Robot performs first laparoscopic surgery without human help
In picking up trash, robots pick up new approaches to work
Digital Transformation and Industrial Robots Outlook
Kirigami robotic grippers are delicate enough to lift egg yolks
Matt Robinson: Accelerating Industrial Workflows with Open Source | Sense Think Act Podcast #12
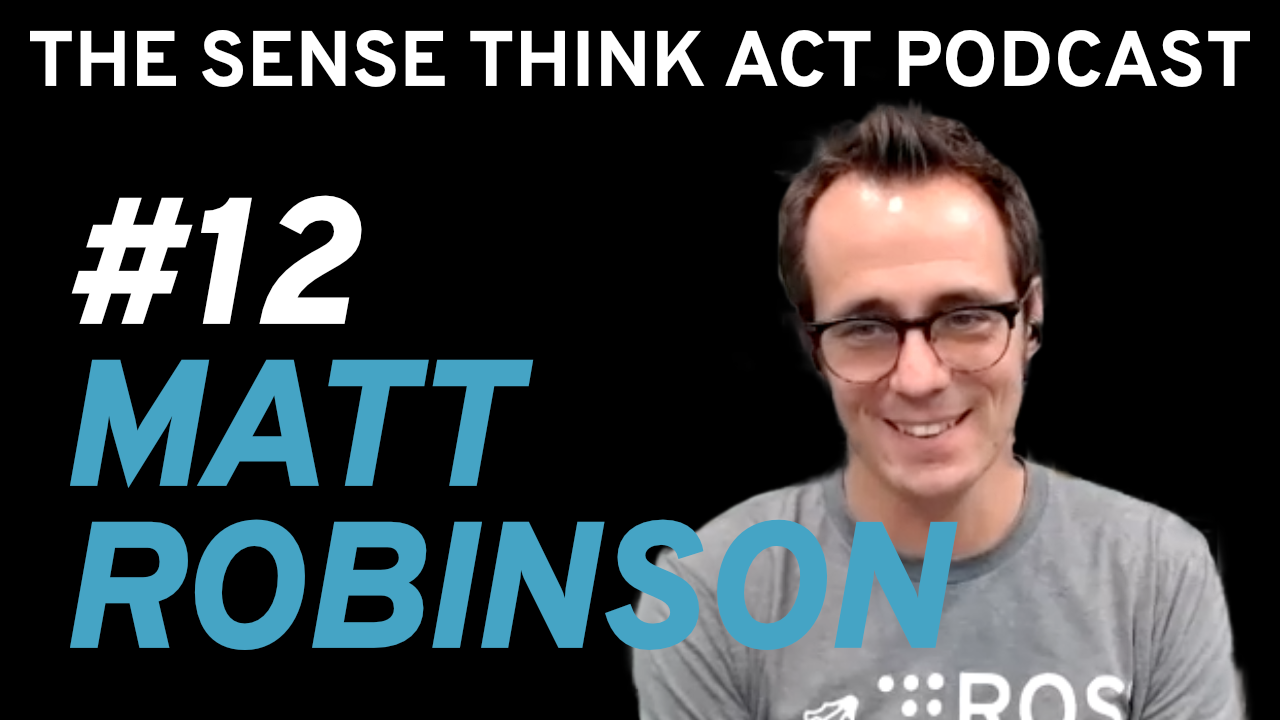
In this episode, Audrow Nash speaks to Matt Robinson, Program Manager for ROS-Industrial Americas at the Southwest Research Institute. ROS Industrial is a group that seeks to help industrial users, for example factories, leverage ROS and its ecosystem. In this conversation, they talk about Matt’s background, the need for the ROS-Industrial group and what problems they’re working to solve, ROS-Industrial’s consortium, and ROS-Industrial’s new working group.
Episode Links
- Download the episode
- ROS-Industrial
- ROS-Industrial’s Twitter
- ROS-Industrial’s Discourse
- Southwest Research Institute
Podcast info
Learning for Collaboration, Not Competition
Jakob Foerster an accredited Machine Learning Research Scientist who has been at the forefront of research on Multi-Agent Learning speaks with interviewer Kegan Strawn.
Dr. Foerster explains why incorporating uncertainty into multi-agent interactions is essential to creating robust algorithms that can operate not only in games but in real-world applications.
Jakob Foerster
Jakob Foerster is an Associate Professor at the University of Oxford. His papers have gained prestigious awards at top machine learning conferences (ICML, AAAI) and have helped push deep multi-agent reinforcement learning to the forefront of AI research.
