is to employ robots to master the cleanup. However, existing underwater robots are mostly bulky with rigid bodies, unable to explore and sample in complex and unstructured environments, and are noisy due to electrical motors or hydraulic pumps. For a more suitable design, scientists at the Max Planck Institute for Intelligent Systems (MPI-IS) in Stuttgart looked to nature for inspiration. They configured a jellyfish-inspired, versatile, energy-efficient and nearly noise-free robot the size of a hand. Jellyfish-Bot is a collaboration between the Physical Intelligence and Robotic Materials departments at MPI-IS. “A Versatile Jellyfish-like Robotic Platform for Effective Underwater Propulsion and Manipulation” was published in Science Advances.
To build the robot, the team used electrohydraulic actuators through which electricity flows. The actuators serve as artificial muscles which power the robot. Surrounding these muscles are air cushions as well as soft and rigid components which stabilize the robot and make it waterproof. This way, the high voltage running through the actuators cannot contact the surrounding water. A power supply periodically provides electricity through thin wires, causing the muscles to contract and expand. This allows the robot to swim gracefully and to create swirls underneath its body.
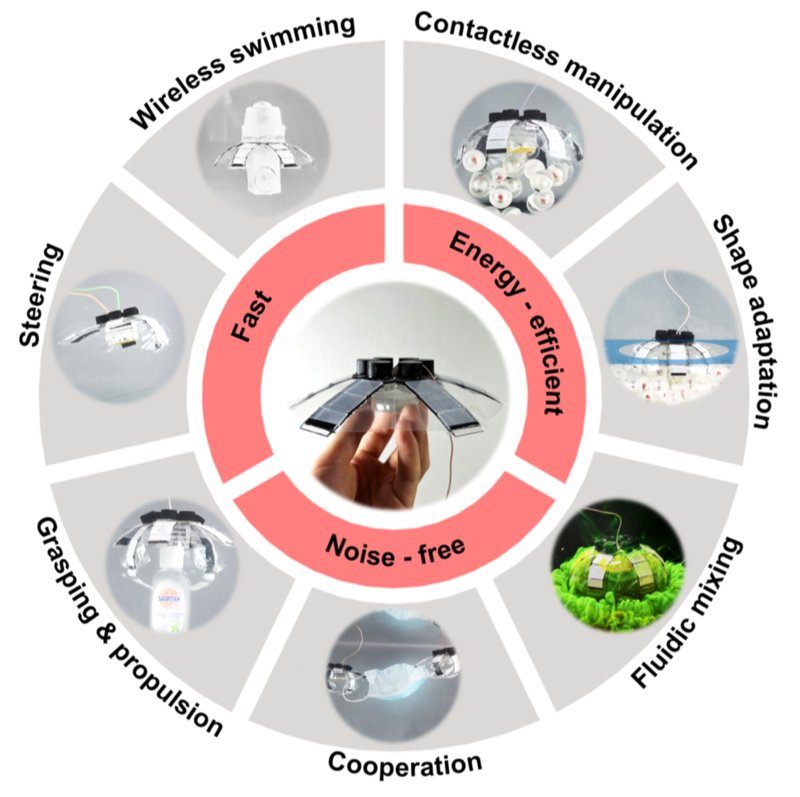
“When a jellyfish swims upwards, it can trap objects along its path as it creates currents around its body. In this way, it can also collect nutrients. Our robot, too, circulates the water around it. This function is useful in collecting objects such as waste particles. It can then transport the litter to the surface, where it can later be recycled. It is also able to collect fragile biological samples such as fish eggs. Meanwhile, there is no negative impact on the surrounding environment. The interaction with aquatic species is gentle and nearly noise-free”, Tianlu Wang explains. He is a postdoc in the Physical Intelligence Department at MPI-IS and first author of the publication.
His co-author Hyeong-Joon Joo from the Robotic Materials Department continues: “70% of marine litter is estimated to sink to the seabed. Plastics make up more than 60% of this litter, taking hundreds of years to degrade. Therefore, we saw an urgent need to develop a robot to manipulate objects such as litter and transport it upwards. We hope that underwater robots could one day assist in cleaning up our oceans.”
