Future of Warehouse Automation – Market worth $27B by 2025
Encouraging robot uptake through Europe’s network of Digital Innovation Hubs
A recent report by the OECD showed that Europe is only capitalising on a fraction (12%) of its digital potential. Most companies limit their digital use to email and internet. Small and Medium Sized Enterprises (SMEs) are particularly slow to integrate digital technologies. The recent Digital Economy and Society Index Report found that “Less than a fifth of companies in the EU-28 are highly digitised“ and that “Use of robots is low on an EU level, with 6.7% of all enterprises using industrial or service robots. The share of large enterprises that use robots is four times higher than the share of SMEs.”
Yet advances in robotics, AI, cloud computing, and big data have the potential to boost productivity and change the industrial landscape.
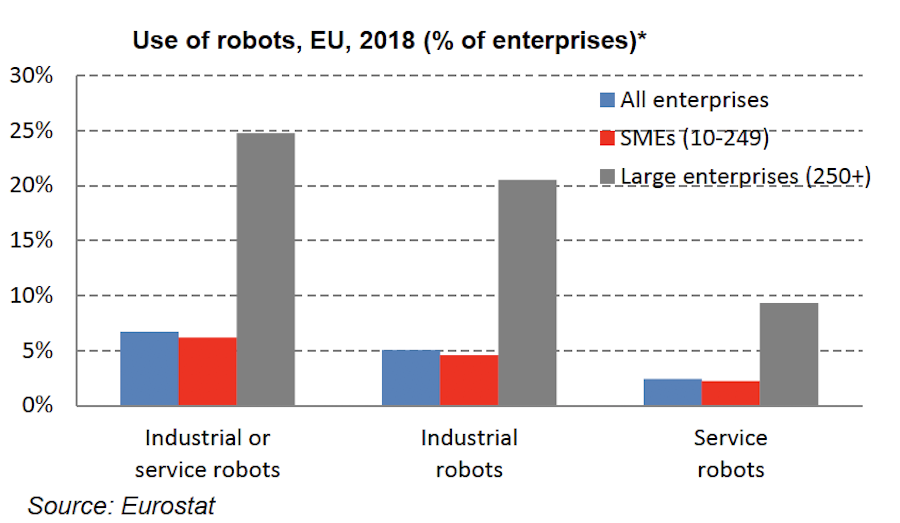
Digital Innovation Hubs
In an effort to increase uptake of digital technologies in companies, the European Commission promised 500M € in 2016, over 5 years, to launch Digital Innovation Hubs (DIHs). DIHs are regional one-stop-shops that help companies access the latest knowledge, expertise, and technology to prototype and test their own digital innovations, network, receive financing advice and market intelligence.
Key to the success of DIHs is to build on core technology infrastructures, so-called Competence Centres (CC), and other existing structures, and link them on a regional level. The idea is that every company should be able to access at least one DIH within their region. This is especially important since most SMEs confess not knowing where to start when it comes to integrating digital technologies into their companies.
“The DIHs funded by the EU Commission can boost digitalisation in Europe in an effective way by supporting both the public sector and SMEs to become more competitive in a global market” says Francesco Ferro, CEO of the Spanish SME PAL Robotics.
The catalogue of Digital Innovation Hubs, hosted by the Joint Research Centre in Sevilla, currently includes over 290 operational hubs across Europe, with 200 more in preparation. The hubs span the full digital landscape, including robotics, artificial intelligence, big data, high-performance computing and cybersecurity, as well as its applications in healthcare, manufacturing, agriculture and food production, maintenance and inspection.
