When humans play in competition with a humanoid robot, they delay their decisions when the robot looks at them
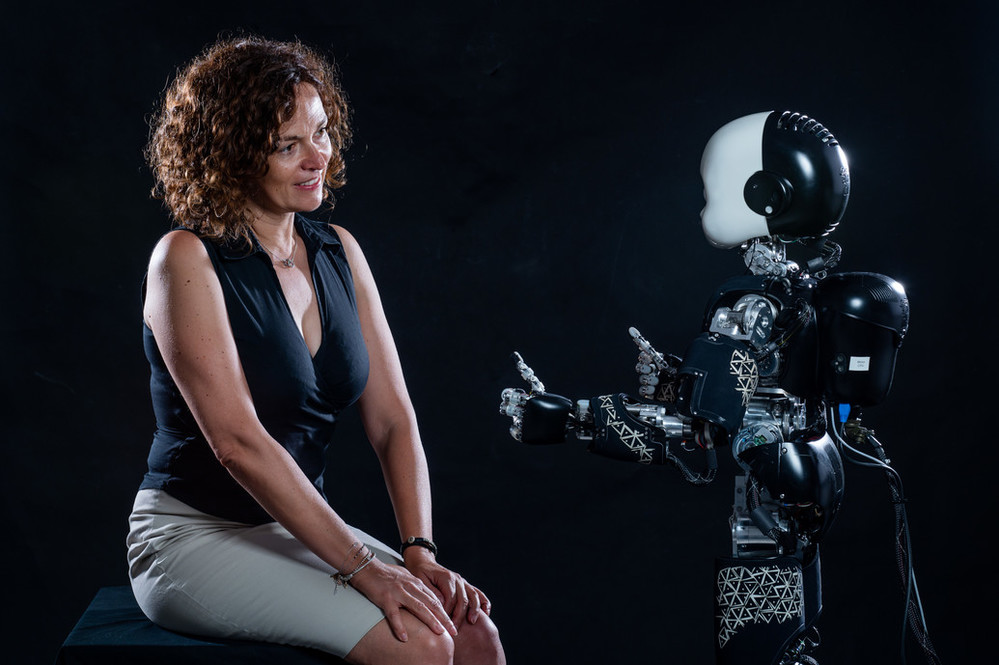
Gaze is an extremely powerful and important signal during human-human communication and interaction, conveying intentions and informing about other’s decisions. What happens when a robot and a human interact looking at each other? Researchers at IIT-Istituto Italiano di Tecnologia (Italian Institute of Technology) investigated whether a humanoid robot’s gaze influences the way people reason in a social decision-making context. What they found is that a mutual gaze with a robot affects human neural activity, influencing decision-making processes, in particular delaying them. Thus, a robot gaze brings humans to perceive it as a social signal. These findings have strong implications for contexts where humanoids may find applications such as co-workers, clinical support or domestic assistants.
The study, published in Science Robotics, has been conceived within the framework of a larger overarching project led by Agnieszka Wykowska, coordinator of IIT’s lab “Social Cognition in Human-Robot Interaction”, and funded by the European Research Council (ERC). The project, called “InStance”, addresses the question of when and under what conditions people treat robots as intentional beings. That is, whether, in order to explain and interpret robot’s behaviour, people refer to mental states such as beliefs or desires.
The research paper’s authors are Marwen Belkaid, Kyveli Kompatsiari, Davide de Tommaso, Ingrid Zablith, and Agnieszka Wykowska.