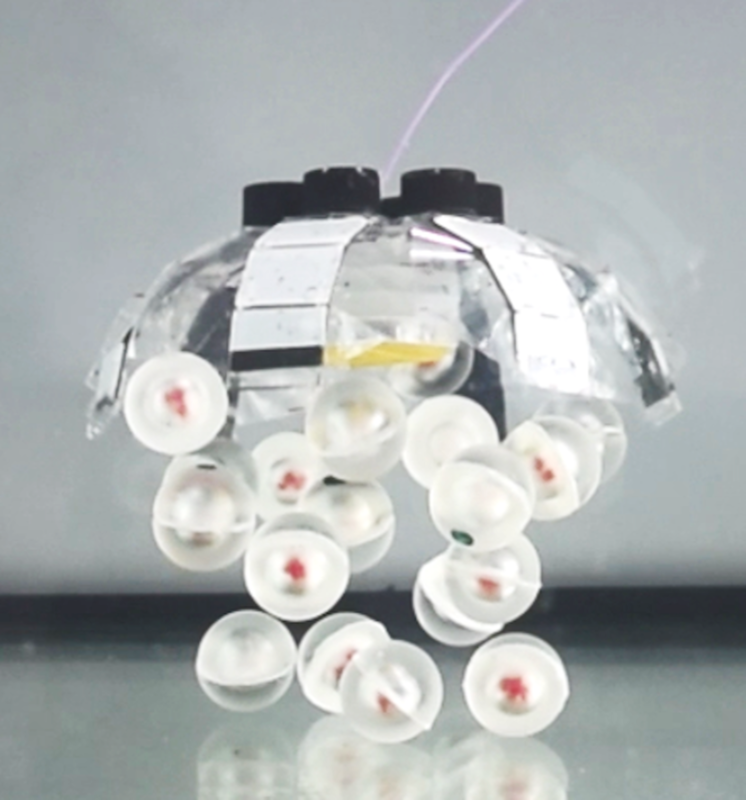
Jellyfish-Bots are capable of moving and trapping objects without physical contact, operating either alone or with several in combination. Each robot works faster than other comparable inventions, reaching a speed of up to 6.1 cm/s. Moreover, Jellyfish-Bot only requires a low input power of around 100 mW. And it is safe for humans and fish should the polymer material insulating the robot one day be torn apart. Meanwhile, the noise from the robot cannot be distinguished from background levels. In this way Jellyfish-Bot interacts gently with its environment without disturbing it – much like its natural counterpart.
The robot consists of several layers: some stiffen the robot, others serve to keep it afloat or insulate it. A further polymer layer functions as a floating skin. Electrically powered artificial muscles known as HASELs are embedded into the middle of the different layers. HASELs are liquid dielectric-filled plastic pouches that are partially covered by electrodes. Applying a high voltage across an electrode charges it positively, while surrounding water is charged negatively. This generates a force between positively-charged electrode and negatively-charged water that pushes the oil inside the pouches back and forth, causing the pouches to contract and relax – resembling a real muscle. HASELs can sustain the high electrical stresses generated by the charged electrodes and are protected against water by an insulating layer. This is important, as HASEL muscles were never before used to build an underwater robot.
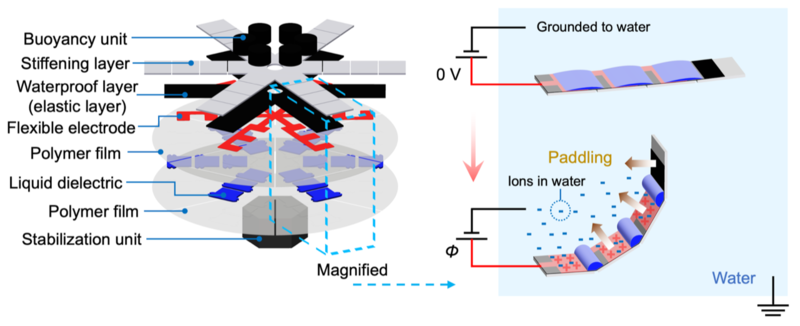
The first step was to develop Jellyfish-Bot with one electrode with six fingers or arms. In the second step, the team divided the single electrode into separated groups to independently actuate them.
