Reprogrammable materials selectively self-assemble
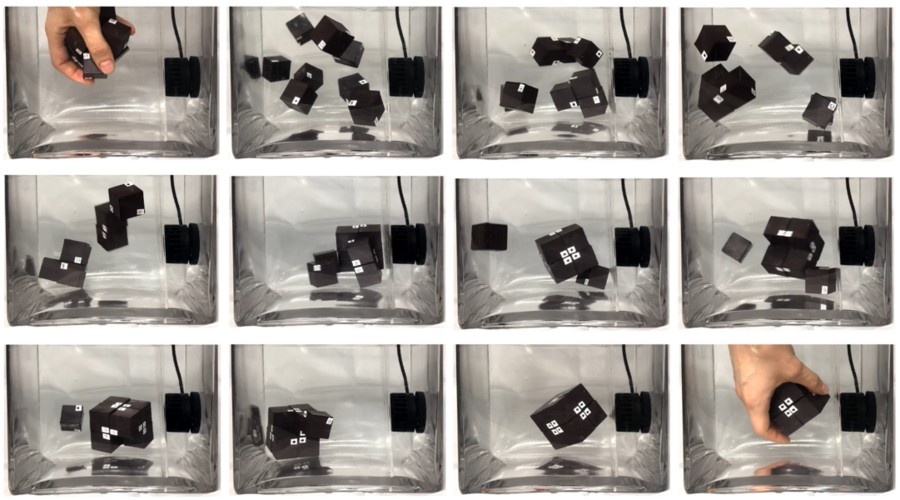
With just a random disturbance that energizes the cubes, they selectively self-assemble into a larger block. Photos courtesy of MIT CSAIL.
By Rachel Gordon | MIT CSAIL
While automated manufacturing is ubiquitous today, it was once a nascent field birthed by inventors such as Oliver Evans, who is credited with creating the first fully automated industrial process, in flour mill he built and gradually automated in the late 1700s. The processes for creating automated structures or machines are still very top-down, requiring humans, factories, or robots to do the assembling and making.
However, the way nature does assembly is ubiquitously bottom-up; animals and plants are self-assembled at a cellular level, relying on proteins to self-fold into target geometries that encode all the different functions that keep us ticking. For a more bio-inspired, bottom-up approach to assembly, then, human-architected materials need to do better on their own. Making them scalable, selective, and reprogrammable in a way that could mimic nature’s versatility means some teething problems, though.
Now, researchers from MIT’s Computer Science and Artificial Intelligence Laboratory (CSAIL) have attempted to get over these growing pains with a new method: introducing magnetically reprogrammable materials that they coat different parts with — like robotic cubes — to let them self-assemble. Key to their process is a way to make these magnetic programs highly selective about what they connect with, enabling robust self-assembly into specific shapes and chosen configurations.
The soft magnetic material coating the researchers used, sourced from inexpensive refrigerator magnets, endows each of the cubes they built with a magnetic signature on each of its faces. The signatures ensure that each face is selectively attractive to only one other face from all the other cubes, in both translation and rotation. All of the cubes — which run for about 23 cents — can be magnetically programmed at a very fine resolution. Once they’re tossed into a water tank (they used eight cubes for a demo), with a totally random disturbance — you could even just shake them in a box — they’ll bump into each other. If they meet the wrong mate, they’ll drop off, but if they find their suitable mate, they’ll attach.
An analogy would be to think of a set of furniture parts that you need to assemble into a chair. Traditionally, you’d need a set of instructions to manually assemble parts into a chair (a top-down approach), but using the researchers’ method, these same parts, once programmed magnetically, would self-assemble into the chair using just a random disturbance that makes them collide. Without the signatures they generate, however, the chair would assemble with its legs in the wrong places.
“This work is a step forward in terms of the resolution, cost, and efficacy with which we can self-assemble particular structures,” says Martin Nisser, a PhD student in MIT’s Department of Electrical Engineering and Computer Science (EECS), an affiliate of CSAIL, and the lead author on a new paper about the system. “Prior work in self-assembly has typically required individual parts to be geometrically dissimilar, just like puzzle pieces, which requires individual fabrication of all the parts. Using magnetic programs, however, we can bulk-manufacture homogeneous parts and program them to acquire specific target structures, and importantly, reprogram them to acquire new shapes later on without having to refabricate the parts anew.”
