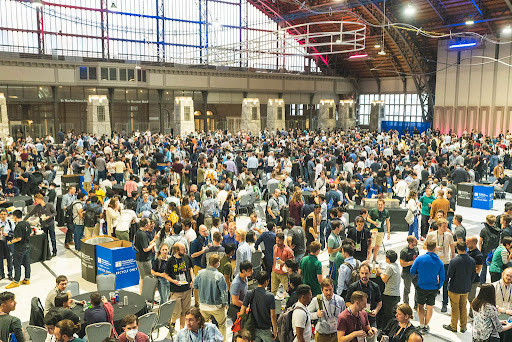
Welcome Reception. Credits: Wise Owl Multimedia
The 39th edition of the IEEE International Conference on Robotics and Automation (ICRA) took place at the Pennsylvania Convention Center in Philadelphia (USA) and online May 23-27. ICRA 2022 brought together the world’s top researchers and companies to share ideas and advances in the fields of robotics and automation.
Nearly 8,000 participants from academia and industry, including 4700 in person, from a total of 97 countries, joined the largest conference in robotics. Indeed, these figures reflect the evolution of the field in the last 34 years, with the last ICRA in Philadelphia (1988) only welcoming around 300 participants and a few exhibitors.
“We were thrilled to see the robotics community respond so positively to the first in-person ICRA conference since the pandemic started,” ICRA 2022 General Co-Chair George J. Pappas (University of Pennsylvania) commented. “In addition to breaking numerous records, such as in-person attendance and number of countries represented, there was an incredible amount of energy and interaction among attendees, exhibitors, competitors, and other aspects of the technical program. By all accounts, ICRA 2022 has been a major success.”
Not only did ICRA 2022 have an impact on the robotics community worldwide, but also locally in the city of Philadelphia and the state of Pennsylvania. As ICRA 2022 General Co-Chair Vijay Kumar (University of Pennsylvania) stated, “ICRA 2022 showcased Philadelphia area robotics research and development activities in academia and industry, and exposed high school and university students to exciting STEM opportunities and cutting edge research in robotics.”
The main topic of ICRA 2022 was ‘Future of Work’, with dedicated discussion sessions such as the Future of Work Forum, which featured panelists Jeff Burnstein (A3), Erik Brynjolfssonn (Stanford), Moshe Vardi (Rice University), Michael Lotito (Littler), Bernd Liepert (EuRobotics), Cecilia Laschi (NUS), and Ioana Marinescu (University of Pennsylvania). The main take-home message of the session, Chaired by Henrik Christensen (University of California, San Diego), was that employment and robot sales are correlated. “When companies hire people, they also invest in new technology. An important aspect is how we train the workforce, and how we re-train to continue to have access to a competitive workforce,” as Henrik Christensen summarized. “The panel agreed that there is a need for a comprehensive view of how we provide training, invest in technology, and provide appropriate policies to continue to grow the economy,” he finished. Another five Forum sessions were organized, covering the topics of Industry, US National Robotics Programs, Investor/Venture Capital, Start-ups, and Autonomous Driving.
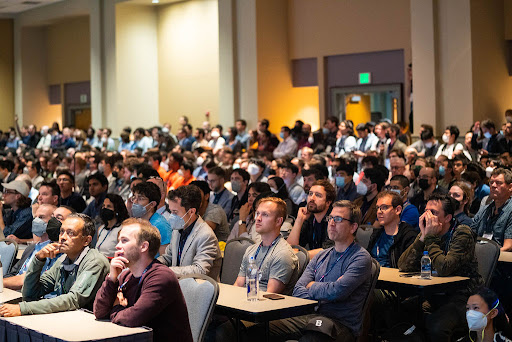
Participants in one of the sessions. Credits: Wise Owl Multimedia
Plenary and Keynote sessions were an important part of the conference, with 12 top researchers from the robotics community being invited to share their reflections on topics such as Robots, Ethics, and Society (Ayanna Howard, Ohio State University, USA); Human-Machine Partnerships and Work of the Future (Julie Shah, MIT, USA); or the Embodied Intelligence Aporia (Antonio Bicchi, University of Pisa, Italy), among others. Many research contributions were also presented during ICRA 2022 by the robotics community during the 1,500 Technical presentations and 56 Workshop & Tutorial sessions, especially by students, who represented 46% of all participants. A total of 13 Awards were given to researchers to honor their outstanding contributions in topics such as Computer Vision and Pattern Recognition, Robot Grasping, Collaborative Transportation, Legged & Aerial Robot Subterranean Exploration, Monocopters, Human-Robot Interaction for Surgery, Manipulation, Track-leg & Wheel-leg Ground Robotics, Biomimetic Tactile Sensors, Visual Odometry, and Trajectory Optimization.
Researchers and companies were able to show their robots in action in the 10 Competitions that were organized, including robots understanding where they are and moving or flying around obstacles, battling robots, robots setting dinner tables, and even examining the ethics of robots doing tasks for humans. A wide range of international teams competed in challenges like the ‘10th F1TENTH Grand Prix’ (winning place went to University of Pennsylvania students), where competitors had to build a 1:10 scaled autonomous race car, and write software for it to race head-to-head with the rest of the cars, minimizing lap time without crashing. Other competitions like the ‘FIRST LEGO League Challenge’ featured younger students, where local teams of 4th-8th graders had to design, build, and program a LEGO robot to complete autonomous missions. “Competitions provide an excellent way to validate research. Robotics research results often show great progress, but it is hard to compare different methods unless they are on the same playing field literally,” ICRA 2022 Chair of Competitions Mark Yim (University of Pennsylvania) stated. “There are also the outreach components. Competitions provide an exciting mechanism to show students and the general population what is involved in robotics,” Mark added.