“We achieved grasping objects by making four of the arms function as a propeller, and the other two as a gripper. Or we actuated only a subset of the arms, in order to steer the robot in different directions. We also looked into how we can operate a collective of several robots. For instance, we took two robots and let them pick up a mask, which is very difficult for a single robot alone. Two robots can also cooperate in carrying heavy loads. However, at this point, our Jellyfish-Bot needs a wire. This is a drawback if we really want to use it one day in the ocean”, Hyeong-Joon Joo says.
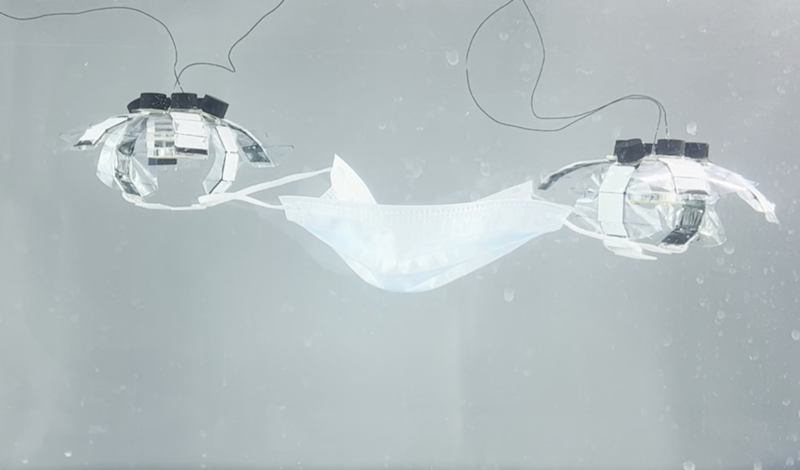
Perhaps wires powering robots will soon be a thing of the past. “We aim to develop wireless robots. Luckily, we have achieved the first step towards this goal. We have incorporated all the functional modules like the battery and wireless communication parts so as to enable future wireless manipulation”, Tianlu Wang continues. The team attached a buoyancy unit at the top of the robot and a battery and microcontroller to the bottom. They then took their invention for a swim in the pond of the Max Planck Stuttgart campus, and could successfully steer it along. So far, however, they could not direct the wireless robot to change course and swim the other way.
Knowing the team, it won’t take long to achieve this goal.
New model seeks to explain how humans interact socially with robots
New model seeks to explain how humans interact socially with robots
10 Key Questions to Evaluate AI-Powered Automation
Can’t find your phone? There’s a robot for that
Talking AUTOMATE 2023 with Stäubli
Adama Sesay on solving problems with sensors and microsystems
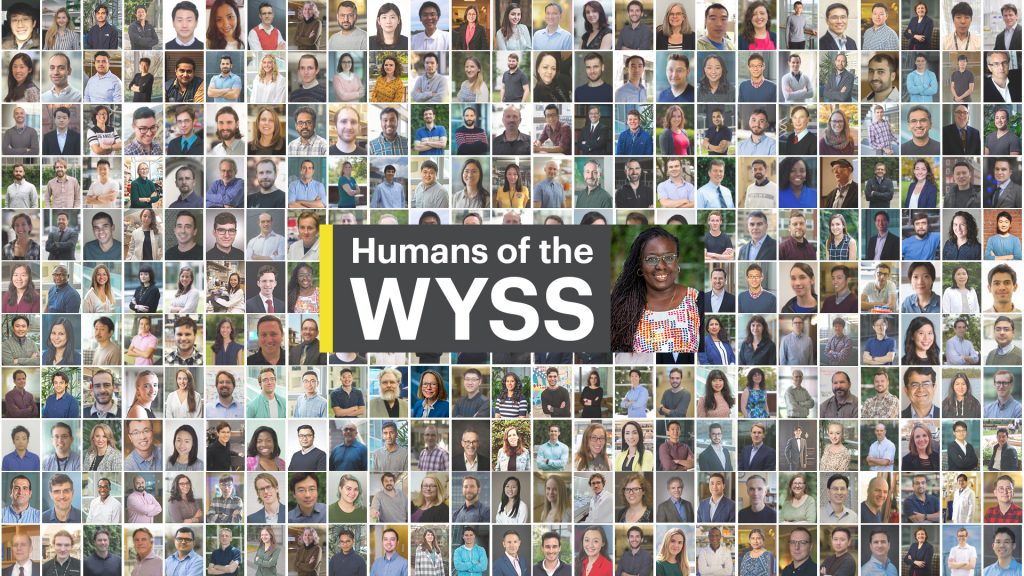
If you had asked Adama Sesay as a child what she wanted to be when she grew up, the answer would have been a doctor, an architect, and a firefighter. Now a Senior Engineer specializing in sensors and microsystems, you may think she’s gone in a completely different direction, but by following the passions that led her to those ideas – science, design, and saving lives – she’s found a career she loves. At the Wyss, Adama is a member of the Advanced Technology Team and works on a wide range of projects that span from sensor-integrated Organ Chips to make drugs safer to an enzyme that converts sugar to fiber to make food healthier, while simultaneously leading the Women’s Health Catalyst. Learn more about Adama and her work in this month’s Humans of the Wyss.
What projects are you involved with?
