A new type of material called a mechanical neural network can learn and change its physical properties to create adaptable, strong structures
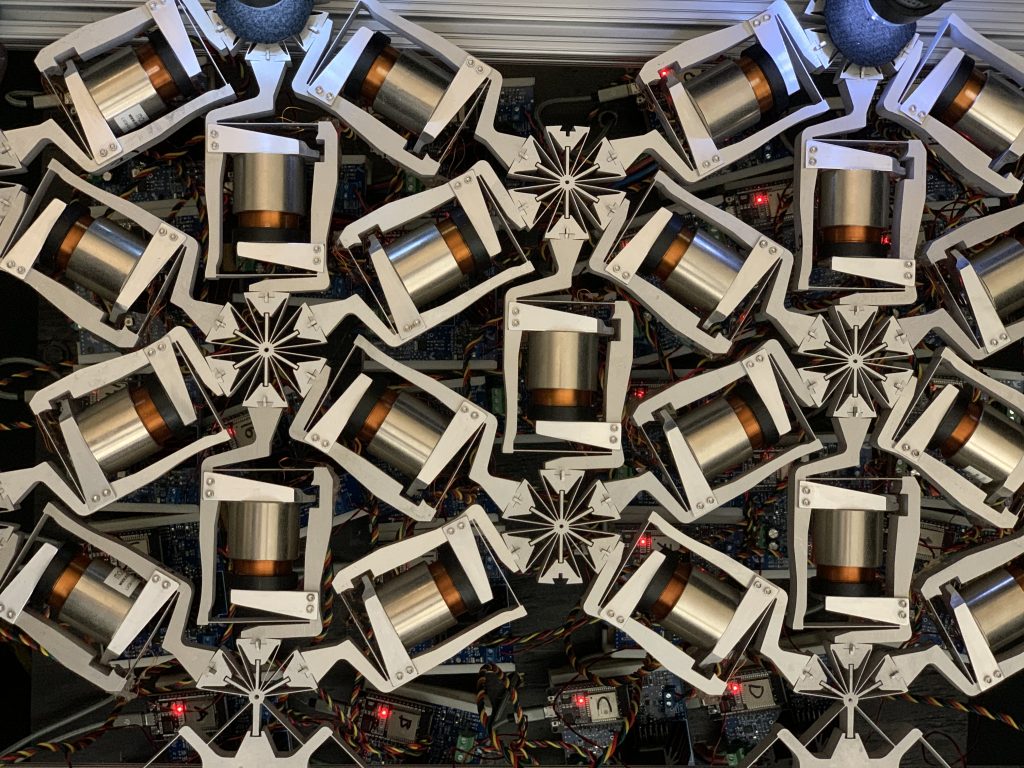
This connection of springs is a new type of material that can change shape and learn new properties. Jonathan Hopkins, CC BY-ND
By Ryan H. Lee (PhD Student in Mechanical and Aerospace Engineering, University of California, Los Angeles)
A new type of material can learn and improve its ability to deal with unexpected forces thanks to a unique lattice structure with connections of variable stiffness, as described in a new paper by my colleagues and me.