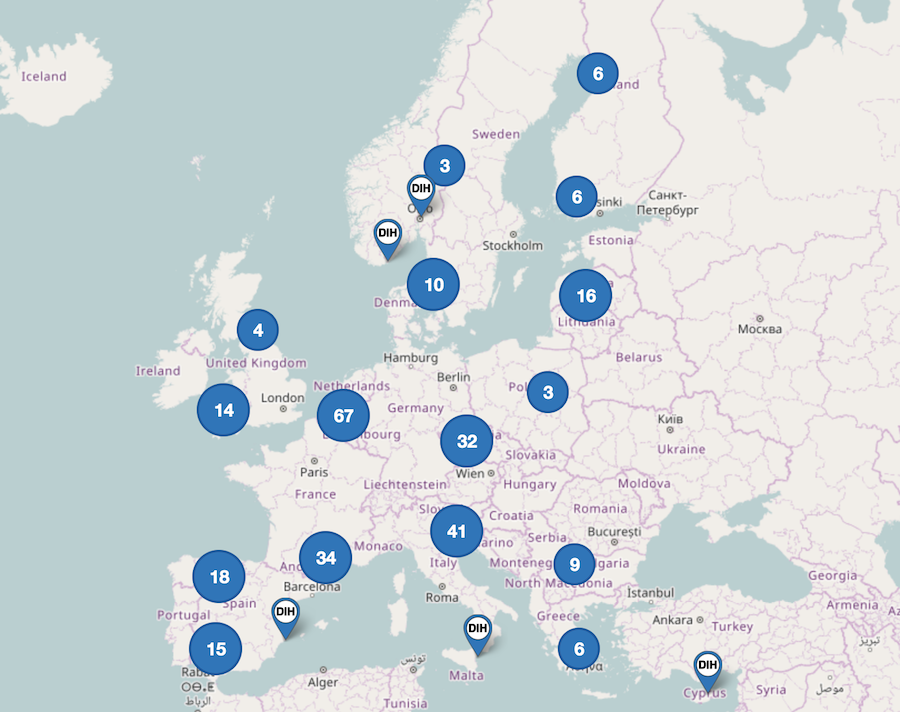
Focus on Robotics
Robotics is central to Europe’s Digital Strategy and 196 of the registered DIHs have identified robotics as an area of expertise. In addition, the European Commission awarded 80M € since 2018 to 5 DIH networks with a robotics focus. Each of these brings together one or two dozen DIHs, with the aim of expanding to even more during the project.
The Horizon 2020 projects Trinity and DIH² focus on Agile production, RIMA promotes the uptake of robotics for inspection and maintenance applications, DIH-HERO facilitates the healthcare robotics sector, and agROBOfood enables the adoption of robotics technologies in the agri-food sector. To coordinate these projects, the Coordination and Support Action (CSA) RODIN started last November with funding of 2M € over five years to cover the whole life-cycle of the network projects. The aim is to present a harmonised interface to the overall landscape of robotics DIHs, coordinate events and calls, share best practice, and connect with similar networks in other areas, such as DIHNET.EU (Next Generation European DIH Network).
Open calls for funding from robotics DIHs
Networks of Networks
DIHNET.EU, the 1M € three-year project launched in November, coordinates the whole network of DIHs in different domains such as robotics, cybersecurity, photonics, advanced manufacturing, artificial intelligence, high-performance-computing, software, big data, agriculture, and more. Think of it as a pan-European network of networks. DIHNET.EU promotes collaboration between DIHs through workshops and events, provides tools and an on-line community platform for DIHs, and is the link to the JRC that maintains the DIH catalogue. The project provides an overview of DIHs to the outside world and helps the European Commission shape DIH-related workshops. To promote the sharing of best practice, DIHNET.EU just launched the Champions Challenge to identify, show and support success stories from mature DIHs that can inspire and guide other DIHs in their developments.