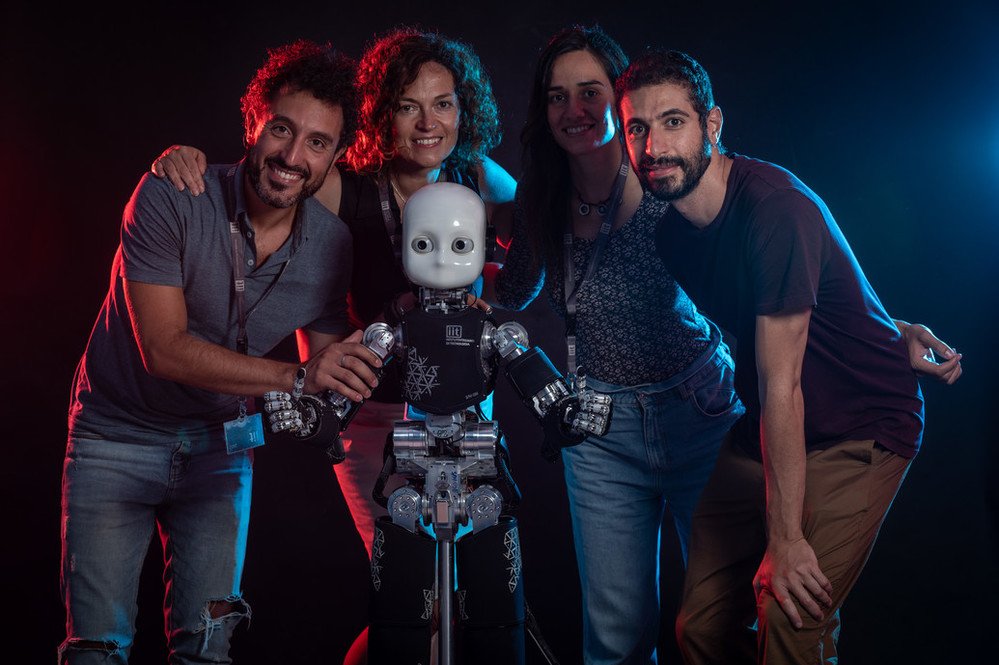
In most everyday life situations, the human brain needs to engage not only in making decisions, but also in anticipating and predicting the behaviour of others. In such contexts, gaze can be highly informative about others’ intentions, goals and upcoming decisions. Humans pay attention to the eyes of others, and the brain reacts very strongly when someone looks at them or directs gaze to a certain event or location in the environment. Researchers investigated this kind of interaction with a robot.
“Robots will be more and more present in our everyday life” comments Agnieszka Wykowska, Principal Investigator at IIT and senior author of the paper. “That is why it is important to understand not only the technological aspects of robot design, but also the human side of the human-robot interaction. Specifically, it is important to understand how the human brain processes behavioral signals conveyed by robots”.
Wykowska and her research group, asked a group of 40 participants to play a strategic game – the Chicken game – with the robot iCub while they measured the participants’ behaviour and neural activity, the latter by means of electroencephalography (EEG). The game is a strategic one, depicting a situation in which two drivers of simulated cars move towards each other on a collision course and the outcome depends on whether the players yield or keep going straight.
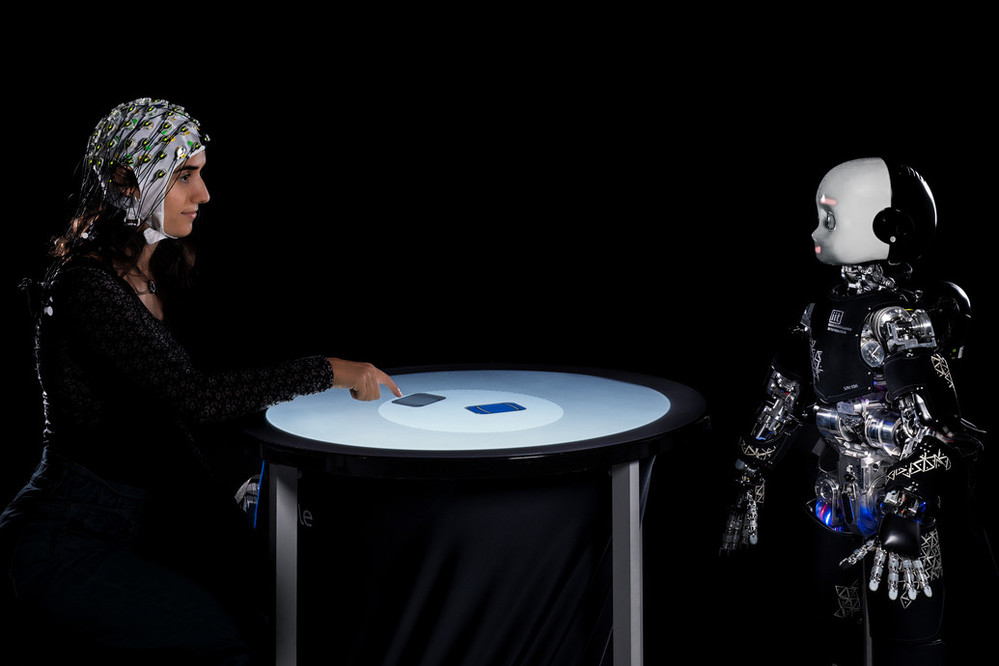
Researchers found that participants were slower to respond when iCub established mutual gaze during decision making, relative to averted gaze. The delayed responses may suggest that mutual gaze entailed a higher cognitive effort, for example by eliciting more reasoning about iCub’s choices or higher degree of suppression of the potentially distracting gaze stimulus, which was irrelevant to the task.
