Making AI models more trustworthy for high-stakes settings
Vote-based model developed for more accurate hand-held object pose estimation
Artificial sense of touch, improved
Researchers develop a novel vote-based model for more accurate hand-held object pose estimation
Taking autonomous driving off-road for mining, search and rescue, exploration
Robot Talk Episode 119 – Robotics for small manufacturers, with Will Kinghorn
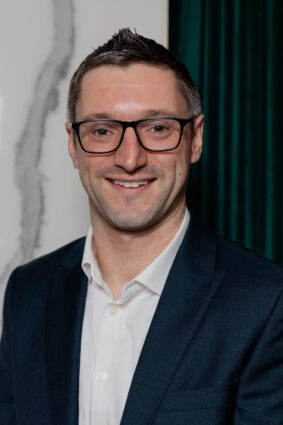
Claire chatted to Will Kinghorn from Made Smarter about how to increase adoption of new tech by small manufacturers.
Will Kinghorn is an automation and robotics specialist for the Made Smarter Adoption Programme in the UK. With a background as a chartered manufacturing engineer in the aerospace industry, Will has extensive experience in developing and implementing automation and robotic solutions. He now works with smaller manufacturing companies, assessing their needs, identifying suitable technologies, and guiding them through the adoption process. Last year he released a book called ‘Digital Transformation in Your Manufacturing Business – A Made Smarter Guide’.
Automate 2025 Q&A with DESTACO
Multi-agent path finding in continuous environments
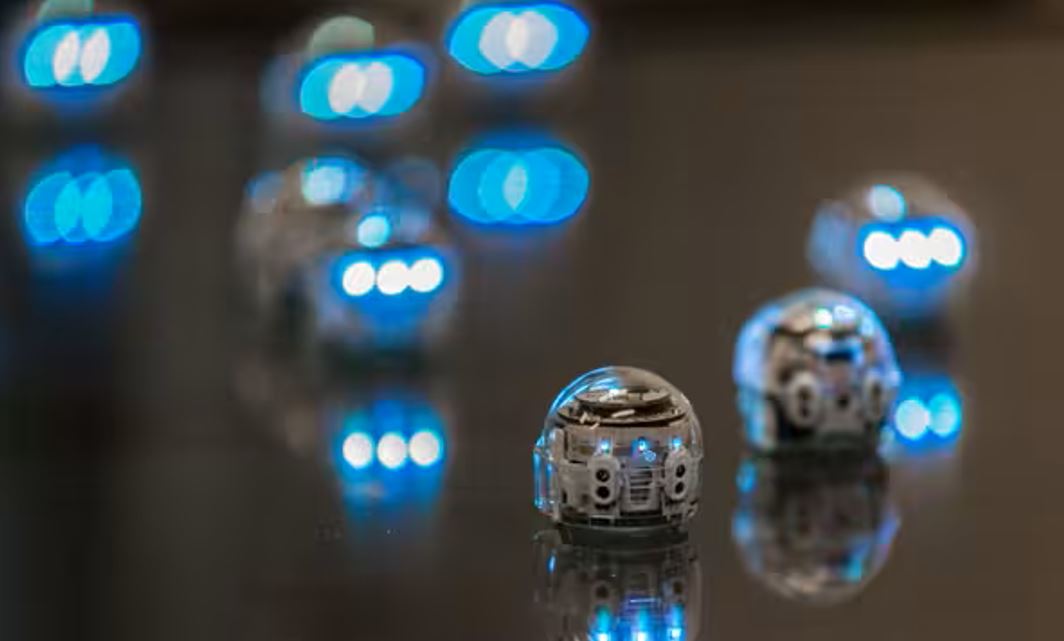
By Kristýna Janovská and Pavel Surynek
Imagine if all of our cars could drive themselves – autonomous driving is becoming possible, but to what extent? To get a vehicle somewhere by itself may not seem so tricky if the route is clear and well defined, but what if there are more cars, each trying to get to a different place? And what if we add pedestrians, animals and other unaccounted for elements? This problem has recently been increasingly studied, and already used in scenarios such as warehouse logistics, where a group of robots move boxes in a warehouse, each with its own goal, but all moving while making sure not to collide and making their routes – paths – as short as possible. But how to formalize such a problem? The answer is MAPF – multi-agent path finding [Silver, 2005].