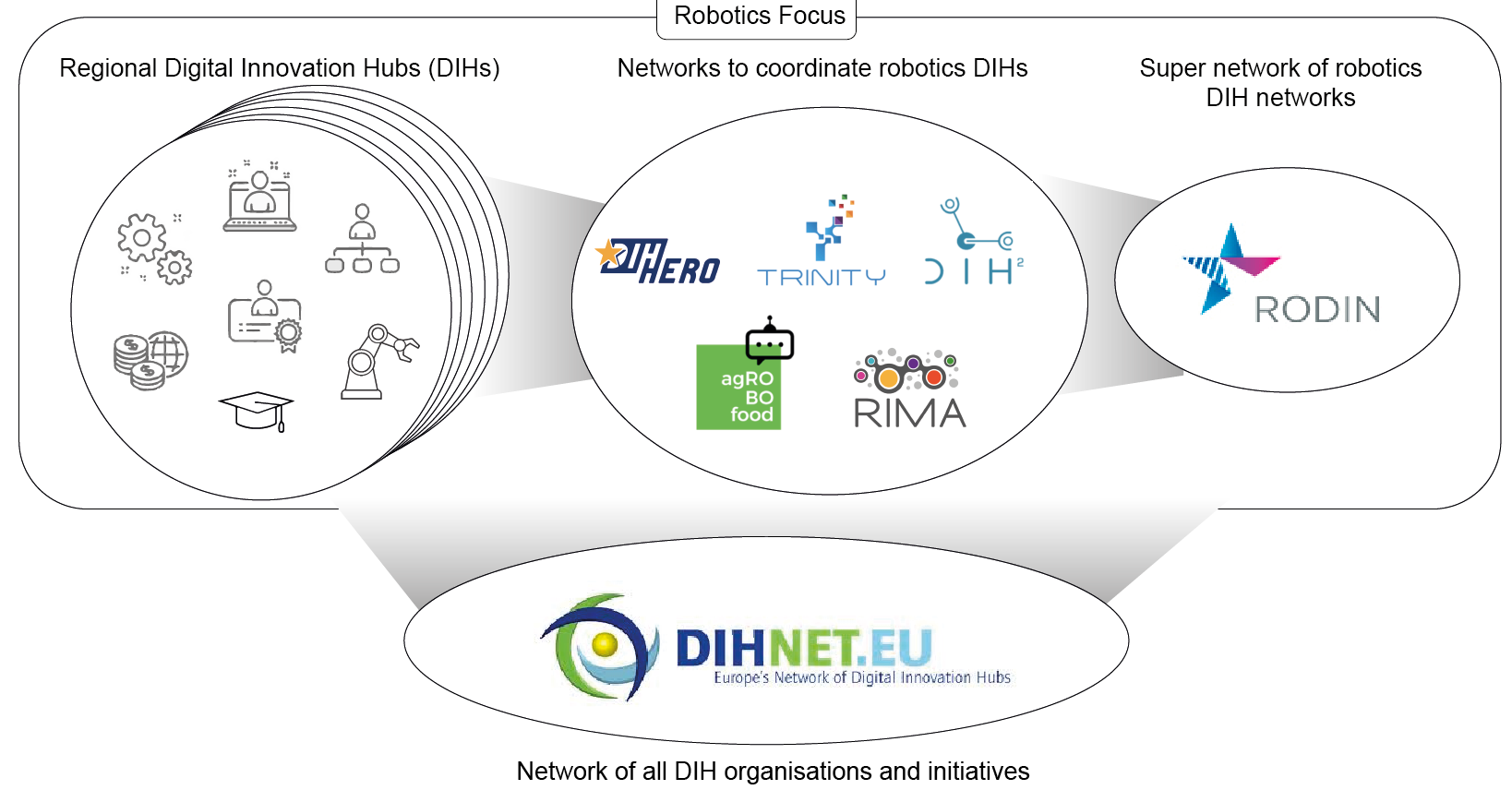
“The DIHNET.EU project is meant to link all relevant initiatives around DIHs together and to create sustainability. Sharing of best practice, creation of awareness and synergies across application sectors, technologies, and regions will help shape a pan-European business ecosystem” says Reinhard Lafrenz, Secretary General of euRobotics.
Robo-Exoticism is the theme for 2019/20 Art, Technology and Culture Colloquiums

Madeline Gannon’s “Robots Are Creatures, Not Things” will be the first work of the Fall 2019-Spring 2020 season of the Colloquiums at UC Berkeley’s Center for New Media at 6pm on Sept 9th.
Dr. Madeline Gannon is a multidisciplinary designer inventing better ways to communicate with machines. In her work, Gannon seeks to blend knowledge from design, robotics, and human-computer interaction to innovate at the intersection of art and technology. Gannon designs her research to engage with wide audiences across scientific and cultural communities: her work has been exhibited at international cultural institutions, published at ACM conferences, and covered by diverse global media outlets. Her 2016 interactive installation, Mimus, even earned her the nickname, “The Robot Whisperer.”
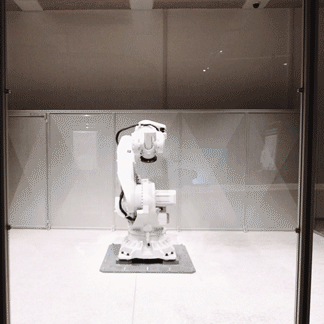
She is three-time World Economic Forum Cultural Leader, and serves as a council member on the World Economic Forum Global Council for IoT, Robotics, & Smart Cities. Gannon holds a Ph.D. in computational design from Carnegie Mellon University, a master’s in architecture from Florida International University, and is a Research Fellow at the Frank-Ratchye STUDIO for Creative Inquiry at Carnegie Mellon University.