Using the team’s magnetic plotting machine, one can stick a cube back in the plotter and reprogram it. Every time the plotter touches the material, it creates either a “north”- or “south”-oriented magnetic pixel on the cube’s soft magnetic coating, letting the cubes be repurposed to assemble new target shapes when required. Before plotting, a search algorithm checks each signature for mutual compatibility with all previously programmed signatures to ensure they are selective enough for successful self-assembly.
With self-assembly, you can go the passive or active route. With active assembly, robotic parts modulate their behavior online to locate, position, and bond to their neighbors, and each module needs to be embedded with hardware for the computation, sensing, and actuation required to self-assemble themselves. What’s more, a human or computer is needed in the loop to actively control the actuators embedded in each part to make it move. While active assembly has been successful in reconfiguring a variety of robotic systems, the cost and complexity of the electronics and actuators have been a significant barrier to scaling self-assembling hardware up in numbers and down in size.
With passive methods like these researchers’, there’s no need for embedded actuation and control.
Once programmed and set free under a random disturbance that gives them the energy to collide with one another, they’re on their own to shapeshift, without any guiding intelligence.
If you want a structure built from hundreds or thousands of parts, like a ladder or bridge, for example, you wouldn’t want to manufacture a million uniquely different parts, or to have to re-manufacture them when you need a second structure assembled.
The trick the team used toward this goal lies in the mathematical description of the magnetic signatures, which describes each signature as a 2D matrix of pixels. These matrices ensure that any magnetically programmed parts that shouldn’t connect will interact to produce just as many pixels in attraction as those in repulsion, letting them remain agnostic to all non-mating parts in both translation and rotation.
While the system is currently good enough to do self-assembly using a handful of cubes, the team wants to further develop the mathematical descriptions of the signatures. In particular, they want to leverage design heuristics that would enable assembly with very large numbers of cubes, while avoiding computationally expensive search algorithms.
“Self-assembly processes are ubiquitous in nature, leading to the incredibly complex and beautiful life we see all around us,” says Hod Lipson, the James and Sally Scapa Professor of Innovation at Columbia University, who was not involved in the paper. “But the underpinnings of self-assembly have baffled engineers: How do two proteins destined to join find each other in a soup of billions of other proteins? Lacking the answer, we have been able to self-assemble only relatively simple structures so far, and resort to top-down manufacturing for the rest. This paper goes a long way to answer this question, proposing a new way in which self-assembling building blocks can find each other. Hopefully, this will allow us to begin climbing the ladder of self-assembled complexity.”
Nisser wrote the paper alongside recent EECS graduates Yashaswini Makaram ’21 and Faraz Faruqi SM ’22, both of whom are former CSAIL affiliates; Ryo Suzuki, assistant professor of computer science at the University of Calgary; and MIT associate professor of EECS Stefanie Mueller, who is a CSAIL affiliate. They will present their research at the 2022 IEEE/RSJ International Conference on Intelligent Robots and Systems (IROS 2022).
