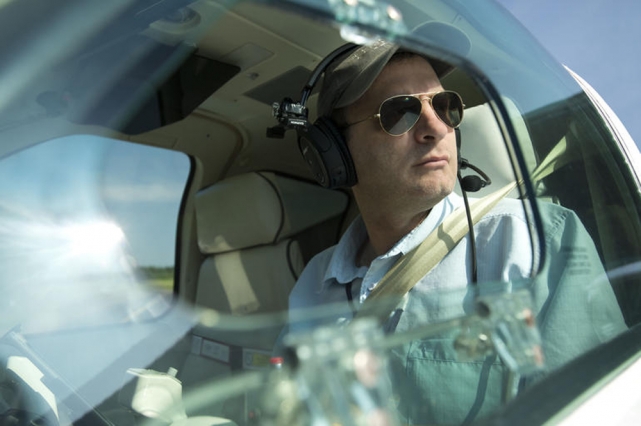
Science and technology are essential tools for innovation, and to reap their full potential, we also need to articulate and solve the many aspects of today’s global issues that are rooted in the political, cultural, and economic realities of the human world. With that mission in mind, MIT’s School of Humanities, Arts, and Social Sciences has launched The Human Factor — an ongoing series of stories and interviews that highlight research on the human dimensions of global challenges. Contributors to this series also share ideas for cultivating the multidisciplinary collaborations needed to solve the major civilizational issues of our time.
David Mindell, the Frances and David Dibner Professor of the History of Engineering and Manufacturing and Professor of Aeronautics and Astronautics at MIT, researches the intersections of human behavior, technological innovation, and automation. Mindell is the author of five acclaimed books, most recently “Our Robots, Ourselves: Robotics and the Myths of Autonomy” (Viking, 2015). He is also the co-founder of Humatics Corporation, which develops technologies for human-centered automation. SHASS Communications recently asked him to share his thoughts on the relationship of robotics to human activities, and the role of multidisciplinary research in solving complex global issues.
Q: A major theme in recent political discourse has been the perceived impact of robots and automation on the United States labor economy. In your research into the relationship between human activity and robotics, what insights have you gained that inform the future of human jobs, and the direction of technological innovation?
A: In looking at how people have designed, used, and adopted robotics in extreme environments like the deep ocean, aviation, or space, my most recent work shows how robotics and automation carry with them human assumptions about how work gets done, and how technology alters those assumptions. For example, the U.S. Air Force’s Predator drones were originally envisioned as fully autonomous — able to fly without any human assistance. In the end, these drones require hundreds of people to operate.
The new success of robots will depend on how well they situate into human environments. As in chess, the strongest players are often the combinations of human and machine. I increasingly see that the three critical elements are people, robots, and infrastructure — all interdependent.
Q: In your recent book “Our Robots, Ourselves,” you describe the success of a human-centered robotics, and explain why it is the more promising research direction — rather than research that aims for total robotic autonomy. How is your perspective being received by robotic engineers and other technologists, and do you see examples of research projects that are aiming at human-centered robotics?
A: One still hears researchers describe full autonom as the only way to go; often they overlook the multitude of human intentions built into even the most autonomous systems, and the infrastructure that surrounds them. My work describes situated autonomy, where autonomous systems can be highly functional within human environments such as factories or cities. Autonomy as a means of moving through physical environments has made enormous strides in the past ten years. As a means of moving through human environments, we are only just beginning. The new frontier is learning how to design the relationships between people, robots, and infrastructure. We need new sensors, new software, new ways of architecting systems.
Q: What can the study of the history of technology teach us about the future of robotics?
A: The history of technology does not predict the future, but it does offer rich examples of how people build and interact with technology, and how it evolves over time. Some problems just keep coming up over and over again, in new forms in each generation. When the historian notices such patterns, he can begin to ask: Is there some fundamental phenomenon here? If it is fundamental, how is it likely to appear in the next generation? Might the dynamics be altered in unexpected ways by human or technical innovations?
One such pattern is how autonomous systems have been rendered less autonomous when they make their way into real world human environments. Like the Predator drone, future military robots will likely be linked to human commanders and analysts in some ways as well. Rather than eliding those links, designing them to be as robust and effective as possible is a worthy focus for researchers’ attention.
Q: MIT President L. Rafael Reif has said that the solutions to today’s challenges depend on marrying advanced technical and scientific capabilities with a deep understanding of the world’s political, cultural, and economic realities. What barriers do you see to multidisciplinary, sociotechnical collaborations, and how can we overcome them?
A: I fear that as our technical education and research continues to excel, we are building human perspectives into technologies in ways not visible to our students. All data, for example, is socially inflected, and we are building systems that learn from those data and act in the world. As a colleague from Stanford recently observed, go to Google image search and type in “Grandma” and you’ll see the social bias that can leak into data sets — the top results all appear white and middle class.
Now think of those data sets as bases of decision making for vehicles like cars or trucks, and we become aware of the social and political dimensions that we need to build into systems to serve human needs. For example, should driverless cars adjust their expectations for pedestrian behavior according to the neighborhoods they’re in?
Meanwhile, too much of the humanities has developed islands of specialized discourse that is inaccessible to outsiders. I used to be more optimistic about multidisciplinary collaborations to address these problems. Departments and schools are great for organizing undergraduate majors and graduate education, but the old two-cultures divides remain deeply embedded in the daily practices of how we do our work. I’ve long believed MIT needs a new school to address these synthetic, far-reaching questions and train students to think in entirely new ways.
Interview prepared by MIT SHASS Communications
Editorial team: Emily Hiestand (series editor), Daniel Evans Pritchard