Her work “Robots Are Creatures, Not Things” questions how we should coexist with intelligent, autonomous machines. After 50 years of promises and potential, robots are beginning to leave the lab to live in the wild with us. In this lecture, Dr. Madeline Gannon discusses how art and technology are merging to forge new futures for human-robot relations. She shares her work in convincing robots to do things they were never intended to do: from transforming a giant industrial robot into living, breathing mechanical creature, to taming a horde autonomous robots to behave more like a pack of animals. By pushing the boundaries of human-robot interaction, her work shows that robots can not only be useful, but meaningful additions to our everyday lives.
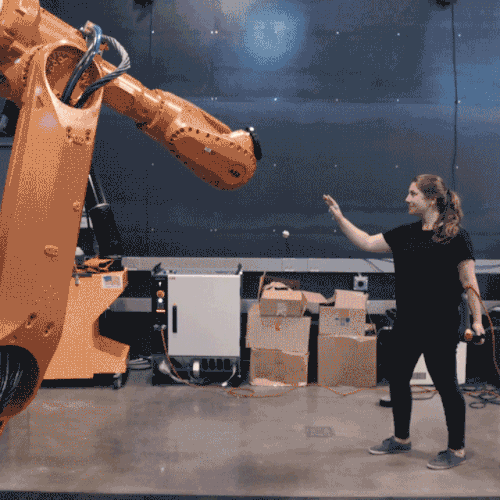
Founded in 1997, the ATC series is an internationally respected forum for creative ideas. The ATC series, free of charge and open to the public, is coordinated by the Berkeley Center for New Media and has presented over 170 leading artists, writers, and critical thinkers who question assumptions and push boundaries at the forefront of art, technology, and culture including: Vito Acconci, Laurie Anderson, Sophie Calle, Bruno Latour, Maya Lin, Doug Aitken, Pierre Huyghe, Miranda July, Billy Kluver, David Byrne, Gary Hill, and Charles Ray.
Current ATC Director is robotics professor Ken Goldberg, who is behind this season’s “Robo-Exotica” theme as well as being the Director of the CITRIS People and Robots Initiative and head of the AutoLab at UC Berkeley.
In 1920, Karl Capek coined the term “robot” in a play about mechanical workers organizing a rebellion to defeat their human overlords. A century later, increasing popularism, inequality, and xenophobia require us to reconsider our assumptions about labor, trade, political stability, and community. At the same time, advances in artificial intelligence and robotics, fueled by corporations and venture capital, challenge our assumptions about the distinctions between humans and machines. To explore potential linkages between these trends, “Robo-Exoticism” characterizes a range of human responses to AI and robots that exaggerate both their negative and positive attributes and reinforce fears, fantasies, and stereotypes.
A Century of Art and Technology in the Bay Area” (essay)
Location:
Monday Evenings, 6:30-8:00pm
Osher Auditorium
BAMPFA, Berkeley, CA
More information
Lectures are free and open to the public. Sign up for the ATC Mailing List!
Global Robotics Revenue to Reach $248.5 Billion by 2025, as the Market for Non-Industrial Robots Maintains Strong Growth, According to Tractica
A Robot Inspired by Worms
Soft robotics breakthrough manages immune response for implanted devices
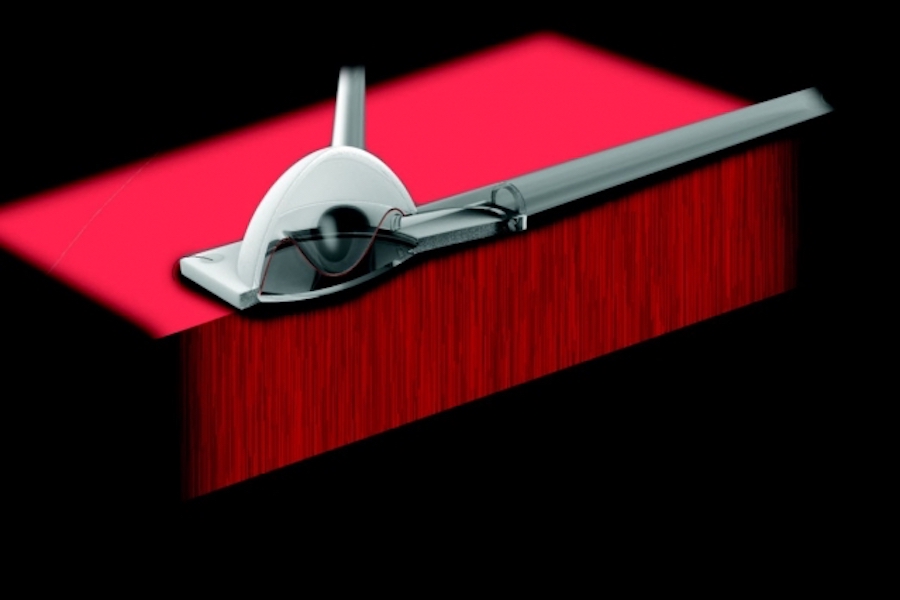
Image courtesy of the researchers.