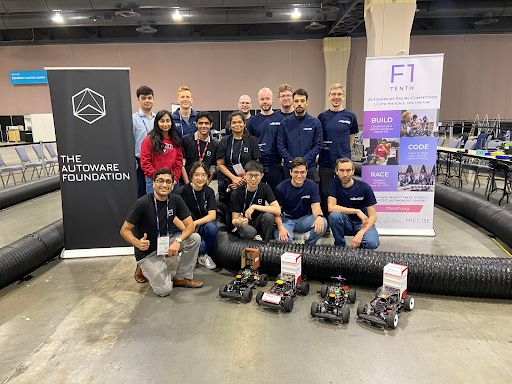
Competitors of the ‘10th F1TENTH Grand Prix’ Competition. Credits: Daniel Carrillo-Zapata
On the industry side of the conference, a robot exhibition hall was prepared with nearly 100 Exhibitors offering robot displays, Tech Huddles, and demos from companies like Dyson, Motional, Built Robotics, Exyn, Ghost Robotics, NVIDIA, Technology Innovation Institute, Boston Dynamics, Pal-Robotics, KUKA Robotics, Amazon Science, Toyota Research Institute, or Tesla, among others. As ICRA 2022 Accessibility Chair Andra Keay (Silicon Valley Robotics), who also Chaired the Startup Forum, commented, “It was incredibly exciting to see such a strong participation from industry at ICRA 2022. Companies were able to showcase their technologies, recruit talented candidates, network with their peers, and discover the latest advances in robotics. Startups also were able to showcase to investors and potential customers. Tech Huddles were a great addition to the program because they gave students and faculty more opportunities to network with industry.”
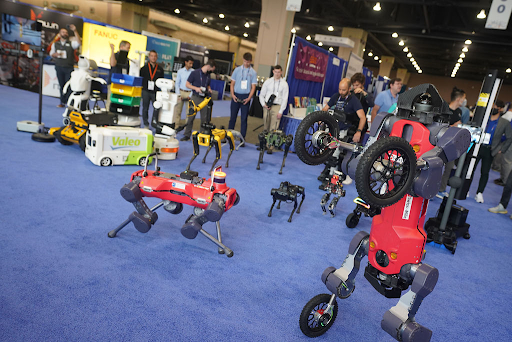
Exhibitors’ robots round-up. Credits: Wise Owl Multimedia
As everyone could not attend ICRA 2022 in person, the Organizing Committee, the IEEE Robotics and Automation Society and OhmniLabs teamed up to offer access to the OhmiLab’s telepresence robots that were on site. Three OhmniBots were in the main exhibition hall (with all the other robots) from opening to closing from Tuesday to Thursday, with time slots aligning with Poster Sessions, networking breaks and Expo Hall hours.
ICRA 2022 continued exploring innovative ways to generate impact on robotics and automation through its partnership with the RAD Lab and several Philadelphia-based art galleries to offer a central space for art in its program. Building on the previous ICRA robotic art programs, this year’s installment explored aesthetic and creative influences on robot motion through interactive, expressive, and meditative robotic art installations. When artist-in-residence from the RAD Lab Kate Ladenheim was interviewed by David Garzón Ramos (IRIDIA) -one of the four ICRA 2022 Science Communication Awardees- about the intersection of robotics and art, she answered, “Roboticists and artists both engage in really intensive creative processes in order to make their work come to life. If a roboticist is trying to make something with a high level of intellectual and conceptual rigor, with an output that is not necessarily commercial in nature but is one that is meant to enrich the lives of people around it, then I think it crosses the realm from a project into a project that is artistic.”
This year’s edition of ICRA was a record-breaking gathering of the top roboticists and stakeholders from academia and industry, having a huge impact on the local and international community. Preparations are already in place for the 40th edition of the conference. ICRA 2023 will take place at ExCeL London between 29 May – 2 June 2023. Kaspar Althoefer (Queen Mary University of London), General Chair of ICRA 2023, stated, “We are looking forward to building on the wonderful success of ICRA 2022 in Philadelphia with the ICRA 2023 conference. The theme of the congress is ‘Embracing the Future. Making Robots for Humans’, and we are planning a wide range of workshops, sessions, networking events and tours to fit in with this theme. We are looking forward to welcoming everyone to London next year!”
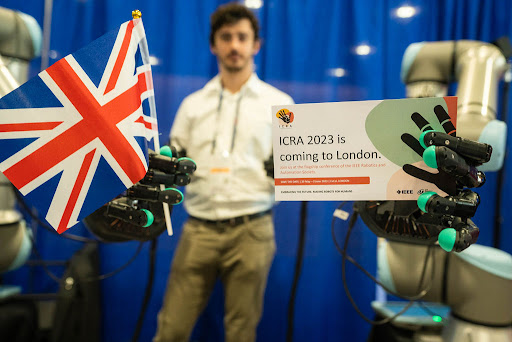
ICRA 2023 will take place in London. Credits: Wise Owl Multimedia
We would like to thank ICRA 2022 Partners, which have also supported us in record numbers this year, as well as all participants, organization members and volunteers. Thank you for coming together again in person and online after a few years apart to imagine a new future where humans and robots work together!