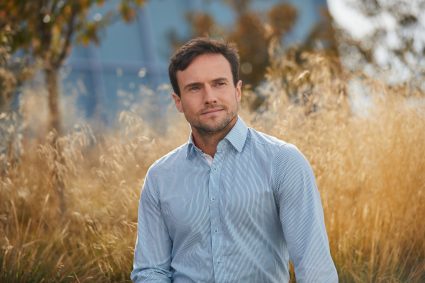
Jakob previously worked at Facebook AI Research and received his Ph.D. from the University of Oxford under the supervision of Shimon Whiteson. During his Ph.D., Jakob also interned at Google Brain, OpenAI, and DeepMind.
Jakob’s research interests span Deep Multi-Agent Reinforcement Learning, Human-AI Coordination, Emergent Communication, Search, Planning, and Game Theory.
Links
- Download mp3 (36.4 MB)
- Subscribe to Robohub using iTunes, RSS, or Spotify
- Support us on Patreon
Naïo Technologies Unsupervised Work of its Full Range of Robots
Tamim Asfour’s Keynote talk – Learning humanoid manipulation from humans
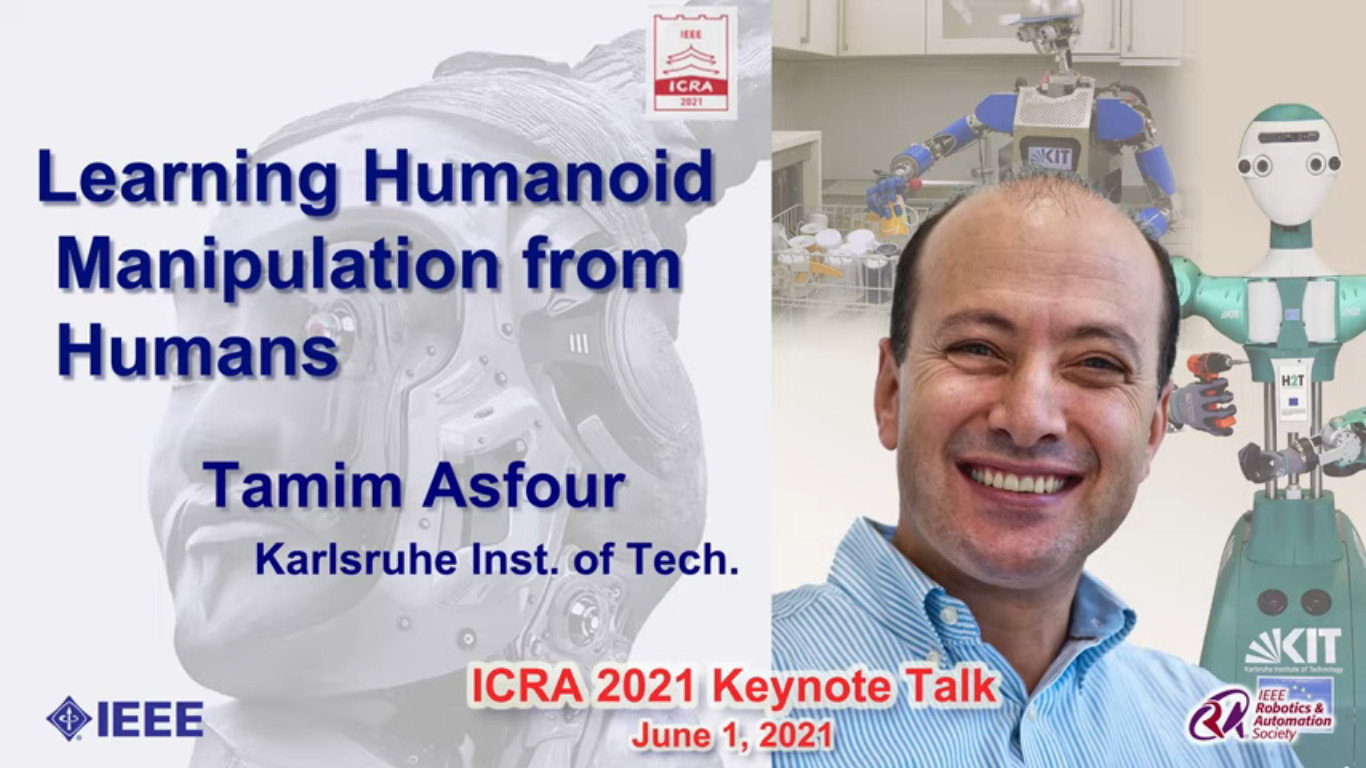
Through manipulation, a robotic system can physically change the state of the world. This is intertwined with intelligence, which is the ability whereby such system can detect and adapt to change. In his talk, Tamim Asfour gives an overview of the developments in manipulation for robotic systems his lab has done by learning manipulation task models from human observations, and the challenges and open questions associated with this.