I specialize in biosensing, microfluidics, and microsystems, and my projects span over quite a diverse area. The first project I’ve been managing is a BARDA project, which is a federally funded project looking at integrating sensors to measure biomarkers like cytokines, from a lymph node tissue model, or a lymphoid follicle (LF) Chip. In this project, I’ve mostly concentrated on the instrumentation side, providing the actual hardware (which is a sort of sensor-integrated cartridge) and retrofitting it into a commercial Organ Chip system.
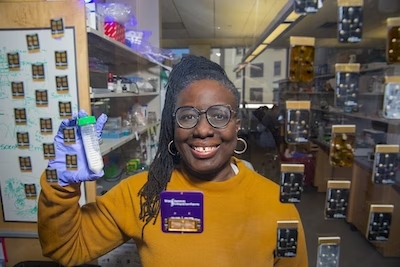
Adama Sesay, Senior Engineer II. Credit: Wyss Institute at Harvard University
Then I have another project where we’re developing an enzyme-encapsulated particle that reduces sugar in food once it’s consumed, converting it to dietary fiber. Basically, this would be a “smart food” ingredient, where the enzyme is only activated once you consume it. That way, the food tastes the same, but the actual amount of sugar your body metabolizes is lower.
I’m working on a third project where we are developing and microfabricating a microfluidic Blood Clotting Chip to study clotting time for patients that have mesothelioma, a cancer caused by exposure to asbestos. We’re collaborating with Massachusetts General Hospital and Boston Children’s Hospital.
What are biosensors, microfluidics, and microsystems?
A biosensor is a device that combines a biological component with a sensor transducer and can measure a biological or chemical reaction by producing signals to indicate the concentration of the analyte, or component of interest, in the monitored sample. Microfluidics refers to a system that has small channels that can move and deliver low volumes of fluid. The concept is that fabrication-wise, a microfluidic channel is anything that has dimensions in the micrometer range. The advantage of microfluidics is that you can deliver very low volumes to different areas and manipulate those flows a classic example is a an Organ Chip. A microsystem device in this context takes it a bit further and is the integration of sensors, microfluidics, and application. The three are a closely integrated package.
What real-world problems do these projects address?
With the BARDA project, we can use the LF Chips to monitor the immune system’s reaction to different types of drugs. We can use patient samples to get time resolved data about the inflammation response. In addition to helping screen drugs for safety, this could help us determine which therapies can be used on immuno-compromised patients or what a vaccine response will be in a certain population.