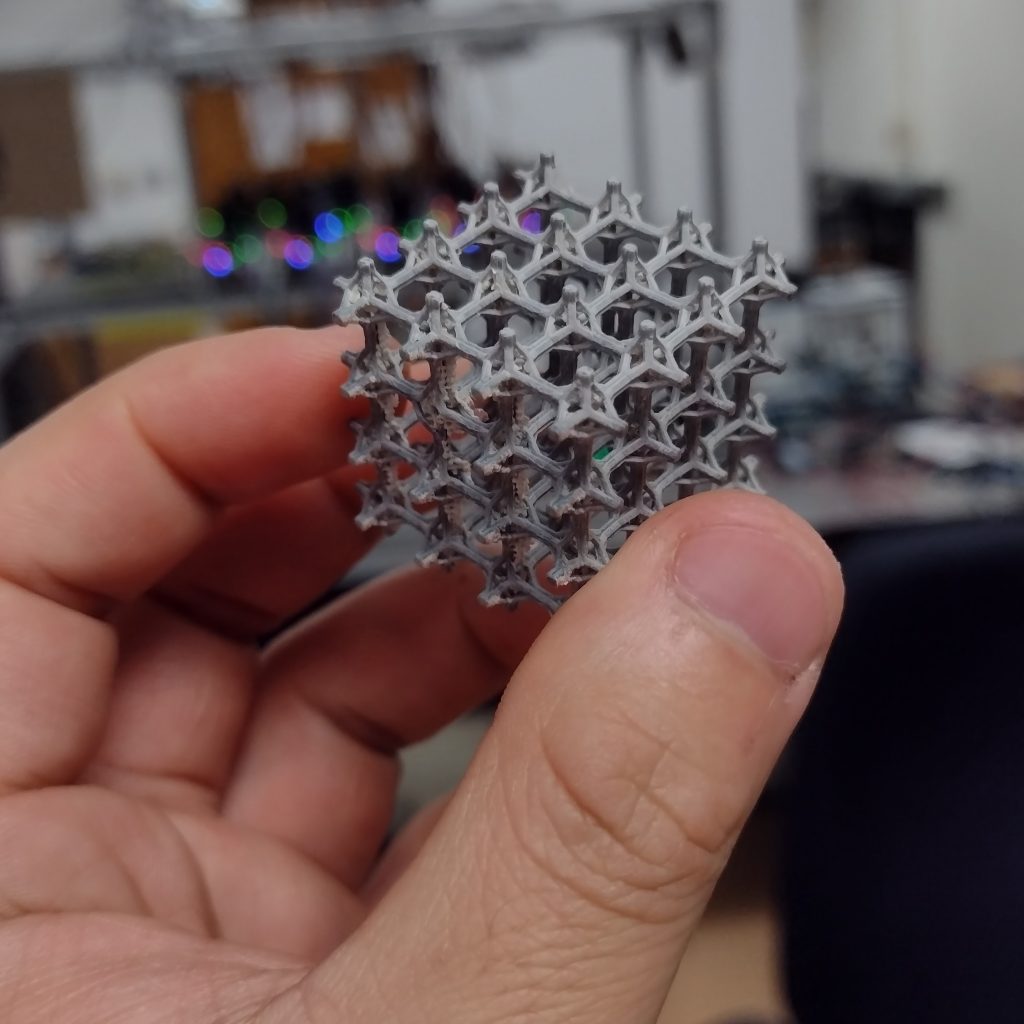
Architected materials – like this 3D lattice – get their properties not from what they are made out of, but from their structure. Ryan Lee, CC BY-ND
The new material is a type of architected material, which gets its properties mainly from the geometry and specific traits of its design rather than what it is made out of. Take hook-and-loop fabric closures like Velcro, for example. It doesn’t matter whether it is made from cotton, plastic or any other substance. As long as one side is a fabric with stiff hooks and the other side has fluffy loops, the material will have the sticky properties of Velcro.
My colleagues and I based our new material’s architecture on that of an artificial neural network – layers of interconnected nodes that can learn to do tasks by changing how much importance, or weight, they place on each connection. We hypothesized that a mechanical lattice with physical nodes could be trained to take on certain mechanical properties by adjusting each connection’s rigidity.
To find out if a mechanical lattice would be able to adopt and maintain new properties – like taking on a new shape or changing directional strength – we started off by building a computer model. We then selected a desired shape for the material as well as input forces and had a computer algorithm tune the tensions of the connections so that the input forces would produce the desired shape. We did this training on 200 different lattice structures and found that a triangular lattice was best at achieving all of the shapes we tested.
Once the many connections are tuned to achieve a set of tasks, the material will continue to react in the desired way. The training is – in a sense – remembered in the structure of the material itself.