“Think of playing poker with a robot. If the robot looks at you during the moment you need to make a decision on the next move, you will have a more difficult time in making a decision, relative to a situation when the robot gazes away. Your brain will also need to employ effortful and costly processes to try to “ignore” that gaze of the robot” explains further Wykowska.
These results suggest that the robot’s gaze “hijacks” the “socio-cognitive” mechanisms of the human brain – making the brain respond to the robot as if it was a social agent. In this sense, “being social” for a robot could be not always beneficial for the humans, interfering with their performance and speed of decision making, even if their reciprocal interaction is enjoyable and engaging.
Wykowska and her research group hope that these findings would help roboticists design robots that exhibit the behaviour that is most appropriate for a specific context of application. Humanoids with social behaviours may be helpful in assisting in care elderly or childcare, as in the case of the iCub robot, being part of experimental therapy in the treatment of autism. On the other hand, when focus on the task is needed, as in factory settings or in air traffic control, presence of a robot with social signals might be distracting.
Super-stretchy wormlike robots capable of ‘feeling’ their surroundings
#IROS2020 Real Roboticist focus series #5: Michelle Johnson (Robots That Matter)
We’re reaching the end of this focus series on IEEE/RSJ IROS 2020 (International Conference on Intelligent Robots and Systems) original series Real Roboticist. This week you’ll meet Michelle Johnson, Associate Professor of Physical Medicine and Rehabilitation at the University of Pennsylvania.
Michelle is also the Director of the Rehabilitation Robotics Lab at the University of Pennsylvania, whose aim is to use rehabilitation robotics and neuroscience to investigate brain plasticity and motor function after non-traumatic brain injuries, for example in stroke survivors or persons diagnosed with cerebral palsy. If you’d like to know more about her professional journey, her work with affordable robots for low/middle income countries and her next frontier in robotics, among many more things, check out her video below!
How Implementing Robotics Affects Business Insurance
When mud is our greatest teacher
On 25 March, a small RoboHouse team went out in the fields of Oldeberkoop in East Friesland with gas leak detector Waylon and mechanic Rob. They began by checking the calibration to prevent malfunctions. Then they cleaned the detector mat and changed the filter, after which the search could start.
The two men proceeded slowly, constantly checking their tablet to see whether they were still close enough to the pipes. A big cart was pushed forward with the mat dragging behind it. Except for the grinding of the equipment on the sidewalk, everything was quiet.
The team waited to hear from the device, which is supposed to sound an alarm when it detects a leak. And then they heard it: a beep! After taking a few steps back, because the system lags, Rob sprayed a yellow dot. Waylon pointed to the beauty of the on-screen image that enables assessment of the severity of the leak. “It’s not a biggie”, Waylon said to the RoboHouse team. That means someone will come within a week to measure it again, before calling for a repair.
The team slowly walked on, looking for more leaks. When they bumped into any kind of obstacle, they had to lift the device over it themselves. They also pushed the big device while constantly looking down on their tablet. After a full day of leak detection, every member of the team could feel it in their shoulders.
The RoboHouse team then realised how easily bad ergonomics can lead to injuries. There have been tests with more expensive machines and Segways but a solution has not yet been found. So our ambition remains: develop robotic technology that transforms the daily grind of leak detection, but stay modest and don’t overestimate our progress.
At RoboHouse, the process of improving working life starts with the worker. “Research, development and co-creation go hand in hand to deploy robotics in the best way possible,” says Marieke Mulder, program manager. “The goal is to support 90% of the work in gas leak detection autonomously so Rob and Waylon can make the pipelines safe and future proof.”
The field research sparked many new ideas. Waylon was curious about next steps and Rob said: “I just hope we can come up with something that allows me to take the right routes without destroying my back by looking at the tablet all day”.