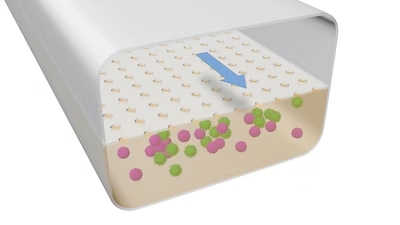
This illustration demonstrates the structure of the LF Chip that Adama is working on. Credit: Wyss Institute at Harvard University
The sugar fiber project will help address America’s ever-growing problems with obesity and diabetes. Despite these issues, there is a big food industry here that relies on refined sugars, especially high fructose corn syrup. In addition to those other issues, high fructose diets contribute to metabolic syndrome. Plus, the American diet is low in fiber. We started this project looking at how to make food more enjoyable while also being responsible. Our enzyme encapsulation will hopefully address diabetes and metabolic syndrome, while increasing fiber, which will make people’s gut microbiomes healthier.
We hope to use the Blood Clotting Chip to understand the clotting time and the thrombosis factors of mesothelioma. It can also be used as a diagnostic tool. Understanding a patient’s blood clotting factor is essential when they go into surgery, even beyond those suffering from this disease. This became even more apparent to me recently when my father needed to have emergency surgery, but they had to wait until he could be off blood thinners for a period of time. If we could use this as a diagnostic test, surgeons would know when a patient’s clotting factor was such that they were ready for surgery.
What is your specific role on the team?
I’m a Senior Engineer here and part of the Advanced Technology Team, I lead the biosensing, microfluidics, and microsystems effort at the Wyss. I am also responsible for the microfabrication room and efforts, and work closely with Pawan Jolly, who is the lead on sensors. That entails but is not limited to research project management, writing funding proposals, mentorship, and overseeing relationships with internal and external collaborator.
How are you helping to advance women’s health at the Wyss?
One of my biggest interests at the moment is to build up the Women’s Health Catalyst. In a place like the Wyss that’s looking at unmet needs, it’s natural that we have quite a lot of projects already in our pipeline dedicated to women’s health because therapeutics and diagnostics specifically aimed at women’s health issues are one of the biggest unmet clinical needs in the world. All this work is being done within our existing Focus Areas. Many of our researchers are incredibly dedicated to increasing our knowledge and finding real-world solutions.
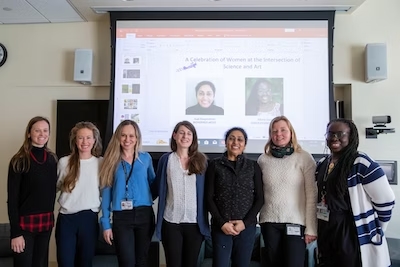
Adama and the other speakers at the Wyss’ event celebrating Women at the Intersection of Science and Art on International Women’s Day. Credit: Wyss Institute at Harvard University
So, right now we’re aiming to coalesce all these projects to bring together our brilliant scientists, clinicians, and technology teams to advance research and make drugs and devices to help people. We aim to be able to highlight these projects to attract external collaborators to work with our Wyss technology translation engine, and one day become a world-class beacon where people want to come and really make advances in women’s health.
How are you helping to bridge the gap between academia and industry at the Wyss?
I have a diverse group of researchers on my team including biologists, biotechnologists, biomedical engineers, and mechanical engineers who look at challenges very differently, while I look at the industrial need and see how we can translate the science into something to address the gaps. I think what it boils down to is facilitating the communication between scientists and engineers on the research side and translating that acquired knowledge into know-how, services, and products on the business and industrial sides.
“I think what it boils down to is facilitating the communication between scientists and engineers on the research side and translating that acquired knowledge into know-how, services, and products on the business and industrial sides.”
– Adama Sesay
For example, if I’m designing a diagnostic device, I will listen to the scientists about how the fundamental biology works in their system and use my experience in sensor development, microsystems, and developing point-of-care devices to speak to more practically minded engineers about how to build the device, finding a common language between the two. Then, we need to communicate why this device is useful to a business audience in order to successfully commercialize it.
What brought you to the Wyss?
I wanted to be in a place that was busy doing what I had been doing for a while in Europe, which is translational science. The first place on my wish list was the Wyss Institute. I loved the work going on here; the organs-on-chips and the translational nature of the place. It’s quite unique in its structure. So, I got in touch with people working here, especially in Donald Ingber’s lab, and I was lucky that there was a position open when I applied.