Bio: Tamim Asfour is full Professor at the Institute for Anthropomatics and Robotics, where he holds the chair of Humanoid Robotics Systems and is head of the High Performance Humanoid Technologies Lab (H2T). His current research interest is high performance 24/7 humanoid robotics. Specifically, his research focuses on engineering humanoid robot systems integrating the mechano-informatics of such systems with the capabilities of predicting, acting and learning from human demonstration and sensorimotor experience. He is developer and the leader of the development team of the ARMAR humanoid robot family.
Improving algorithms in drones to increase their usability
Soft Robotics Set to Unveil mGripAI™ at the International Processing and Production Expo
Robot science fiction books of 2021
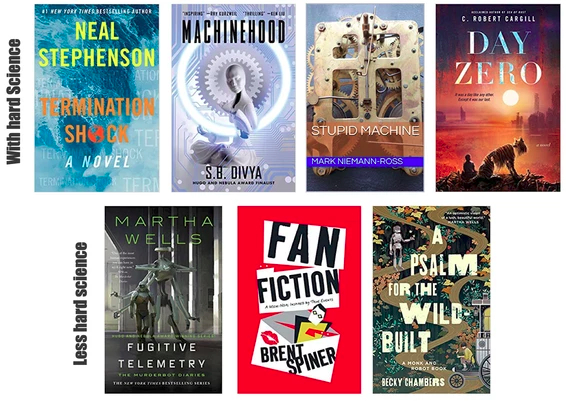
Scifi robot books of 2021
2021 produced four new scifi books with good hard science underpinning their description of robots and three where there was less science but lots of interesting ideas about robots. Not only are these books enjoyable on their own, fiction can serve as teachable moments in robots and STEM and inspire a robot-obsessed teen to read more and improve their reading comprehension.
- Termination Shock
- Machinehood
- Stupid Machine
- Day Zero
- Fugitive Telemetry
- Fan Fiction
- A Psalm for the Wild-Built
Let’s start with the scifi book I most frequently recommended to friends to read in 2021: Termination Shock by Neal Stephenson. It is not a robot book per se but robots and automation are realistically interspersed through it- and the book is one of Stephenson’s best, pulling together LOTS of technology, subplots, and themes similar to what he did in Diamond Age. One of the technology threads is how drones are ubiquitous throughout the book, with small drones being used singly or in swarms for surveillance and social media and bigger drones used for delivery, human transport, and, well, mayhem. Nominally the book is about climate change and how a group of individuals led by a rich Texan plan to cut through the COP26 meetings blather and get on with geoengineering the environment. Except money and geoengineering is the easy part… It’s a dramedy of a book and manages to never lecture or push political agendas, instead it is hard science wrapped with memorable characters, a compelling plot, and a sense of humor, with an “oh my!” twist at the end.
A great way to think about how drones are becoming subtly integrated as tools into military, security, and journalism. And that at the end of the day, despite the huge investment in anti-drone technology, a shotgun with bird shot may be our best defense for small drones. Check out the RTSF topics page for more links to the science.
Unlike Termination Shock, robots and AI *are* the subject of S.B. Divya’s Machinehood. It’s a thorny book with a piercingly sharp commentary on the gig economy, climate change, automation, and ethics. A rogue neo-Buddhist decides that intelligent machines deserve legal rights and protections, similar to animals, which she calls the Machinehood Manifesto. Then she leads a terrorist cell to force governments to incorporate machinehood protections into their legal framework. A SpecialOps operator is tasked to take her down, which she does with the help of her sister-in-law. Lots of action, lots of ideas, lots of realism and full of thought provoking jabs. The book echoes real-world arguments since the 1980’s about treating robots as animals from a legal perspective.
It is a wonderful, very useful introduction to issues in robot ethics and autonomy and the very real concept of treating robots like animals- which is covered in the non-fiction book The New Breed by Kate Darling. You can read more about that in my recent Science Robotics article.
Stupid Machine by Mark Niemann-Ross is a comedy with an interesting and timely plot about autonomous cars, cyber hackers, and social justice warriors in Portland. It would be tempting to hack an autonomous car to drive an annoying semi-full time, I-protest-everything activist off a bridge, wouldn’t it? Plus there is a nice Ubik-like smart house subplot. Not as well-written, plotted, and memorable as Termination Shock and Machinehood, but a quick, easy read.