After the field session, the team from RoboHouse gathered experts from different sectors to analyse the challenges at hand and co-create the first concepts towards a solution. Development engineers Bas van Mil, Tom Dalhuisen and Guus Paris joined the team online in a workshop on Miro. Together they envisioned a way forward and this was translated into a roadmap to 2031 by the RoboHouse team.
There will be many interactions with workers at Alliander along the way, and many more hours in the field. Marieke Mulder says: “After walking just a mile through the mud, we have barely begun to know how it is to do this work every day. But by going beyond our lab, into the field, we already discovered so much more about the challenges that workers like Rob and Waylon face every day.”
The post When mud is our greatest teacher appeared first on RoboHouse.
Los Angeles is about to get its first robotaxi test fleet
Soft perching robot validates the benefit of having a fifth leg
Robot Control: Using Native Programming Language or an External Controller?
Artificial fiber spun from liquid crystal elastomer using electricity performs like human muscle fiber
Researchers develop bionic arm that restores natural behaviors in patients with upper limb amputations
Grubhub testing delivery robots
DefGraspSim: A pipeline to evaluate robotic grasping of 3D deformable objects
Standards, Guidelines & Industry Best Practices for Industrial & Collaborative Robots
#IROS2020 Plenary and Keynote talks focus series #5: Nikolaus Correll & Cynthia Breazeal
As part of our series showcasing the plenary and keynote talks from the IEEE/RSJ IROS2020 (International Conference on Intelligent Robots and Systems), this week we bring you Nikolaus Correll (Associate Professor at the University of Colorado at Boulder) and Cynthia Breazeal (Professor of Media Arts and Sciences at MIT). Nikolaus’ talk is on the topic of robot manipulation, while Cynthia’s talk is about the topic of social robots.
|
Prof. Nikolaus Correll – Robots Getting a Grip on General Manipulation Bio: Nikolaus Correll is an Associate Professor at the University of Colorado at Boulder. He obtained his MS in Electrical Engineering from ETH Zürich and his PhD in Computer Science from EPF Lausanne in 2007. From 2007-2009 he was a post-doc at MIT’s Computer Science and Artificial Intelligence Lab (CSAIL). Nikolaus is the recipient of a NSF CAREER award, a NASA Early Career Faculty Fellowship and a Provost Faculty achievement award. In 2016, he founded Robotic Materials Inc. to commercialize robotic manipulation technology. |
|
Prof. Cynthia Breazeal – Living with Social Robots: from Research to Commercialization and Back Abstract: Social robots are designed to interact with people in an interpersonal way, engaging and supporting collaborative social and emotive behavior for beneficial outcomes. We develop adaptive algorithmic capabilities and deploy multitudes of cloud-connected robots in schools, homes, and other living facilities to support long-term interpersonal engagement and personalization of specific interventions. We examine the impact of the robot’s social embodiment, emotive and relational attributes, and personalization capabilities on sustaining people’s engagement, improving learning, impacting behavior, and shaping attitudes to help people achieve long-term goals. I will also highlight challenges and opportunities in commercializing social robot technologies for impact at scale. In a time where citizens are beginning to live with intelligent machines on a daily basis, we have the opportunity to explore, develop, study, and assess humanistic design principles to support and promote human flourishing at all ages and stages. Bio: Cynthia Breazeal is a Professor at the MIT Media Lab where she founded and Directs the Personal Robots Group. She is also Associate Director of the Media Lab in charge of new strategic initiatives, and she is spearheading MIT’s K-12 education initiative on AI in collaboration with the Media Lab, Open Learning and the Schwarzman College of Computing. She is recognized as a pioneer in the field of social robotics and human-robot interaction and is a AAAI Fellow. She is a recipient of awards by the National Academy of Engineering as well as the National Design Awards. She has received Technology Review’s TR100/35 Award and the George R. Stibitz Computer & Communications Pioneer Award. She has also been recognized as an award-winning entrepreneur, designer and innovator by CES, Fast Company, Entrepreneur Magazine, Forbes, and Core 77 to name a few. Her robots have been recognized by TIME magazine’s Best Inventions in 2008 and in 2017 where her award-wining Jibo robot was featured on the cover. She received her doctorate from MIT in Electrical Engineering and Computer Science in 2000. |