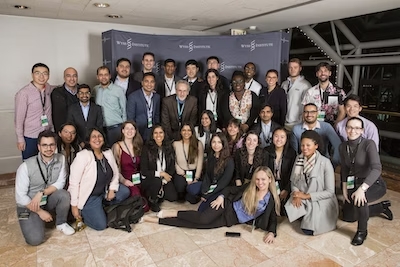
Members of Don Ingber’s lab, including Adama, at the Wyss Retreat in 2022. Credit: Wyss Institute at Harvard University
How has your previous work experience shaped your approach to your work today?
Starting with my master’s and Ph.D., much of my work has focused on technology transfer. It’s shaped my approach to work because it has taught me to talk to different people, bring various viewpoints and skills together, really listen to where the problems are, and find solutions. I think sometimes, especially earlier in your career, it’s easy to think that your idea is brilliant, but at the end of the day, it might be a great technology that’s hard to translate into a product. I’ve learned that you need to take your ego out of it, listen, and find the best way forward, even if it isn’t your way. Having a critical mass of new knowledge around you means you’ll always be at the forefront; you just have to be open to trying new things and making the sum of the parts better than the individual pieces.
What is your biggest piece of advice for an academic scientist looking to translate their technology?
“Maintain a level of curiosity and wonder. Be prepared to keep on improving and learning.”
– Adama Sesay
Maintain a level of curiosity and wonder. Be prepared to keep on improving and learning. Don’t be discouraged if you get knocked back, because even if your first approach doesn’t work, it’s because you go through that and you’re willing to get back up again that you will succeed.
What inspired you to get into this field?
If you had asked me what I wanted to be when I was a kid, I would always say a doctor, an architect, or a firefighter. A doctor because I really liked science and I didn’t know there was anything else out there other than that. My parents were in the medical field, so I thought that was it. An architect because I liked art, and I love buildings. I thought architecture was the practical way to apply that. I was unaware there was a profession called an engineer. And a firefighter because I enjoy being active and I thought they were so heroic. I just admired them.
I realized very quickly that none of those things were exactly for me, but I followed the passions that led me to those ideas – science, design, and saving lives – and by doing what I love I found my way to a career in translational research focused on sensors and microsystems. If you really enjoy what you do, it doesn’t feel like a job.
What continues to motivate you?
Making a difference and working with a great team in an amazing work environment. I think that knowing that the people I’m working alongside are truly having an impact, even if they’re not on my project directly, is very inspiring. It makes me feel that I’m a part of something that can cause positive change in my lifetime.
“I think that knowing that the people I’m working alongside are truly having an impact, even if they’re not on my project directly, is very inspiring. It makes me feel that I’m a part of something that can cause positive change in my lifetime.”
– Adama Sesay
When not at the Wyss, how do you like to spend your time?
I like roller skating. I started playing my clarinet again, which I used to do when I was a teenager, and that’s given me a lot of joy. I also like watching films. My favorite recent films have been Everything, Everywhere, All at Once and The Woman King. Everything, Everywhere, All at Once manages to be light while also touching some quite thought-provoking concepts. I love the types of films that you can spend time talking about. The Woman King, while it has faced some criticism for being inaccurate, opens a dialogue about African history on a world stage between individuals whom audiences in the west have never known or even wondered about it. Although some of these discussions might be uncomfortable, at least people are beginning to have them. Again, I like a film that starts a conversation.
What’s something unique about you that someone wouldn’t know from your resume?
My mother suffered from Alzheimer’s disease, and it finally took her this past Christmas. In her memory, my sister and I are working towards building a smart city in her village in Sierra Leone. To do this, we’re raising awareness and funding to build an agricultural school for women and empower them to harvest crops based on new technology that’s sustainable and appropriate for the land, given that it’s a wildlife sanctuary area, and create businesses from farming. Hopefully, by next year we can start working on the curriculum for the school. We’re putting a lot of work into this, but we think it’s a great way to honor our mother’s legacy and enable women to get out of poverty and become future entrepreneurs.