Multi-agent path finding describes a problem where we have a group of agents – robots, vehicles or even people – who are each trying to get from their starting positions to their goal positions all at once without ever colliding (being in the same position at the same time).
Typically, this problem has been solved on graphs. Graphs are structures that are able to simplify an environment using its focal points and interconnections between them. These points are called vertices and can represent, for example, coordinates. They are connected by edges, which connect neighbouring vertices and represent distances between them.
If however we are trying to solve a real-life scenario, we strive to get as close to simulating reality as possible. Therefore, discrete representation (using a finite number of vertices) may not suffice. But how to search an environment that is continuous, that is, one where there is basically an infinite amount of vertices connected by edges of infinitely small sizes?
This is where something called sampling-based algorithms comes into play. Algorithms such as RRT* [Karaman and Frazzoli, 2011], which we used in our work, randomly select (sample) coordinates in our coordinate space and use them as vertices. The more points that are sampled, the more accurate the representation of the environment is. These vertices are connected to that of their nearest neighbours which minimizes the length of the path from the starting point to the newly sampled point. The path is a sequence of vertices, measured as a sum of the lengths of edges between them.
Figure 1: Two examples of paths connecting starting positions (blue) and goal positions (green) of three agents. Once an obstacle is present, agents plan smooth curved paths around it, successfully avoiding both the obstacle and each other.
We can get a close to optimal path this way, though there is still one problem. Paths created this way are still somewhat bumpy, as the transition between different segments of a path is sharp. If a vehicle was to take this path, it would probably have to turn itself at once when it reaches the end of a segment, as some robotic vacuum cleaners do when moving around. This slows the vehicle or a robot down significantly. A way we can solve this is to take these paths and smooth them, so that the transitions are no longer sharp, but smooth curves. This way, robots or vehicles moving on them can smoothly travel without ever stopping or slowing down significantly when in need of a turn.
Our paper [Janovská and Surynek, 2024] proposed a method for multi-agent path finding in continuous environments, where agents move on sets of smooth paths without colliding. Our algorithm is inspired by the Conflict Based Search (CBS) [Sharon et al., 2014]. Our extension into a continuous space called Continuous-Environment Conflict-Based Search (CE-CBS) works on two levels:
Figure 2: Comparison of paths found with discrete CBS algorithm on a 2D grid (left) and CE-CBS paths in a continuous version of the same environment. Three agents move from blue starting points to green goal points. These experiments are performed in the Robotic Agents Laboratory at Faculty of Information Technology of the Czech Technical University in Prague.
Firstly, each agent searches for a path individually. This is done with the RRT* algorithm as mentioned above. The resulting path is then smoothed using B-spline curves, polynomial piecewise curves applied to vertices of the path. This removes sharp turns and makes the path easier to traverse for a physical agent.
Individual paths are then sent to the higher level of the algorithm, in which paths are compared and conflicts are found. Conflict arises if two agents (which are represented as rigid circular bodies) overlap at any given time. If so, constraints are created to forbid one of the agents from passing through the conflicting space at a time interval during which it was previously present in that space. Both options which constrain one of the agents are tried – a tree of possible constraint settings and their solutions is constructed and expanded upon with each conflict found. When a new constraint is added, this information passes to all agents it concerns and their paths are re-planned so that they avoid the constrained time and space. Then the paths are checked again for validity, and this repeats until a conflict-free solution, which aims to be as short as possible is found.
This way, agents can effectively move without losing speed while turning and without colliding with each other. Although there are environments such as narrow hallways where slowing down or even stopping may be necessary for agents to safely pass, CE-CBS finds solutions in most environments.
This research is supported by the Czech Science Foundation, 22-31346S.
You can read our paper here.
References
- Janovská, K. and Surynek, P. (2024). Multi-agent Path Finding in Continuous Environment, CoRR.
- Sharon, G., Stern, R., Felner, A., and Sturtevant, N. R. (2014). Conflict-based search for optimal multi-agent pathfinding, Artificial Intelligence.