We then built a physical prototype lattice with adjustable electromechanical springs arranged in a triangular lattice. The prototype is made of 6-inch connections and is about 2 feet long by 1½ feet wide. And it worked. When the lattice and algorithm worked together, the material was able to learn and change shape in particular ways when subjected to different forces. We call this new material a mechanical neural network.
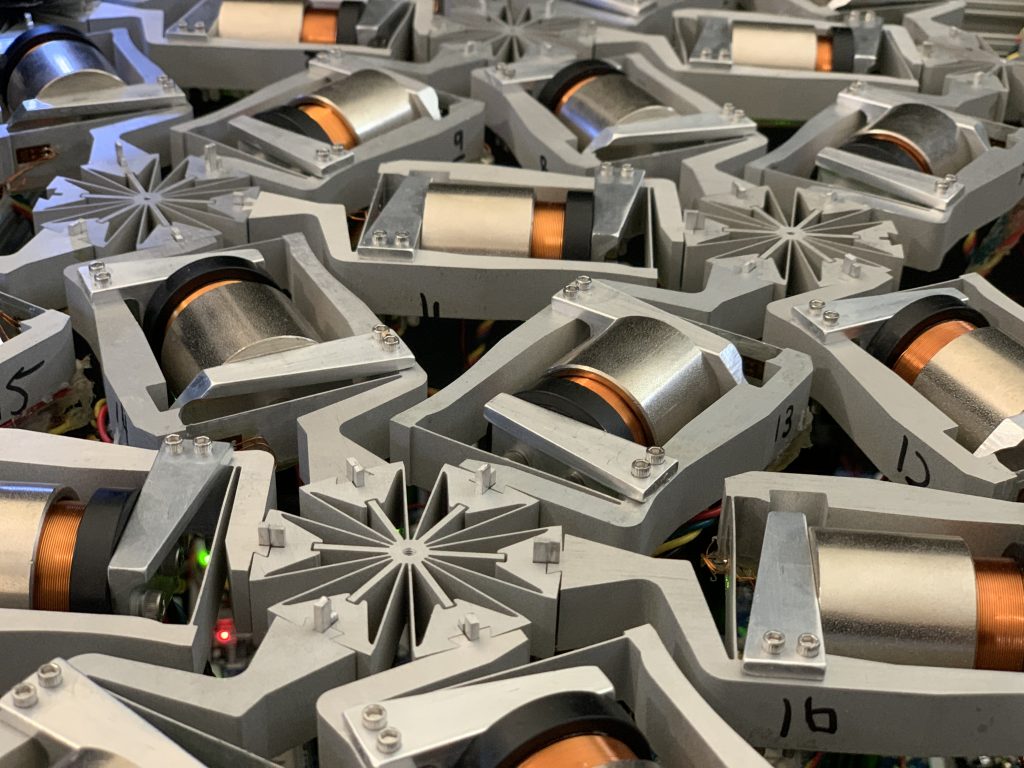
The prototype is 2D, but a 3D version of this material could have many uses. Jonathan Hopkins, CC BY-ND
Why it matters
Besides some living tissues, very few materials can learn to be better at dealing with unanticipated loads. Imagine a plane wing that suddenly catches a gust of wind and is forced in an unanticipated direction. The wing can’t change its design to be stronger in that direction.
The prototype lattice material we designed can adapt to changing or unknown conditions. In a wing, for example, these changes could be the accumulation of internal damage, changes in how the wing is attached to a craft or fluctuating external loads. Every time a wing made out of a mechanical neural network experienced one of these scenarios, it could strengthen and soften its connections to maintain desired attributes like directional strength. Over time, through successive adjustments made by the algorithm, the wing adopts and maintains new properties, adding each behavior to the rest as a sort of muscle memory.