What does it feel like to be working towards translating cutting-edge technology that has the potential to have a real and significant impact on people’s lives and society?
It feels great to be part of such a dynamic environment. I think as an engineer and a technology transfer specialist, it’s the best of all worlds. I’m lucky enough to have worked at some exceptional institutes in some amazing countries, but the Wyss is quite special in that we have a critical mass of world-class, high-impact projects ripe for translation. I’m in my fifth year now and it’s been a great ride so far. I’m looking forward to what comes next.
Study observes the interactions between live fish and fish-like robots
How the Talent Shortage Is Helping and Hindering the Field of Robotics
Robot Talk Episode 48 – Georgia Chalvatzaki
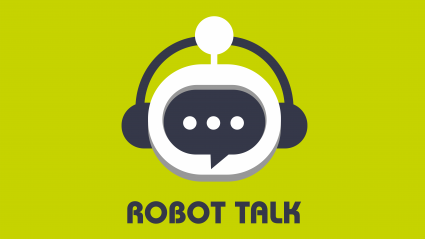
Claire chatted to Georgia Chalvatzaki from the Technical University of Darmstadt all about mobile assistive robots, learning, and planning.
Georgia Chalvatzaki is a Professor of Robot Perception and Learning at the Technical University of Darmstadt, Germany. Before that, she was an Assistant Professor and Independent Research Group Leader since March 2021, after getting the renowned Emmy Noether grant of the German Research Foundation. She completed her Ph.D. in 2019 at the Intelligent Robotics and Automation Lab at the National Technical University of Athens, Greece, with her thesis “Human-Centered Modeling for Assistive Robotics: Stochastic Estimation and Robot Learning in Decision-Making.”
Robotic proxy brings remote users to life in real time
Talking AUTOMATE 2023 with TM Robotics
The 5 Laws of Robotics
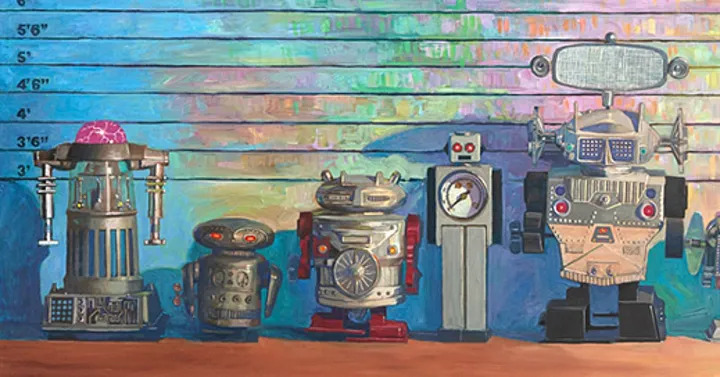
I have been studying the whole range of issues/opportunities in the commercial roll out of robotics for many years now, and I’ve spoken at a number of conferences about the best way for us to look at regulating robotics. In the process I’ve found that my guidelines most closely match the EPSRC Principles of Robotics, although I provide additional focus on potential solutions. And I’m calling it the 5 Laws of Robotics because it’s so hard to avoid Asimov’s Laws of Robotics in the public perception of what needs to be done.
The first most obvious point about these “5 Laws of Robotics” should be that I’m not suggesting actual laws, and neither actually was Asimov with his famous 3 Laws (technically 4 of them). Asimov proposed something that was hardwired or hardcoded into the existence of robots, and of course that didn’t work perfectly, which gave him the material for his books. Interestingly Asimov believed, as did many others at the time (symbolic AI anyone?) that it was going to be possible to define effective yet global behavioral rules for robots. Whereas, I don’t.
My 5 Laws of Robotics are:
- Robots should not kill.
- Robots should obey the law.
- Robots should be good products.
- Robots should be truthful.
- Robots should be identifiable.
What exactly does those laws mean?
Firstly, people should not legally able to weaponize robots, although there may be lawful exclusions for use by defense forces or first responders. Some people are completely opposed to Lethal Autonomous Weapon Systems (LAWS) in any form, whereas others draw the line at robot weapons being ultimately under human command, with accountability to law. Currently in California there is a proposed legislation to introduce fines for individuals building or modifying weaponized robots, drones or autonomous systems, with the exception of ‘lawful’ use.