Developing the world’s first elephant trunk-mimetic robot hand, capable of gripping even fine needles
A reinforcement learning-based four-legged robotic goalkeeper
Swimming with the Substrates: Infrared (IR) Applications
New compact and dexterous robotic finger that can withstand physical impacts
Omron to showcase an interactive experience that combines pick-and-place, materials transport and end-of-line palletizing at PACK EXPO 2022
Battery-free smart devices to harvest ambient energy for IoT
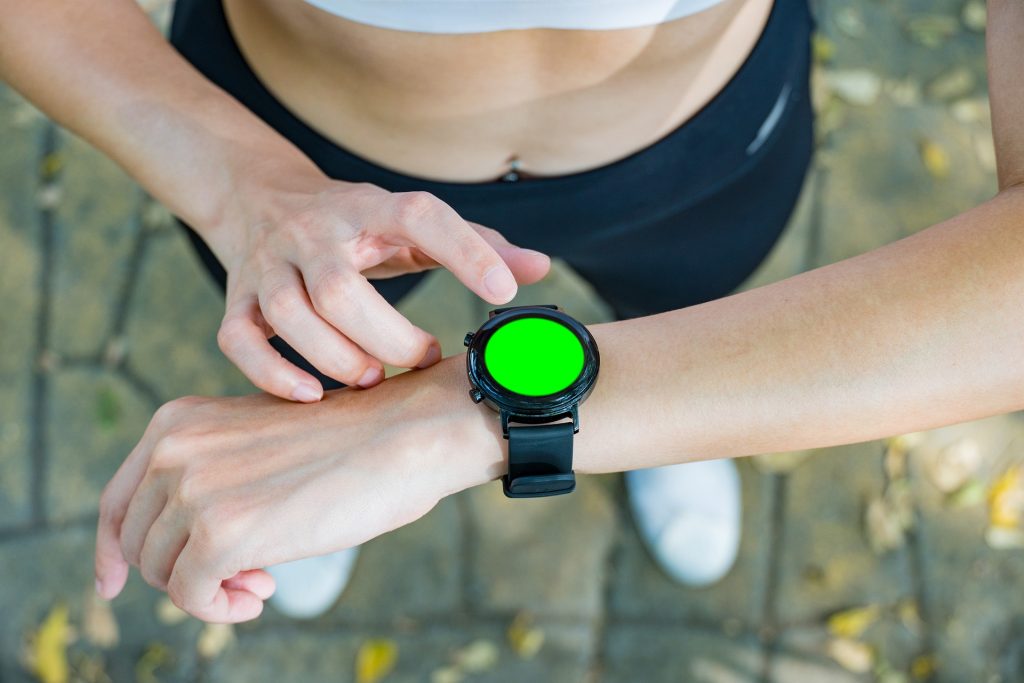
The Internet of Things allows our smart gadgets in the home and wearable technologies like our smart watches to communicate and operate together. Image Credit: Ponchai nakumpa via Pixabay
Tiny internet-connected electronic devices are becoming ubiquitous. The so-called Internet of Things (IoT) allows our smart gadgets in the home and wearable technologies like our smart watches to communicate and operate together. IoT devices are increasingly used across all sorts of industries to drive interconnectivity and smart automation as part of the ‘fourth industrial revolution’.
The fourth industrial revolution builds on already widespread digital technology such as connected devices, artificial intelligence, robotics and 3D printing. It is expected to be a significant factor in revolutionising society, the economy and culture.
These small, autonomous, interconnected and often wireless devices are already playing a key role in our everyday lives by helping to make us more resource and energy-efficient, organised, safe, secure and healthy.
There is a key challenge, however – how to power these tiny devices. The obvious answer is “batteries”. But it is not quite that simple.
Small devices
Many of these devices are too small to use a long-life battery and they are located in remote or hard-to-access locations – for instance in the middle of the ocean tracking a shipping container or at the top of a grain silo, monitoring levels of cereal. These types of locations make servicing some IoT devices extremely challenging and commercially and logistically infeasible.
Mike Hayes, head of ICT for energy efficiency at the Tyndall National Institute in Ireland, summarises the marketplace. ‘It’s projected that we are going to have one trillion sensors in the world by 2025,’ he said, ‘That is one thousand billion sensors.’
That number is not as crazy as it first seems, according to Hayes, who is the coordinator of the Horizon-funded EnABLES project (European Infrastructure Powering the Internet of Things).
If you think about the sensors in the technology someone might carry on their person or have in their car, home, office plus the sensors embedded in the infrastructure around them such as roads and railways, you can see where that number comes from, he explained.
“In the trillion IoT sensor world predicted for 2025, we are going to be throwing over 100 million batteries everyday into landfills unless we significantly extend battery life.”
– Mike Hayes, EnABLES
Battery life
Landfill is not the only environmental concern. We also need to consider where all the material to make the batteries is going to come from. The EnABLES project is calling on the EU and industry leaders to think about battery life from the outset when designing IoT devices to ensure that batteries are not limiting the lifespan of devices.
‘We don’t need the device to last forever,’ said Hayes. ‘The trick is that you need to outlive the application that you’re serving. For example, if you want to monitor a piece of industrial equipment, you probably want it to last for five to 10 years. And in some cases, if you do a regular service every three years anyway, once the battery lasts more than three or four years that’s probably good enough.’
Although many devices have an operational life of more than 10 years, the battery life of wireless sensors is typically only one to two years.
The first step to longer battery life is increasing the energy supplied by batteries. Also, reducing the power consumption of devices will prolong the battery. But EnABLES is going even further.