This type of material could have far reaching applications for the longevity and efficiency of built structures. Not only could a wing made of a mechanical neural network material be stronger, it could also be trained to morph into shapes that maximize fuel efficiency in response to changing conditions around it.
What’s still not known
So far, our team has worked only with 2D lattices. But using computer modeling, we predict that 3D lattices would have a much larger capacity for learning and adaptation. This increase is due to the fact that a 3D structure could have tens of times more connections, or springs, that don’t intersect with one another. However, the mechanisms we used in our first model are far too complex to support in a large 3D structure.
What’s next
The material my colleagues and I created is a proof of concept and shows the potential of mechanical neural networks. But to bring this idea into the real world will require figuring out how to make the individual pieces smaller and with precise properties of flex and tension.
We hope new research in the manufacturing of materials at the micron scale, as well as work on new materials with adjustable stiffness, will lead to advances that make powerful smart mechanical neural networks with micron-scale elements and dense 3D connections a ubiquitous reality in the near future.

Ryan Lee has received funding from the Air Force Office of Science Research .
This article appeared in The Conversation.
Robotics Plus unveils autonomous modular vehicle to alleviate agriculture labour shortages
AI material that learns behaviors and adapts to changing conditions
What Does E.M.I.L.Y. Mean for the Future of Robot-Assisted Rescue?
‘Killer robots’ will be nothing like the movies show – here’s where the real threats lie
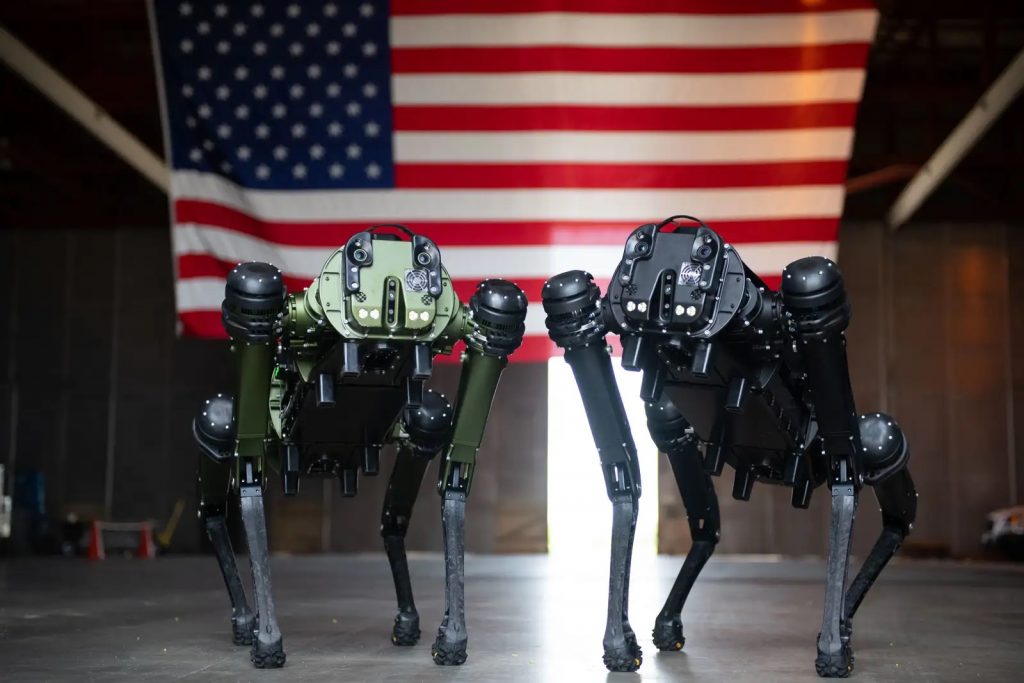
Ghost Robotics Vision 60 Q-UGV. US Space Force photo by Senior Airman Samuel Becker
By Toby Walsh (Professor of AI at UNSW, Research Group Leader, UNSW Sydney)
You might suppose Hollywood is good at predicting the future. Indeed, Robert Wallace, head of the CIA’s Office of Technical Service and the US equivalent of MI6’s fictional Q, has recounted how Russian spies would watch the latest Bond movie to see what technologies might be coming their way.