Secondly, robots should be built so that they comply with existing laws, including privacy laws. This implies some form of accountability for companies on compliance in various jurisdictions, and while that is technically very complex, successful companies will be proactive because companies otherwise there will be a lot of court cases and insurance claims keeping lawyers happy but badly impacting the reputation of all robotics companies.
Thirdly, although we are continually developing and adapting standards as our technologies evolve, the core principle is that robots are products, designed to do tasks for people. As such, robots should be safe, reliable and do what they claim to do, in the manner that they claim to operate. Misrepresentation of the capabilities of any product is universally frowned upon.
Fourthly, and this is a fairly unique capability of robots, robots should not lie. Robots have the illusion of emotions and agency, and humans are very susceptible to being ‘digitally nudged’ or manipulated by artificial agents. Examples include robots or avatars claiming to be your friend, but could be as subtle as robots using a human voice just as if there was a real person listening and speaking. Or not explaining that a conversation that you’re having with a robot might have many listeners at other times and locations. Robots are potentially amazingly effective advertizing vehicles, in ways we are not yet expecting.
Finally, and this extends the principles of accountability, transparency and truthfulness, it should be possible to know who is the owner and/or operator of any robot that we interact with, even if we’re just sharing a sidewalk with them. Almost every other vehicle has to comply with some registration law or process, allowing ownership to be identified.
What can we do to act on these laws?
- Robot Registry (license plates, access to database of owners/operators)
- Algorithmic Transparency (via Model Cards and Testing Benchmarks)
- Independent Ethical Review Boards (as in biotech industry)
- Robot Ombudspeople (to liaise between the public, policy makers and the robotics industry)
- Rewarding Good Robots (design awards and case studies)
There are many organizations releasing guides, principles, and suggested laws. I’ve surveyed most of them and looked at the research. Most of them are just ethical hand wringing and accomplish nothing because they don’t factor in real world conditions around what the goals are, who would be responsible and how to make progress towards the goals. I wrote about this issue ahead of giving a talk at the ARM Developer Summit in 2020 (video included below).
Silicon Valley Robotics announced the first winners of our inaugural Robotics Industry Awards in 2020. The SVR Industry Awards consider the responsible design as well as technological innovation and commercial success. There are also some ethical checkmark or certification initiatives under preparation, but like the development of new standards, these can take a long time to do properly, whereas awards, endorsements and case studies can be available immediately to foster the discussion of what constitutes good robots, and, what are the social challenges that robotics needs to solve.
The Federal Trade Commission recently published “The Luring Test: AI and the engineering of consumer trust” describing the
For those not familiar with Isaac Asimov’s famous Three Laws of Robotics, they are:
First Law: A robot may not injure a human being, or, through inaction, allow a human being to come to harm.
Second Law: A robot must obey the orders given it by human beings except where such orders would conflict with the First Law.
Third Law: A robot must protect its own existence as long as such protection does not conflict with the First or Second Law.
Asimov later added a Fourth (called the Zeroth Law, as in 0, 1, 2, 3)
Zeroth Law: A robot may not harm humanity, or, by inaction, allow humanity to come to harm
Robin R. Murphy and David D. Woods have updated Asimov’s laws to be more similar to the laws I proposed above and provide a good analysis for what Asimov’s Laws meant and why they’ve changed them to deal with modern robotics. Beyond Asimov The Three Laws of Responsible Robotics (2009)
Some other selections from the hundreds of principles, guidelines and surveys of the ethical landscape that I recommend come from one of the original EPSRC authors, Joanna Bryson.
The Meaning of the EPSRC Principles of Robotics (2016)
And the 2016/2017 update from the original EPSRC team:
(2017) Principles of robotics: regulating robots in the real world, Connection Science, 29:2, 124-129, DOI: 10.1080/09540091.2016.1271400
Another survey worth reading is on the Stanford Plato site: https://plato.stanford.edu/entries/ethics-ai/