Researchers from the Institute for Medical Engineering and Science (IMES) at MIT; the National University of Ireland Galway (NUI Galway); and AMBER, the SFI Research Centre for Advanced Materials and BioEngineering Research, recently announced a significant breakthrough in soft robotics that could help patients requiring in-situ (implanted) medical devices such as breast implants, pacemakers, neural probes, glucose biosensors, and drug and cell delivery devices.
The implantable medical devices market is currently estimated at approximately $100 billion, with significant growth potential into the future as new technologies for drug delivery and health monitoring are developed. These devices are not without problems, caused in part by the body’s own protection responses. These complex and unpredictable foreign-body responses impair device function and drastically limit the long-term performance and therapeutic efficacy of these devices.
One such foreign body response is fibrosis, a process whereby a dense fibrous capsule surrounds the implanted device, which can cause device failure or impede its function. Implantable medical devices have various failure rates that can be attributed to fibrosis, ranging from 30-50 percent for implantable pacemakers or 30 percent for mammoplasty prosthetics. In the case of biosensors or drug/cell delivery devices, the dense fibrous capsule which can build up around the implanted device can seriously impede its function, with consequences for the patient and costs to the health care system.
A radical new vision for medical devices to address this problem was published in the internationally respected journal, Science Robotics. The study was led by researchers from NUI Galway, IMES, and the SFI research center AMBER, among others. The research describes the use of soft robotics to modify the body’s response to implanted devices. Soft robots are flexible devices that can be implanted into the body.
The transatlantic partnership of scientists has created a tiny, mechanically actuated soft robotic device known as a dynamic soft reservoir (DSR) that has been shown to significantly reduce the build-up of the fibrous capsule by manipulating the environment at the interface between the device and the body. The device uses mechanical oscillation to modulate how cells respond around the implant. In a bio-inspired design, the DSR can change its shape at a microscope scale through an actuating membrane.
IMES core faculty member, assistant professor at the Department of Mechanical Engineering, and W.M. Keck Career Development Professor in Biomedical Engineering Ellen Roche, the senior co-author of the study, is a former researcher at NUI Galway who won international acclaim in 2017 for her work in creating a soft robotic sleeve to help patients with heart failure. Of this research, Roche says “This study demonstrates how mechanical perturbations of an implant can modulate the host foreign body response. This has vast potential for a range of clinical applications and will hopefully lead to many future collaborative studies between our teams.”
Garry Duffy, professor in anatomy at NUI Galway and AMBER principal investigator, and a senior co-author of the study, adds “We feel the ideas described in this paper could transform future medical devices and how they interact with the body. We are very excited to develop this technology further and to partner with people interested in the potential of soft robotics to better integrate devices for longer use and superior patient outcomes. It’s fantastic to build and continue the collaboration with the Dolan and Roche labs, and to develop a trans-Atlantic network of soft roboticists.”
The first author of the study, Eimear Dolan, lecturer of biomedical engineering at NUI Galway and former researcher in the Roche and Duffy labs at MIT and NUI Galway, says “We are very excited to publish this study, as it describes an innovative approach to modulate the foreign-body response using soft robotics. I recently received a Science Foundation Ireland Royal Society University Research Fellowship to bring this technology forward with a focus on Type 1 diabetes. It is a privilege to work with such a talented multi-disciplinary team, and I look forward to continuing working together.”
PACK EXPO 2019 – Staubli
Hyundai Motor Group Develops Wearable Vest Exoskeleton to Alleviate Burden in Overhead Work
RoboticsTomorrow – Special Tradeshow Coverage<br>PACK EXPO Las Vegas
#293: A Robot to Help with Artificial Insemination, with Zhuoran Zhang
In this episode, Audrow Nash interviews Zhuoran Zhang, PhD student at the University of Toronto, about how robots can be used to assist in artificial insemination. Zhang discusses how precise robotic manipulators can be used to extract a single sperm and how sperm can be evaluated for fitness using computer vision. Zhang also discusses his future plans.
Links