Hollywood’s continuing obsession with killer robots might therefore be of significant concern. The newest such movie is Apple TV’s forthcoming sex robot courtroom drama Dolly.
I never thought I’d write the phrase “sex robot courtroom drama”, but there you go. Based on a 2011 short story by Elizabeth Bear, the plot concerns a billionaire killed by a sex robot that then asks for a lawyer to defend its murderous actions.
The real killer robots
Dolly is the latest in a long line of movies featuring killer robots – including HAL in Kubrick’s 2001: A Space Odyssey, and Arnold Schwarzenegger’s T-800 robot in the Terminator series. Indeed, conflict between robots and humans was at the centre of the very first feature-length science fiction film, Fritz Lang’s 1927 classic Metropolis.
But almost all these movies get it wrong. Killer robots won’t be sentient humanoid robots with evil intent. This might make for a dramatic storyline and a box office success, but such technologies are many decades, if not centuries, away.
Indeed, contrary to recent fears, robots may never be sentient.
It’s much simpler technologies we should be worrying about. And these technologies are starting to turn up on the battlefield today in places like Ukraine and Nagorno-Karabakh.
A war transformed
Movies that feature much simpler armed drones, like Angel has Fallen (2019) and Eye in the Sky (2015), paint perhaps the most accurate picture of the real future of killer robots.
On the nightly TV news, we see how modern warfare is being transformed by ever-more autonomous drones, tanks, ships and submarines. These robots are only a little more sophisticated than those you can buy in your local hobby store.
And increasingly, the decisions to identify, track and destroy targets are being handed over to their algorithms.
This is taking the world to a dangerous place, with a host of moral, legal and technical problems. Such weapons will, for example, further upset our troubled geopolitical situation. We already see Turkey emerging as a major drone power.
And such weapons cross a moral red line into a terrible and terrifying world where unaccountable machines decide who lives and who dies.
Robot manufacturers are, however, starting to push back against this future.
A pledge not to weaponise
Last week, six leading robotics companies pledged they would never weaponise their robot platforms. The companies include Boston Dynamics, which makes the Atlas humanoid robot, which can perform an impressive backflip, and the Spot robot dog, which looks like it’s straight out of the Black Mirror TV series.
This isn’t the first time robotics companies have spoken out about this worrying future. Five years ago, I organised an open letter signed by Elon Musk and more than 100 founders of other AI and robot companies calling for the United Nations to regulate the use of killer robots. The letter even knocked the Pope into third place for a global disarmament award.
However, the fact that leading robotics companies are pledging not to weaponise their robot platforms is more virtue signalling than anything else.
We have, for example, already seen third parties mount guns on clones of Boston Dynamics’ Spot robot dog. And such modified robots have proven effective in action. Iran’s top nuclear scientist was assassinated by Israeli agents using a robot machine gun in 2020.
Collective action to safeguard our future
The only way we can safeguard against this terrifying future is if nations collectively take action, as they have with chemical weapons, biological weapons and even nuclear weapons.
Such regulation won’t be perfect, just as the regulation of chemical weapons isn’t perfect. But it will prevent arms companies from openly selling such weapons and thus their proliferation.
Therefore, it’s even more important than a pledge from robotics companies to see the UN Human Rights council has recently unanimously decided to explore the human rights implications of new and emerging technologies like autonomous weapons.
Several dozen nations have already called for the UN to regulate killer robots. The European Parliament, the African Union, the UN Secretary General, Nobel peace laureates, church leaders, politicians and thousands of AI and robotics researchers like myself have all called for regulation.
Australian is not a country that has, so far, supported these calls. But if you want to avoid this Hollywood future, you may want to take it up with your political representative next time you see them.