The project brings together 11 leading European research institutes. With other stakeholders, EnABLES is working to develop innovative ways to harvest tiny ambient energies such as light, heat and vibration.
Harvesting such energies will further extend battery life. The goal is to create self-charging batteries that last longer or ultimately run autonomously.
Energy harvesters
mbient energy harvesters, such as a small vibrational harvester or indoor solar panel, that produce low amounts of power (in the milliwatt range) could significantly extend the battery life of many devices, according to Hayes. These include everyday items like watches, radio frequency identification (RFID) tags, hearing aids, carbon dioxide detectors, and temperature, light and humidity sensors.
EnABLES is also designing the other key technologies needed for tiny IoT devices. Not content with improving energy efficiency, the project is also trying to develop a framework and standardised and interoperable technologies for these devices.
One of the key challenges with autonomously powered IoT tools is power management. The energy source may be intermittent and at very low levels (microwatts), and different methods of harvesting supply different forms of power that require different techniques to convert to electricity.
Steady trickle
Huw Davies, is chief executive officer of Trameto, a company which is developing power management for piezo electric applications. He points out that energy from photovoltaic devices tends to come in a steady trickle, while that from piezoelectric devices, which convert ambient energy from movements (vibrations) into electrical energy, generally comes in bursts.
‘You need a way of storing that energy locally in a store before it is delivered into a load, so you need to have ways of managing that,’ Davies said.
He is the project coordinator of the Horizon-funded HarvestAll project, which has developed an energy management system for ambient energy dubbed OptiJoule.
OptiJoule works with piezoelectric materials, photovoltaics and thermal electric generators. It can function with any of these sources on their own, or with multiple energy harvesting sources at the same time.
The goal is to enable autonomous sensors to be self-sustaining. In principle, it’s quite simple. ‘What we are talking about is ultra-low powered sensors taking some digital measurement,’ said Davies. ‘Temperature, humidity, pressure, whatever it is, with the data from that being delivered into the internet.’
Integrated circuits
The HarvestAll energy management integrated circuit device adjusts to match the different energy harvesters. It takes the different and intermittent energy created by these harvesters and stores it, for instance in a battery or capacitor, and then manages the delivery of a steady output of energy to the sensor.
Similarly to the EnABLES project, the idea is to create standardised technology that will enable the rapid development of long battery life/autonomous IoT devices in Europe and the world.
Davies said that the energy management circuit works completely autonomously and automatically. It is designed so that it can just be plugged into an energy harvester, or combination of harvesters, and a sensor. As a replacement for the battery it has a significant advantage, according to Davies, because ‘It will just work.’
Research in this article was funded by the EU.
This article was originally published in Horizon, the EU Research and Innovation magazine.
New walking robot design could revolutionize how we build things in space
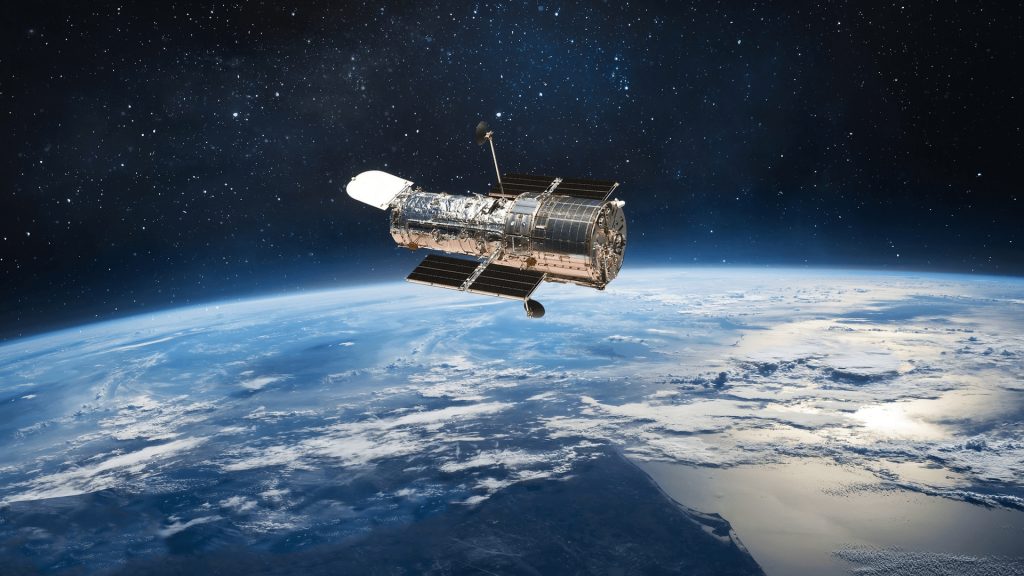
Image: Shutterstock.com
By Suzanna Burgelman, Frontiers science writer
Researchers have designed a state-of-the-art walking robot that could revolutionize large construction projects in space. They tested the feasibility of the robot for the in-space assembly of a 25m Large Aperture Space Telescope. They present their findings in Frontiers in Robotics and AI. A scaled-down prototype of the robot also showed promise for large construction applications on Earth.