The idea that autonomous cars will be both ubiquitous and hackable makes it a nice teachable moment about cybersecurity. A recent scifi book that explains more about the workings of autonomous driving is David Walton’s There Laws Lethal. You can read my Science Robotics article on autonomous cars in scifi here.
Like Machinehood, Day Zero by C. Robert Cargill is set a near future. It’s the prequel to Sea of Rust, one of my all time favorite robot scifi books. Sea of Rust is an evocative story about what happens after the robot revolution and how the robots themselves descend into a kind of Mad Max hell. Day Zero isn’t as striking as Sea of Rust, but very enjoyable as a prequel. If you loved Spielberg’s AI: Artificial Intelligence, then you’ll doubly love Day Zero because it is told from the POV of Pounce, the Teddy-like robot, who protects his boy Ezra during the robot revolution. You don’t have to read Sea of Rust first, Day Zero is a stand alone, but I recommend you do. I hope there are more books in the Sea of Rust series.!
In terms of robotics, Day Zero is a good introduction to nursebots, healthcare robots, and domestic assistance robots. You can learn more about the science of nannybots at the Science Robotics article and domestic robotics, sometimes called domotics at Science Robotics here.
Of course, there was a lot of other robot science fiction in 2021, just with less science. Here are three books for you to consider that have some robots in with real world science.
The Murderbot Diaries by Martha Wells is one of my top “you’ve got to read!” The latest addition, Fugitive Telemetry, continues the delightful Bildungsroman of the galaxy’s snarkiest robot. ROFL as always, it maintains the usual clever plotting and action that makes the Murderbot Diaries a favorite of both the Hugos and Nebulas awards. And Murderbot, like the humans in Termination Shock, has a swarm of drones and knows how to use them. Oh, SecUnit, I love you!
And I love the series as way of illustrating real-world problems in software engineering and cybersecurity for robotics. Check out the discussions of software engineering in the first book and the Internet of Things in the fourth.
It’s hard not to like Lieutenant Commander Data on Star Trek and Picard, right? Well, it’s hard not to like Brent Spiner, the nice Jewish boy from Houston who grew up to write a funny, self-mocking semi-fictional autobiography as well as star in a hit TV series. He calls his book, Fan Fiction, a “mem-noir” where an actor, conveniently named Brent Spiner, on the third season of a modest hit conveniently called “ST:TNG” is being stalked by a someone purported to be Lal, Data’s short-lived robot daughter. The hapless actor finds it is as if he is living in a Raymond Chandler novel. Brent reflects on his life and how he got to this point in his career as he tries to go about shooting episodes, going to parties at the Roddenberrys, signing autographs at cons, and hanging out with Patrick Stewart, Levar Burton, and Jonathan Frakes. Yet Spiner comes across as a regular guy, grounded and grateful- and amused- at “making it” in Hollywood. It makes me long for a follow up- what was life for that actor after the years of grueling 16 hour days on set and the increasing fame?
OK, there is not much there in terms of teachable moments about robots, but it is still fun.
A Psalm for the Wild-Built by Becky Chambers, the reigning comfort lit scifi writer (and that’s a good thing!), is a sentimental Solar-punk book. The book doesn’t have a lot of action but could be perfect for middle schoolers (though some f-bombs are dropped) or a read-aloud to younger children. Or something to just to enjoy instead of listening to Lake Woebegone tales or re-reading Cadfael books. The premise is that in a future world, robots spontaneously gained sentience and then left human occupied terrorizes to explore being a robot. Now they are back, self-actualized, and ready to explore humanity by asking “what do humans need?”
Doesn’t sound like there’s much about real robots, does it? And yet, it has one of the most cogent explanations of agency, of what makes something more than a machine, which is a fundamental concept in artificial intelligence and in how autonomy is different than automation.
Hopefully this list of books gives you something to read and, more importantly, something to think about in 2022!