Toby Walsh does not work for, consult, own shares in or receive funding from any company or organisation that would benefit from this article, and has disclosed no relevant affiliations beyond their academic appointment.
This article appeared in The Conversation.
Suddenly dodging potholes after all this rain? Here’s how drones could help with repairs
Robotic Welding on a Way to Automation
‘Killer robots’ will be nothing like the movies show—here’s where the real threats lie
PACK EXPO Q&A with Brenton Engineering
Tiny particles work together to do big things
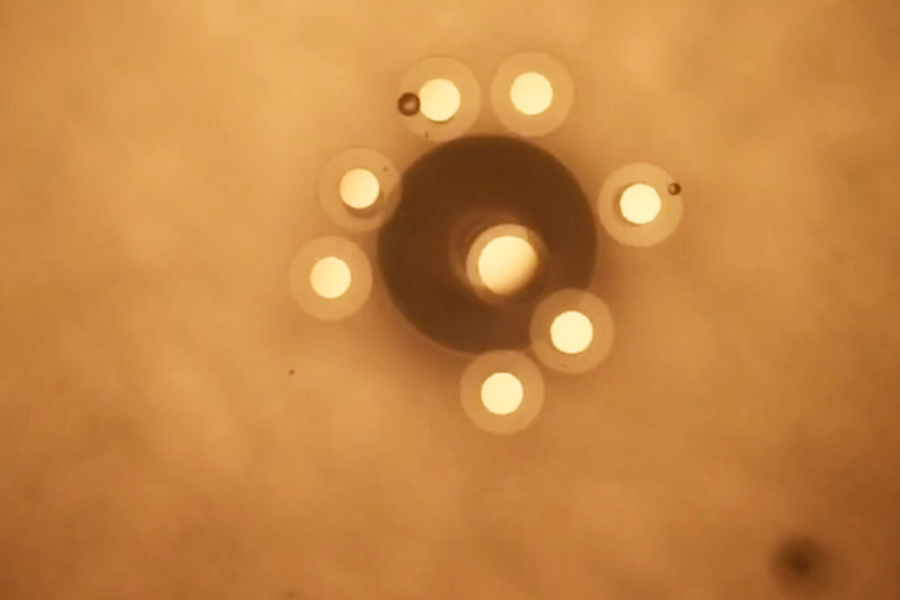
MIT chemical engineers have shown that specialized particles can oscillate together, demonstrating a phenomenon known as emergent behavior. Image: Courtesy of the researchers
By Anne Trafton | MIT News Office
Taking advantage of a phenomenon known as emergent behavior in the microscale, MIT engineers have designed simple microparticles that can collectively generate complex behavior, much the same way that a colony of ants can dig tunnels or collect food.
Working together, the microparticles can generate a beating clock that oscillates at a very low frequency. These oscillations can then be harnessed to power tiny robotic devices, the researchers showed.
“In addition to being interesting from a physics point of view, this behavior can also be translated into an on-board oscillatory electrical signal, which can be very powerful in microrobotic autonomy. There are a lot of electrical components that require such an oscillatory input,” says Jingfan Yang, a recent MIT PhD recipient and one of the lead authors of the new study.
The particles used to create the new oscillator perform a simple chemical reaction that allows the particles to interact with each other through the formation and bursting of tiny gas bubbles. Under the right conditions, these interactions create an oscillator that behaves similar to a ticking clock, beating at intervals of a few seconds.
“We’re trying to look for very simple rules or features that you can encode into relatively simple microrobotic machines, to get them to collectively do very sophisticated tasks,” says Michael Strano, the Carbon P. Dubbs Professor of Chemical Engineering at MIT.
Strano is the senior author of the new paper, which appears in Nature Communications. Along with Yang, Thomas Berrueta, a Northwestern University graduate student advised by Professor Todd Murphey, is a lead author of the study.