Maintenance and servicing of large constructions are nowhere more needed than in space, where the conditions are extreme and human technology has a short lifespan. Extravehicular activities (activities done by an astronaut outside a spacecraft), robotics, and autonomous systems solutions have been useful for servicing and maintenance missions and have helped the space community conduct ground-breaking research on various space missions. Advancements in robotics and autonomous systems facilitate a multitude of in-space services. This includes, but is not limited to, manufacturing, assembly, maintenance, astronomy, earth observation, and debris removal.
With the countless risks involved, only relying on human builders is not enough, and current technologies are becoming outdated.
“We need to introduce sustainable, futuristic technology to support the current and growing orbital ecosystem,” explained corresponding author Manu Nair, PhD candidate at the University of Lincoln.
“As the scale of space missions grows, there is a need for more extensive infrastructures in orbit. Assembly missions in space would hold one of the key responsibilities in meeting the increasing demand.”
In their paper, Nair and his colleagues introduced an innovative, dexterous walking robotic system that can be used for in orbit assembly missions. As a use case, the researchers tested the robot for the assembly of a 25m Large Aperture Space Telescope (LAST).
Assembling telescopes in orbit
Ever since the launch of the Hubble Space Telescope and its successor, the James Webb Space Telescope, the space community has been continuously moving towards deploying newer and larger telescopes with larger apertures (the diameter of the light collecting region).
Assembling such telescopes, such as a 25m LAST, on Earth is not possible with our current launch vehicles due to their limited size. That is why larger telescopes ideally need to be assembled in space (or in orbit).
“The prospect of in-orbit commissioning of a LAST has fueled scientific and commercial interests in deep-space astronomy and Earth observation,” said Nair.
To assemble a telescope of that magnitude in space, we need the right tools: “Although conventional space walking robotic candidates are dexterous, they are constrained in maneuverability. Therefore, it is significant for future in-orbit walking robot designs to incorporate mobility features to offer access to a much larger workspace without compromising the dexterity.”
E-Walker robot
The researchers proposed a seven degrees-of-freedom fully dexterous end-over-end walking robot (a limbed robotic system that can move along a surface to different locations to perform tasks with seven degrees of motion capabilities), or, in short, an E-Walker.
They conducted an in-depth design engineering exercise to test the robot for its capabilities to efficiently assemble a 25m LAST in orbit. The robot was compared to the existing Canadarm2 and the European Robotic Arm on the International Space Station. Additionally, a scaled down prototype for Earth-analog testing was developed and another design engineering exercise performed.
“Our analysis shows that the proposed innovative E-Walker design proves to be versatile and an ideal candidate for future in-orbit missions. The E-Walker would be able to extend the life cycle of a mission by carrying out routine maintenance and servicing missions post assembly, in space” explained Nair.
“The analysis of the scaled-down prototype identifies it to also be an ideal candidate for servicing, maintenance, and assembly operations on Earth, such as carrying out regular maintenance checks on wind turbines.”
Yet a lot remains to be explored. The research was limited to the design engineering analysis of a full-scale and prototype model of the E-Walker. Nair explained: “The E-Walker prototyping work is now in progress at the University of Lincoln; therefore, the experimental verification and validation will be published separately.”
This article was originally published on the Frontiers blog.
