Keeping Your Data Secure 100% Of The Time With VoIP: 5 Things To Implement Right Away
Have you finally ditched landlines for the better and more advanced VoIP? If so, great! There’s so much more than you can get with it compared with the older communication tech. One of our favorite things about it is there’s no business income barrier preventing you from accessing the full potential of the system. You...
The post Keeping Your Data Secure 100% Of The Time With VoIP: 5 Things To Implement Right Away appeared first on 1redDrop.
Sharing a laugh: Scientists teach a robot when to have a sense of humor
Auto supplier bringing electric delivery robots to Detroit
Intelligent cooperation to provide surveillance and epidemic services in smart cities
Expressing and recognizing intentions in robots
Can a robot’s ability to speak affect how much human users trust it?
Tiny, caterpillar-like soft robot folds, rolls, grabs and degrades
ABB survey reveals re-industrialization at risk from global “education gap” in automation
ep.360: Building Communities Around AI in Africa, with Benjamin Rosman
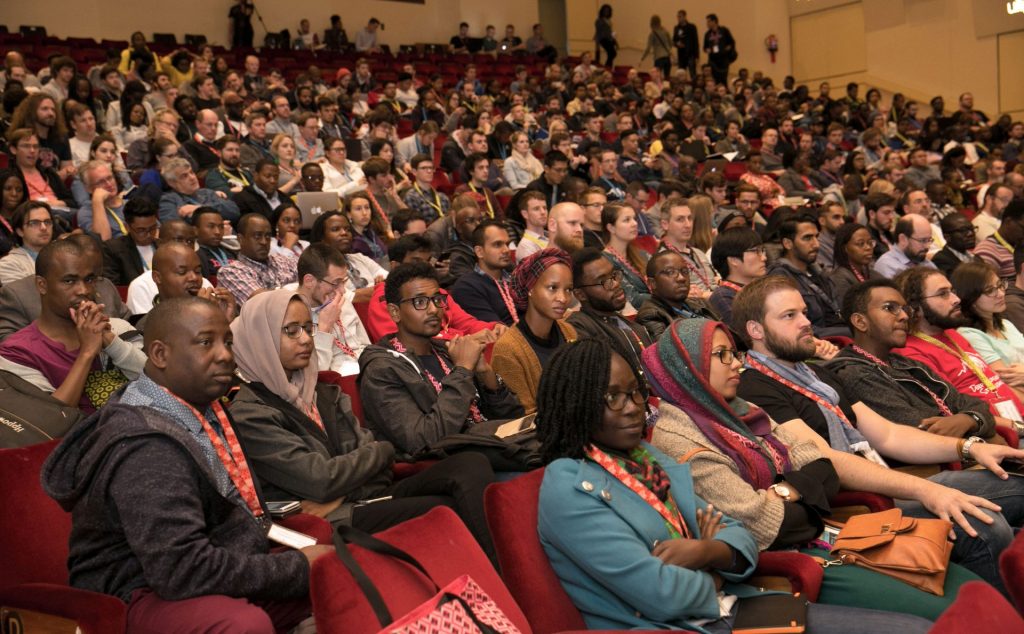
At ICRA 2022, Benjamin Rosman delivered a keynote presentation on an organization he co-founded called “Deep learning Indaba”.
Deep Learning Indaba is based in South Africa and their mission is to strengthen Artificial Intelligence and Machine Learning communities across Africa. They host yearly meetups in varying countries on the continent, as well as promote grass roots communities in each of the countries to run their own local events.
What is Indaba?
An indaba is a Zulu word for a gathering or meeting. Such meetings are held throughout southern Africa, and serve several functions: to listen and share news of members of the community, to discuss common interests and issues facing the community, and to give advice and coach others.
Benjamin Rosman
Benjamin Rosman is an Associate Professor in the School of Computer Science and Applied Mathematics at the University of the Witwatersrand, South Africa, where he runs the Robotics, Autonomous Intelligence, and Learning (RAIL) Laboratory and is the Director of the National E-Science Postgraduate Teaching and Training Platform (NEPTTP).
He is a founder and organizer of the Deep Learning Indaba machine learning summer school, with a focus on strengthening African machine learning. He was a 2017 recipient of a Google Faculty Research Award in machine learning, and a 2021 recipient of a Google Africa Research Award. In 2020, he was made a Senior Member of the IEEE.
Links
- Deep Learning Indaba
- Download mp3
- Subscribe to Robohub using iTunes, RSS, or Spotify
- Support us on Patreon