- Karaman, S. and Frazzoli, E. (2011). Sampling-based algorithms for optimal motion planning, CoRR.
- Piegl, L. and Tiller, W. (1996). The NURBS Book, Springer-Verlag, New York, USA, second edition.
- Silver, D. (2005). Cooperative pathfinding, Proceedings of the First Artificial Intelligence and Interactive Digital Entertainment Conference, Marina del Rey, California, USA.
Scientists use virtual reality for fish to teach robots how to swarm
‘Robotability score’ ranks NYC streets for future robot deployment
Forecast demand with precision using advanced AI for SAP IBP
Supply chain leaders know the pain of misaligned inventory. A high-demand product sells out just as a promotion goes live. Meanwhile, pallets of obsolete stock gather dust in the warehouse.
These aren’t just planning hiccups — they’re costly missteps that eat into margins, tie up working capital, and erode customer trust.
But what if your forecasts could finally keep pace with today’s volatility?
Imagine accurately anticipating demand – even when trends shift overnight, new SKUs launch, or external shocks like tariffs, inflation, or weather disrupt the plan.
If you’re already using SAP Integrated Business Planning (IBP), you’re in a strong position to take forecasting further. By layering advanced AI into your SAP IBP workflows, you can dramatically improve forecast accuracy and planning agility—without changing how your teams work.
The forecast gap that’s costing you millions
No matter your industry, the margin for error in demand planning is razor-thin:
- Retailers lose revenue and customer loyalty when popular products sell out, while slow-moving stock ties up capital.
- Distributors face freight chaos and missed service levels during seasonal peaks, unable to predict and respond quickly to shifting volumes.
- CPG brands risk under- or over-producing when promotions or regional shifts aren’t accounted for.
- All planners struggle with cold starts: new or low-history SKUs that traditional models can’t forecast reliably.
These challenges are only intensifying.
Economic volatility, shifting consumer behaviors, tariffs, and climate-related disruptions introduce new variables that make demand harder to predict — and even harder to respond to in time.
Even in robust, enterprise platforms like SAP IBP, traditional forecasting models often rely too heavily on limited historical data and rigid assumptions. They struggle to adapt quickly to new signals or scale across complex planning environments with thousands of SKUs, channels, and geographic regions.
Staying competitive requires more than minor tuning. It calls for intelligent systems that can learn from change, adapt to complexity, and deliver insights at scale.
That’s where the DataRobot Demand Planning App adds value.
It enhances your SAP IBP workflows with AI to provide a more agile, intelligent, and precise forecasting engine.
Add demand planning precision to your SAP IBP
The DataRobot Demand Planning App integrates directly with SAP IBP, infusing your existing planning environment with advanced AI forecasting. It works within your existing workflows, requiring no complex implementation, retraining, or disruption to planning processes.
Here’s how it helps:
- Improve accuracy where it matters most: Confidently forecast volatile demand patterns, including new product launches, promotional spikes, and macroeconomic disruptions.
- Right-size inventory and reduce waste: Align supply chain with actual demand to minimize stockouts and overstocks, freeing up capital and reducing excess carrying costs.
- Drive adoption with seamless integration: Forecasts appear directly within SAP IBP, so planners don’t need to learn a new tool or adjust their process.
- Accelerate impact without overwhelming AI teams: Prebuilt templates automate data prep, model training, and deployment so your data science resources can stay focused on strategic priorities.