A clear definition and classification taxonomy for safety-critical self-adaptive robotic systems
Robotics researchers turn the public’s ideas into ‘robo-fish’ reality
Scared of injections? Try a wearable soft robot to ease aversion to needles
How drones could determine the direction of gravity without accelerometers
BP is Improving Safety and Efficiency by Using Robotics to Inspect Offshore Sites Remotely
A new type of material called a mechanical neural network can learn and change its physical properties to create adaptable, strong structures
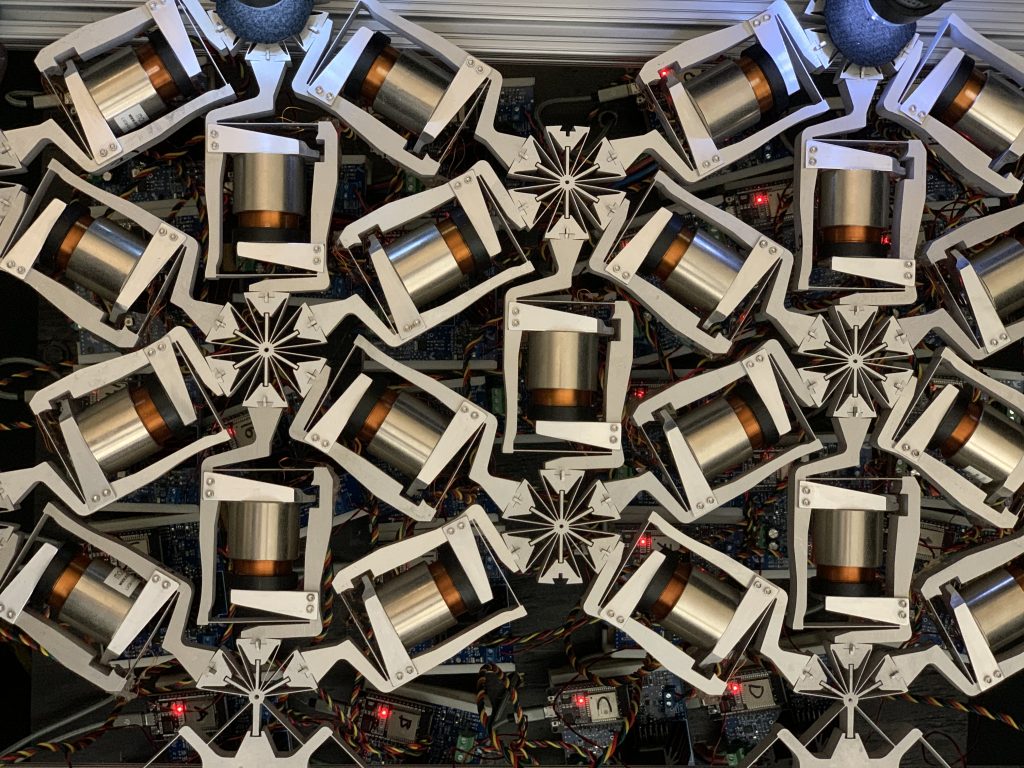
This connection of springs is a new type of material that can change shape and learn new properties. Jonathan Hopkins, CC BY-ND
By Ryan H. Lee (PhD Student in Mechanical and Aerospace Engineering, University of California, Los Angeles)
A new type of material can learn and improve its ability to deal with unexpected forces thanks to a unique lattice structure with connections of variable stiffness, as described in a new paper by my colleagues and me.