Collective behavior
Demonstrations of emergent behavior can be seen throughout the natural world, where colonies of insects such as ants and bees accomplish feats that a single member of the group would never be able to achieve.
“Ants have minuscule brains and they do very simple cognitive tasks, but collectively they can do amazing things. They can forage for food and build these elaborate tunnel structures,” Strano says. “Physicists and engineers like myself want to understand these rules because it means we can make tiny things that collectively do complex tasks.”
In this study, the researchers wanted to design particles that could generate rhythmic movements, or oscillations, with a very low frequency. Until now, building low-frequency micro-oscillators has required sophisticated electronics that are expensive and difficult to design, or specialized materials with complex chemistries.
The simple particles that the researchers designed for this study are discs as small as 100 microns in diameter. The discs, made from a polymer called SU-8, have a platinum patch that can catalyze the breakdown of hydrogen peroxide into water and oxygen.
When the particles are placed at the surface of a droplet of hydrogen peroxide on a flat surface, they tend to travel to the top of the droplet. At this liquid-air interface, they interact with any other particles found there. Each particle produces its own tiny bubble of oxygen, and when two particles come close enough that their bubbles interact, the bubbles pop, propelling the particles away from each other. Then, they begin forming new bubbles, and the cycle repeats over and over.
“One particle by itself stays still and doesn’t do anything interesting, but through teamwork, they can do something pretty amazing and useful, which is actually a difficult thing to achieve at the microscale,” Yang says.
MIT chemical engineers showed that specialized particles can oscillate together, demonstrating a phenomenon known as emergent behavior. At left, two particles oscillate together, and at right, eight particles. Video courtesy of the researchers.
The researchers found that two particles could make a very reliable oscillator, but as more particles were added, the rhythm would get thrown off. However, if they added one particle that was slightly different from the others, that particle could act as a “leader” that reorganized the other particles back into a rhythmic oscillator.
This leader particle is the same size as the other particles but has a slightly larger platinum patch, which enables it to create a larger oxygen bubble. This allows this particle to move to the center of the group, where it coordinates the oscillations of all of the other particles. Using this approach, the researchers found they could create oscillators containing up to at least 11 particles.
Depending on the number of particles, this oscillator beats at a frequency of about 0.1 to 0.3 hertz, which is on the order of the low-frequency oscillators that govern biological functions such as walking and the beating of the heart.
Oscillating current
The researchers also showed that they could use the rhythmic beating of these particles to generate an oscillating electric current. To do that, they swapped out the platinum catalyst for a fuel cell made of platinum and ruthenium or gold. The mechanical oscillation of the particles rhythmically alters the resistance from one end of the fuel cell to the other, which converts the voltage generated by the fuel cell to an oscillating current.
“Like a dripping faucet, catalytic microdiscs floating at a liquid interface use a chemical reaction to drive the periodic growth and release of gas bubbles. The study shows how these oscillatory dynamics can be harnessed for mechanical actuation and electrochemical signaling relevant to microrobotics,” says Kyle Bishop, a professor of chemical engineering at Columbia University, who was not involved in the study.
Generating an oscillating current instead of a constant one could be useful for applications such as powering tiny robots that can walk. The MIT researchers used this approach to show that they could power a microactuator, which was previously used as legs on a tiny walking robot developed by researchers at Cornell University. The original version was powered by a laser that had to be alternately pointed at each set of legs, to manually oscillate the current. The MIT team showed that the on-board oscillating current generated by their particles could drive the cyclic actuation of the microrobotic leg, using a wire to transfer the current from the particles to the actuator.
“It shows that this mechanical oscillation can become an electrical oscillation, and then that electrical oscillation can actually power activities that a robot would do,” Strano says.
One possible application for this kind of system would be to control swarms of tiny autonomous robots that could be used as sensors to monitor water pollution.
The research was funded in part by the U.S. Army Research Office, the U.S. Department of Energy, and the National Science Foundation.