Innovative AI Targets the Problem of Drivable Path Detection in Winter Weather
How robots learn to hike
How robots learn to hike
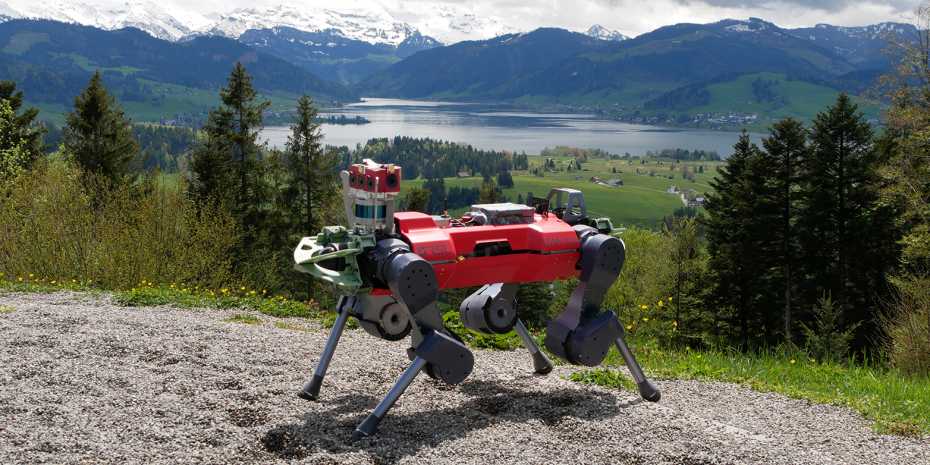
The legged robot ANYmal on the rocky path to the summit of Mount Etzel, which stands 1,098 metres above sea level. (Photo: Takahiro Miki)
By Christoph Elhardt
Steep sections on slippery ground, high steps, scree and forest trails full of roots: the path up the 1,098-metre-high Mount Etzel at the southern end of Lake Zurich is peppered with numerous obstacles. But ANYmal, the quadrupedal robot from the Robotic Systems Lab at ETH Zurich, overcomes the 120 vertical metres effortlessly in a 31-minute hike. That’s 4 minutes faster than the estimated duration for human hikers – and with no falls or missteps.
This is made possible by a new control technology, which researchers at ETH Zurich led by robotics professor Marco Hutter recently presented in the journal Science Robotics. “The robot has learned to combine visual perception of its environment with proprioception – its sense of touch – based on direct leg contact. This allows it to tackle rough terrain faster, more efficiently and, above all, more robustly,” Hutter says. In the future, ANYmal can be used anywhere that is too dangerous for humans or too impassable for other robots.
Video: Nicole Davidson / ETH Zurich
Perceiving the environment accurately
To navigate difficult terrain, humans and animals quite automatically combine the visual perception of their environment with the proprioception of their legs and hands. This allows them to easily handle slippery or soft ground and move around with confidence, even when visibility is low. Until now, legged robots have been able to do this only to a limited extent.
“The reason is that the information about the immediate environment recorded by laser sensors and cameras is often incomplete and ambiguous,” explains Takahiro Miki, a doctoral student in Hutter’s group and lead author of the study. For example, tall grass, shallow puddles or snow appear as insurmountable obstacles or are partially invisible, even though the robot could actually traverse them. In addition, the robot’s view can be obscured in the field by difficult lighting conditions, dust or fog.
“That’s why robots like ANYmal have to be able to decide for themselves when to trust the visual perception of their environment and move forward briskly, and when it is better to proceed cautiously and with small steps,” Miki says. “And that’s the big challenge.”
A virtual training camp
Thanks to a new controller based on a neural network, the legged robot ANYmal, which was developed by ETH Zurich researchers and commercialized by the ETH spin-off ANYbotics, is now able to combine external and proprioceptive perception for the first time. Before the robot could put its capabilities to the test in the real world, the scientists exposed the system to numerous obstacles and sources of error in a virtual training camp. This let the network learn the ideal way for the robot to overcome obstacles, as well as when it can rely on environmental data – and when it would do better to ignore that data.
“With this training, the robot is able to master the most difficult natural terrain without having seen it before,” says ETH Zurich Professor Hutter. This works even if the sensor data on the immediate environment is ambiguous or vague. ANYmal then plays it safe and relies on its proprioception. According to Hutter, this allows the robot to combine the best of both worlds: the speed and efficiency of external sensing and the safety of proprioceptive sensing.
Use under extreme conditions
Whether after an earthquake, after a nuclear disaster, or during a forest fire, robots like ANYmal can be used primarily wherever it is too dangerous for humans and where other robots cannot cope with the difficult terrain.
In September of last year, ANYmal was able to demonstrate just how well the new control technology works at the DARPA Subterranean Challenge, the world’s best-known robotics competition. The ETH Zurich robot automatically and quickly overcame numerous obstacles and difficult terrain while autonomously exploring an underground system of narrow tunnels, caves, and urban infrastructure. This was a major part of why the ETH Zurich researchers, as part of the CERBERUS team, took first place with a prize of 2 million dollars.