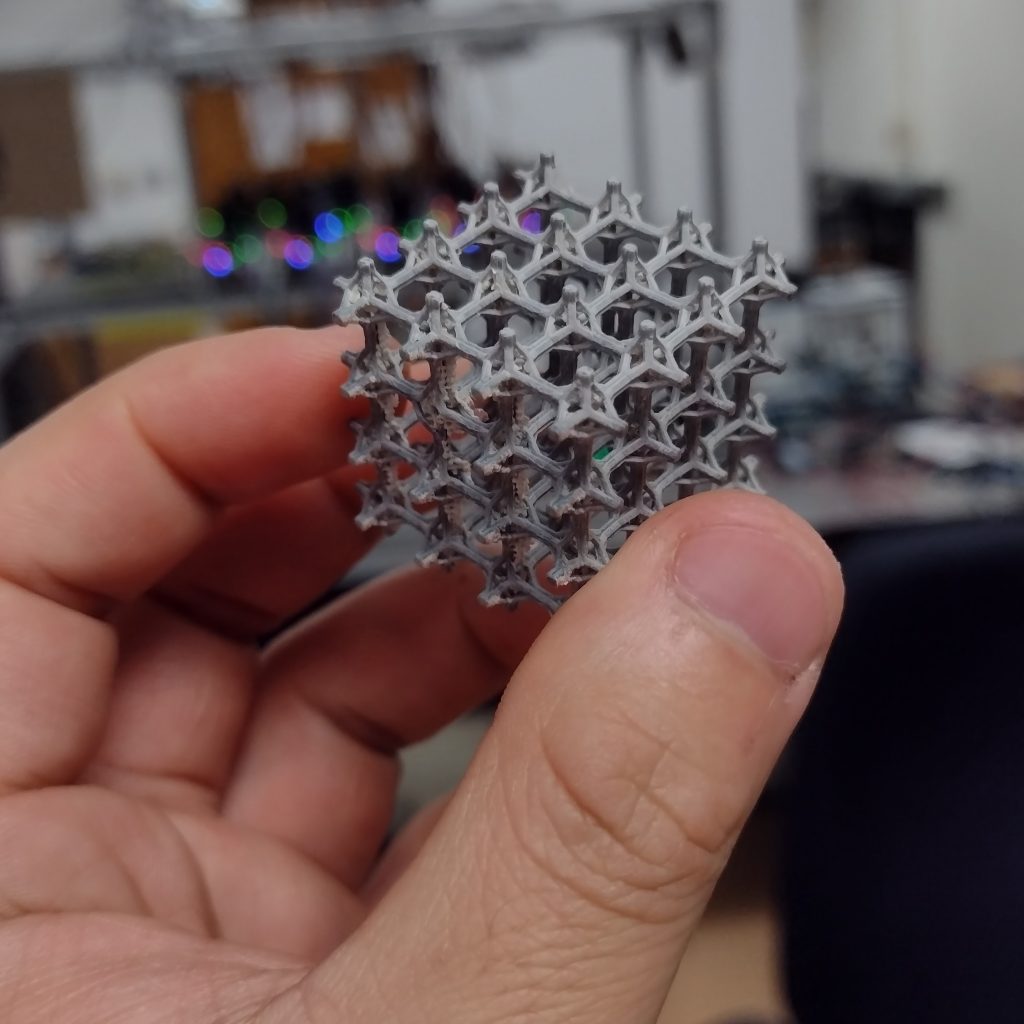
Architected materials – like this 3D lattice – get their properties not from what they are made out of, but from their structure. Ryan Lee, CC BY-ND
The new material is a type of architected material, which gets its properties mainly from the geometry and specific traits of its design rather than what it is made out of. Take hook-and-loop fabric closures like Velcro, for example. It doesn’t matter whether it is made from cotton, plastic or any other substance. As long as one side is a fabric with stiff hooks and the other side has fluffy loops, the material will have the sticky properties of Velcro.
My colleagues and I based our new material’s architecture on that of an artificial neural network – layers of interconnected nodes that can learn to do tasks by changing how much importance, or weight, they place on each connection. We hypothesized that a mechanical lattice with physical nodes could be trained to take on certain mechanical properties by adjusting each connection’s rigidity.
To find out if a mechanical lattice would be able to adopt and maintain new properties – like taking on a new shape or changing directional strength – we started off by building a computer model. We then selected a desired shape for the material as well as input forces and had a computer algorithm tune the tensions of the connections so that the input forces would produce the desired shape. We did this training on 200 different lattice structures and found that a triangular lattice was best at achieving all of the shapes we tested.
Once the many connections are tuned to achieve a set of tasks, the material will continue to react in the desired way. The training is – in a sense – remembered in the structure of the material itself.
We then built a physical prototype lattice with adjustable electromechanical springs arranged in a triangular lattice. The prototype is made of 6-inch connections and is about 2 feet long by 1½ feet wide. And it worked. When the lattice and algorithm worked together, the material was able to learn and change shape in particular ways when subjected to different forces. We call this new material a mechanical neural network.