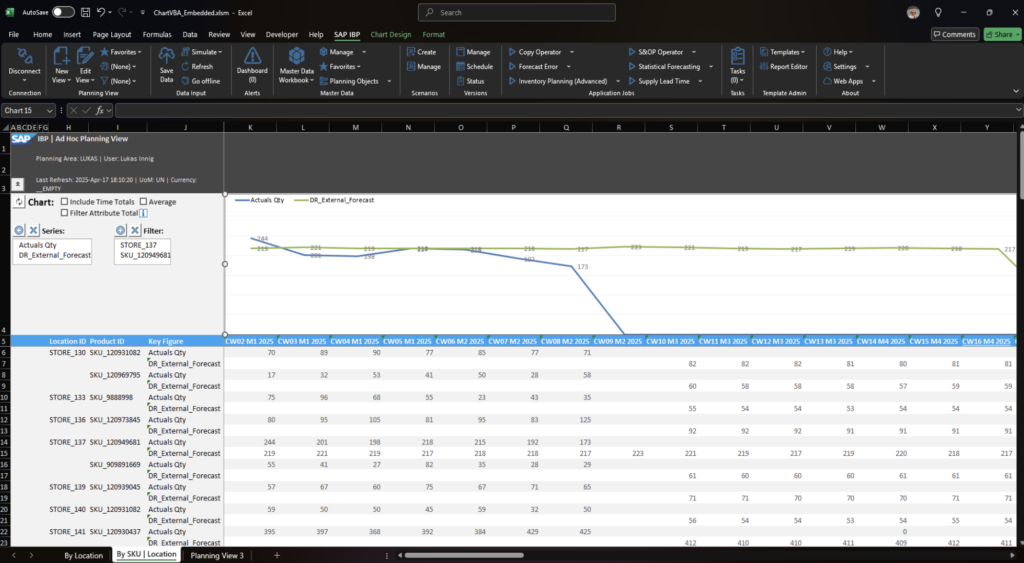
How AI is changing demand planning
Organizations across industries are already using DataRobot for demand planning to deliver measurable ROI and reduce forecast risk :
- Global fashion retailer: Improved forecast accuracy by 9% at the SKU level, saving hundreds of thousands from overstock losses through better inventory alignment.
- European CPG company: Maintained 99% stock availability and reduced held stock by £500K per month, freeing up working capital and improving service levels.
- Fortune 100 retailer: Increased Black Friday forecast accuracy to 95%, saving $2M per week through optimized workforce and inventory planning.
- Fortune 500 tech company: Predicted sell-out volumes four weeks in advance, enabling more strategic inventory placement around retailer promotions.
These aren’t edge cases. They’re evidence that the right AI solution, when integrated into the tools your team already uses, can deliver fast and sustainable value.
What sets the Demand Planning App apart
The DataRobot Demand Planning App wasn’t built to replace SAP IBP. It was built to enhance and extend it. It complements your existing investment with differentiated AI capabilities purpose-built for the real-world complexity of demand planning.
Why it’s different:
- Prebuilt, customizable forecasting templates designed for cold starts, promotions, seasonality, and high-SKU environments help you get started quickly and adjust as needed without starting from scratch.
- The app adapts in near real time, providing flexibility to easily incorporate broader factors from other data sources to identify the impact of emerging trends, geographic variation, and external factors like weather, inflation, or regulatory changes.
- Built-in monitoring, drift detection, version control, and auditability support enterprise-grade accuracy, compliance, and governance.
- Forecast outputs flow directly into SAP IBP, so planners can see and use improved forecasts in the tools they already know, without retraining or manual work.
Four ways to strengthen demand planning in a volatile market
For supply chain and AI leaders looking to reduce risk, drive agility, and future-proof your operations, here are four practical actions to take now:
- Incorporate external signals: Go beyond historical data by integrating real-time signals like inflation, weather, or social sentiment to anticipate shifts in demand.
- Tackle cold starts with proxy data. Use intelligent modeling to accurately forecast demand for new SKUs so they don’t become blind spots in your planning process.
- Align on shared KPIs. Strengthen collaboration by ensuring supply chain, finance, and AI teams are working toward common goals and measurable outcomes.
- Automate what slows you down: Improve accuracy and speed by automating data prep and model deployment using tools designed for scale and repeatability.
Ready to enhance SAP IBP with AI?
In volatile markets, every planning decision carries more weight. Forecasting missteps can ripple across your entire supply chain, eroding trust, tying up cash, and compromising customer satisfaction.
The DataRobot Demand Planning App enhances SAP IBP with advanced AI-driven forecasting that learns, adapts, and scales as fast as your business moves — without disrupting the systems or workflows you rely on.
Want to see what this could look like in your SAP IBP environment? Schedule a demo.
The post Forecast demand with precision using advanced AI for SAP IBP appeared first on DataRobot.