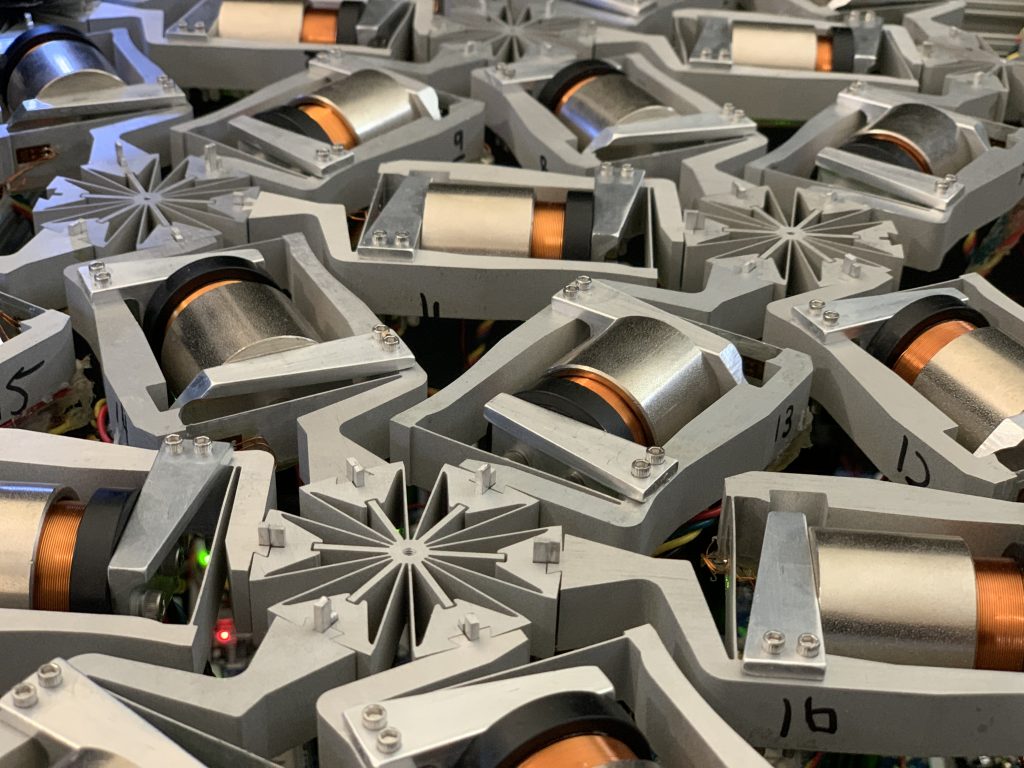
The prototype is 2D, but a 3D version of this material could have many uses. Jonathan Hopkins, CC BY-ND
Why it matters
Besides some living tissues, very few materials can learn to be better at dealing with unanticipated loads. Imagine a plane wing that suddenly catches a gust of wind and is forced in an unanticipated direction. The wing can’t change its design to be stronger in that direction.
The prototype lattice material we designed can adapt to changing or unknown conditions. In a wing, for example, these changes could be the accumulation of internal damage, changes in how the wing is attached to a craft or fluctuating external loads. Every time a wing made out of a mechanical neural network experienced one of these scenarios, it could strengthen and soften its connections to maintain desired attributes like directional strength. Over time, through successive adjustments made by the algorithm, the wing adopts and maintains new properties, adding each behavior to the rest as a sort of muscle memory.
This type of material could have far reaching applications for the longevity and efficiency of built structures. Not only could a wing made of a mechanical neural network material be stronger, it could also be trained to morph into shapes that maximize fuel efficiency in response to changing conditions around it.
What’s still not known
So far, our team has worked only with 2D lattices. But using computer modeling, we predict that 3D lattices would have a much larger capacity for learning and adaptation. This increase is due to the fact that a 3D structure could have tens of times more connections, or springs, that don’t intersect with one another. However, the mechanisms we used in our first model are far too complex to support in a large 3D structure.
What’s next
The material my colleagues and I created is a proof of concept and shows the potential of mechanical neural networks. But to bring this idea into the real world will require figuring out how to make the individual pieces smaller and with precise properties of flex and tension.
We hope new research in the manufacturing of materials at the micron scale, as well as work on new materials with adjustable stiffness, will lead to advances that make powerful smart mechanical neural networks with micron-scale elements and dense 3D connections a ubiquitous reality in the near future.

Ryan Lee has received funding from the Air Force Office of Science Research .
This article appeared in The Conversation.